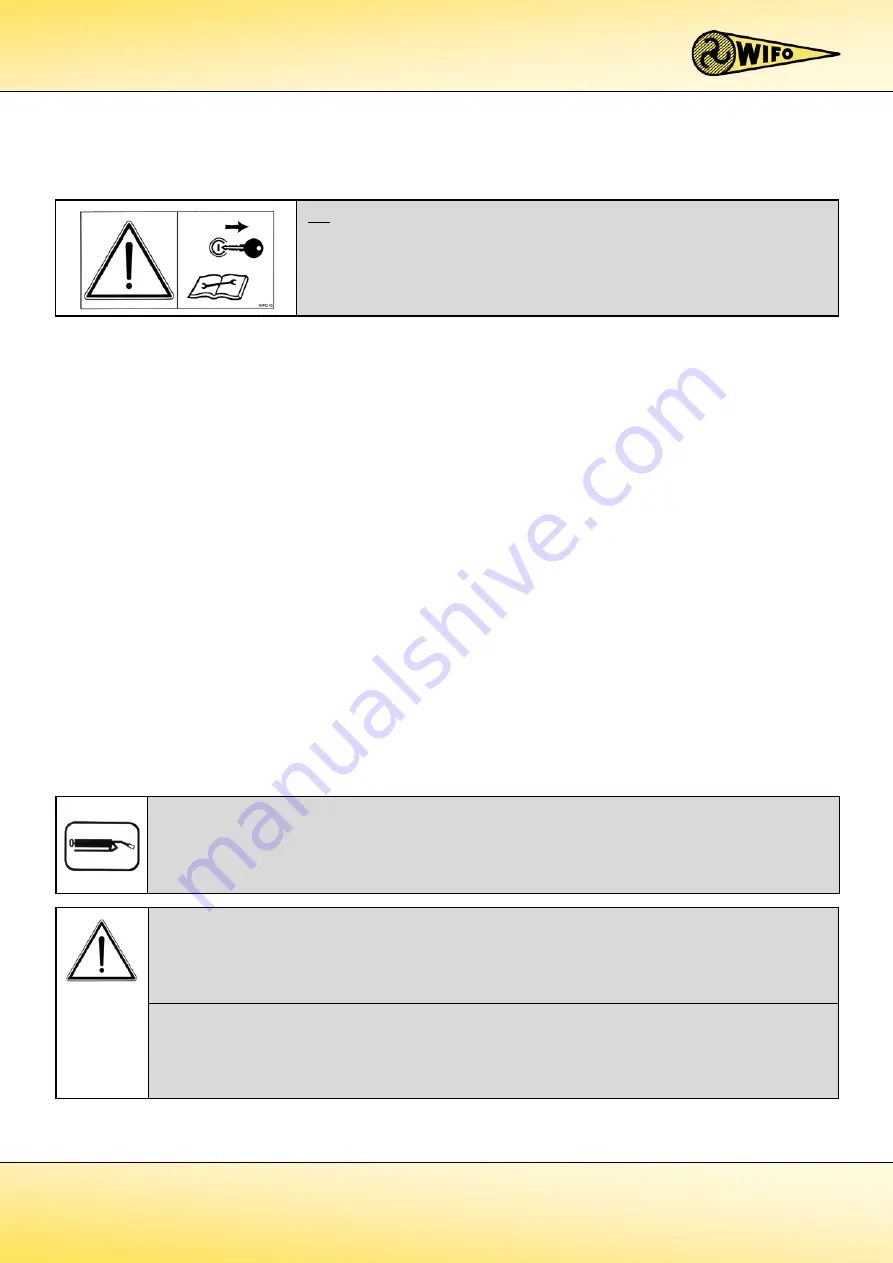
17
3.
Faults and maintenance
Make sure the box rotator is always in the lowest position during maintenance or repairs to the machine. Extra
measures can be taken, e.g. putting the locking pin behind the rotating cylinder and/or disconnecting the hydraulic
hoses
.
3.1
Preventive maintenance and lubrication
After the First 8 working hours:
-
Check the connections and turnbuckles of the hydraulic hoses.
-
Check the bolts of the
locking plate
(100Nm)
and clamping strips
(140Nm).
After every 40 working hours:
-
Check the bolts of the
locking plate
and tighten if necesarry (100Nm).
-
Clean and grease the gear Wheel and gear rack axle. Check both for wear and tear. Replace after excessive
wear and tear.
Regularly check the hydraulic section for any leaks. Never try and search for leaks or stop a leak by hand.
Liquid under high pressure can easily penetrate skin and clothing, and may cause serious injuries. Replace
any damaged hydraulic hoses to prevent them from breaking and any accidents as a result.
Regularly check the oil level of the hydraulic system of your forklift truck / tractor.
NB:
Please read the instructions from the manual prior to any maintenance to the
machine!
Turn off the engine and remove the key from the ignition for the time maintenance
on the machine is carried out!
This sticker shows the position of a grease nipple on the machine. Lubricate the machine after every 10
working hours. Recommended lubricants include SAE 30 oil and Grade 2 grease based on lithium.
Summary of Contents for K55A
Page 2: ......
Page 12: ...10 2 2 K55A and K55C 2 2 1 Parts list Figure 2 2 1 Parts drawing for K55A and K55C...
Page 15: ...13 2 3 SK55A and SK55C 2 3 1 Parts list Figure 2 3 1 Parts drawing for SK55A and SK55C...
Page 22: ...20 Figure 3 3 1 Position of the tapered roller of K55A K55C SK55A and SK55C...
Page 23: ......