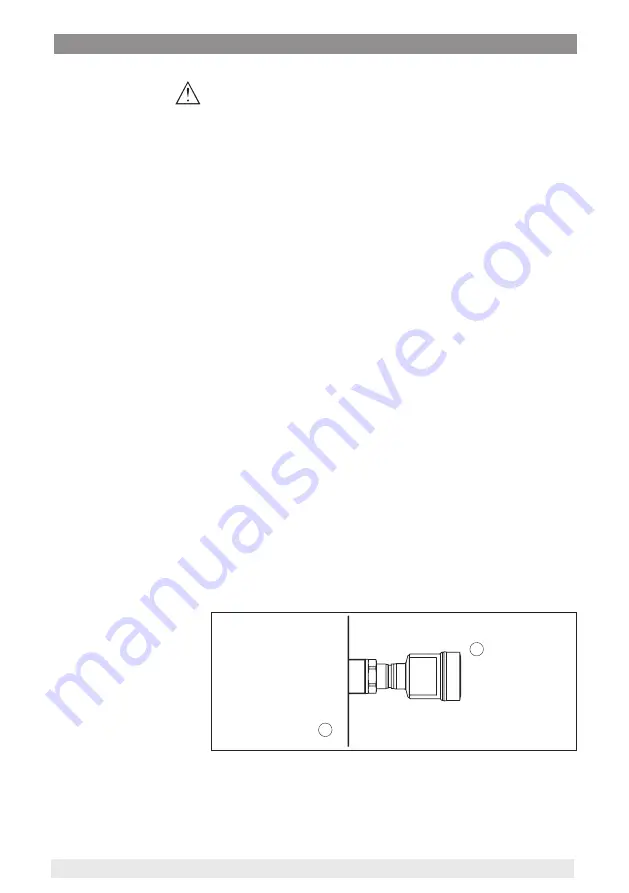
16
4 Mounting
WIKA Operating Instructions - Process pressure transmitter CPT-2x
Warning:
The housing or the electrical connection may not be used for screw-
ing in! Depending on the device version, tightening can cause dam-
age, e. g. to the rotation mechanism of the housing.
If there is strong vibration at the mounting location, the instrument
version with external housing should be used. See chapter "
External
housing
".
The permissible process pressure range is specified by "MWP" (Maxi-
mum Working Pressure) on the type label, see chapter "
Structure
".
The MWP takes the element of the measuring cell and processing
fitting combination with the weakest pressure into consideration and
may applied permanently. The specification refers to a reference
temperature of +20 °C (+68 °F). It also applies when a measuring cell
with a higher measuring range than the permissible pressure range of
the process fitting is installed order-related.
In order to prevent damage to the device, a test pressure may only
exceed the specified MWP briefly by 1.5 times at reference tempera-
ture. The pressure stage of the process fitting as well as the overload
resistance of the measuring cell are taken into consideration here
(see chapter "
Technical Data
").
In addition, a temperature derating of the process fitting, e. g. with
flanges, can limit the permissible process pressure range according
to the respective standard.
The permissible process pressure range is stated on the type label.
The instrument should only be operated with these pressures if the
mounting accessory used also fulfils these values. This should be en-
sured by suitable flanges, welded sockets, tension rings with Clamp
connections, sealings, etc.
Higher process temperatures often mean also higher ambient
temperatures. Make sure that the upper temperature limits stated in
chapter "
Technical data
" for the environment of the electronics hous-
ing and connection cable are not exceeded.
1
2
Fig. 10: Temperature ranges
1 Process temperature
2 Ambient temperature
Vibrations
Permissible process
pressure (MWP) - Device
Permissible process
pressure (MWP) - Mount-
ing accessory
Temperature limits