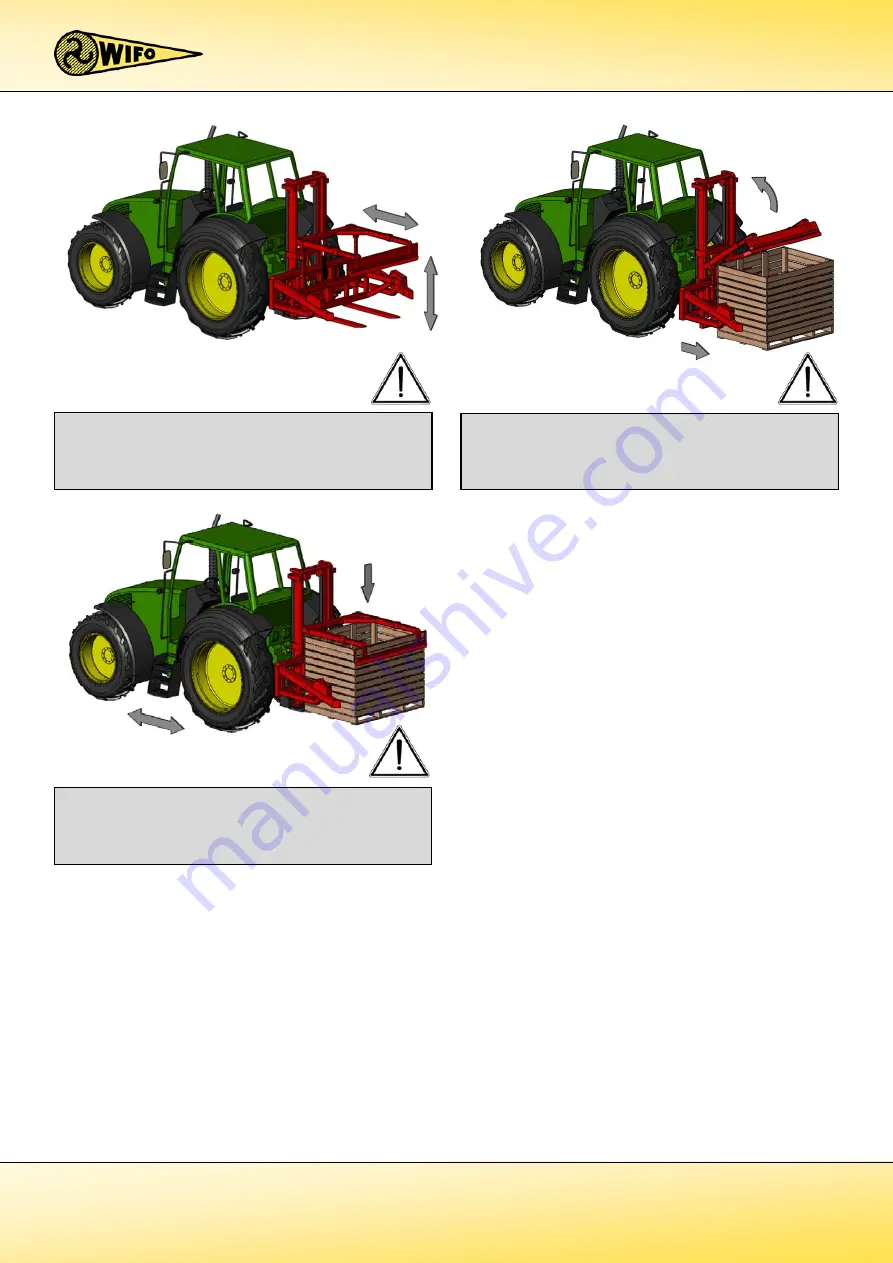
4
Adjust the upper clamp to take account of the height
and depth of the boxes to be tipped.
Raise the upper clamp using the clamping cylinder
before picking up the box with the box rotator.
Distribute the load as evenly as possible over the forks.
Keep the load as low as possible during transportation
to maximise the stability of the lifting vehicle. Boxes
must always be clamped during transportation.