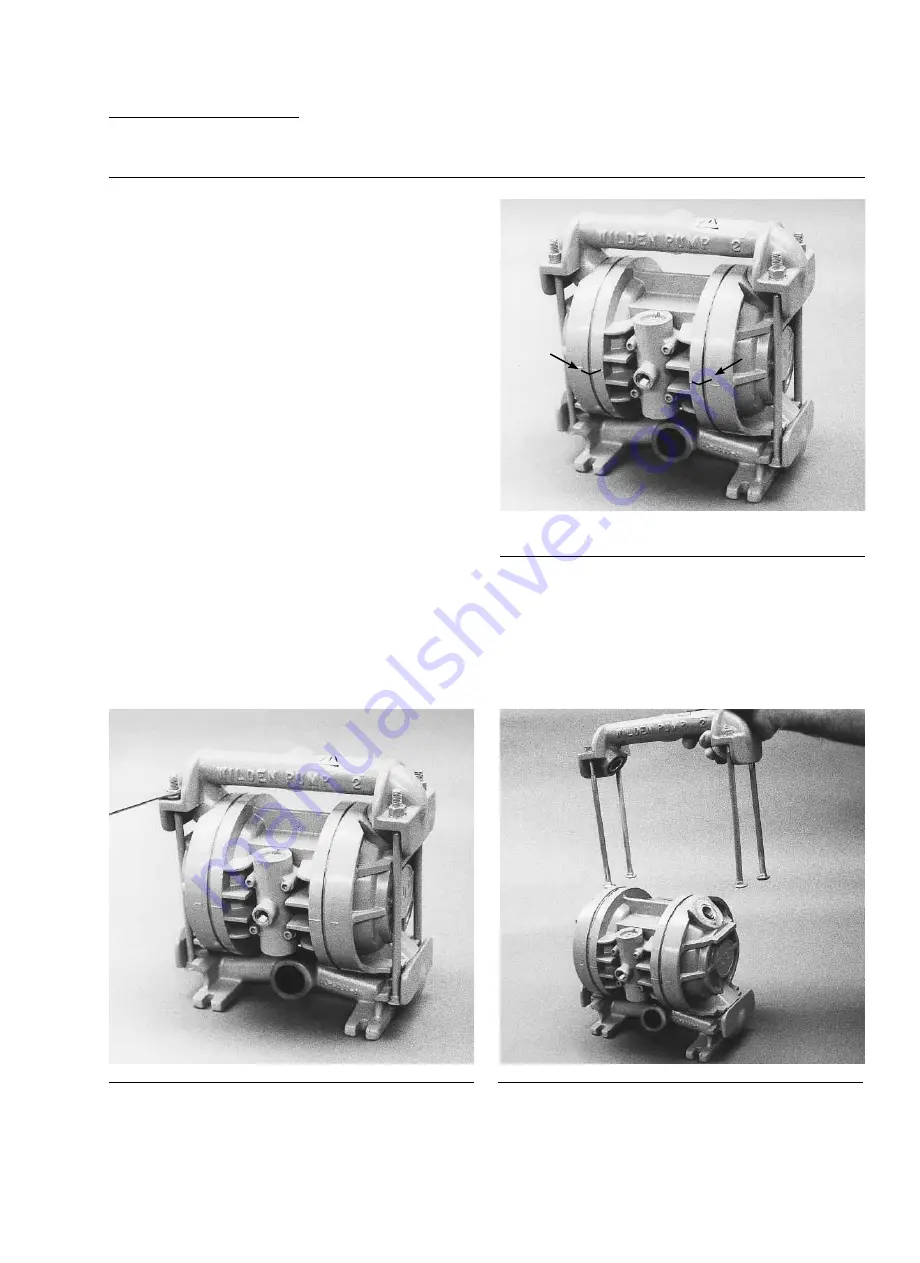
11
SECTION 8A
T2 METAL
DIRECTIONS FOR DISASSEMBLY/REASSEMBLY
Figure 1
Step 2.
Figure 2
Utilizing the 9/16” box wrench, start by removing the four long
carriage bolts that secure the top and bottom manifolds to the
center section.
Step 3.
Figure 3
Remove the top manifold and lift the center section off the inlet
manifold.
CAUTION:
Before any maintenance or repair is attempted, the
compressed air line to the pump should be disconnected and
all air pressure allowed to bleed from the pump. Disconnect
all intake, discharge, and air lines. Drain the pump by turning
it upside down and allowing any fluid to flow into a suitable
container. Be aware of any hazardous effects of contact with
your process fluid.
The Wilden model T2 has a 25 mm (1”) inlet and 19 mm (3/4”)
outlet and is designed for flows up to 132 lpm (35 gpm). The
single-piece center section, consisting of center block and
air chambers, is molded of polypropylene or aluminum. The
air valve is manufactured of brass or high-tech, engineered
thermoplastics. All o-rings used in the pump are of a special
material and shore hardness that should only be replaced with
factory-supplied parts.
TOOLS REQUIRED:
Adjustable Wrench
9/16” Box Wrench
3/4” Box Wrench
Vise equipped with soft jaws (such as plywood, plastic
or other suitable material)
NOTE:
The model used for these instructions incorporates
rubber diaphragms, balls, and seats. Models with PTFE
diaphragms, balls and seats are the same except where
noted.
DISASSEMBLY:
Step 1.
Before starting disassembly, mark a line from each liquid
chamber to its corresponding air chamber. This line will assist
in proper alignment during reassembly.
WIL-10200-E-03
WILDEN PUMP & ENGINEERING, LLC