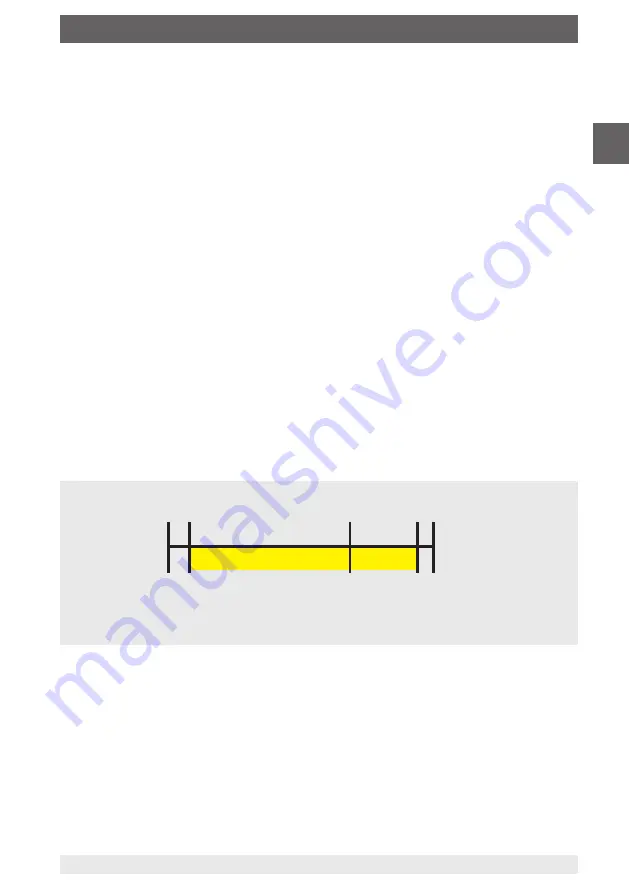
13
WIKA operating instructions, models F2301, F23C1, F23S1, F2303, F2304
ADPR1X914096.01 06/2020 EN/DE
EN
3.9 Signal jump electronics
Compliance with functional safety
An external safety control system independent of the transducer must monitor the safe
functioning of the transducer. The functional test (signal step change) with a signal jump
of 4 mA / 2 V is executed at an interval of 24 hours. The safety control system activates a
relay, thus changing the output signal of the transducer in a defined manner.
If the expected change in the output signal occurs, it can be assumed that the entire
signal path functions correctly. If this does not occur, then it can be concluded that there
is a fault in the signal path.
Moreover, the measuring signal should be checked by the safety control system for the
Min (A) and Max (B) signal value to ensure that any cable break or short-circuit that has
occurred is detected. The default setting of the transducer with current output 4 ... 20 mA
for overload detection is, for example:
With a fixed, set signal jump of, for example, 4 mA, then, in any operating state, the test
cycle can be triggered by activating the test relay. The upper measuring range limit of
20 mA will never be reached and thus the testing of the signal jump is enabled.
Short-circuit (B)
Cable break (A)
[
mA
]
4
3.8
16
20 21
Signals of the signal jump electronics
Overload point
(100 % rated load)
3. Safety
The connection lead of the tension/compression force transducer models
F*3C*.****.15************* and F*3C*.****.21************* must be permanently installed.
No modification must be made to instruments operated in connection with hazardous
areas.