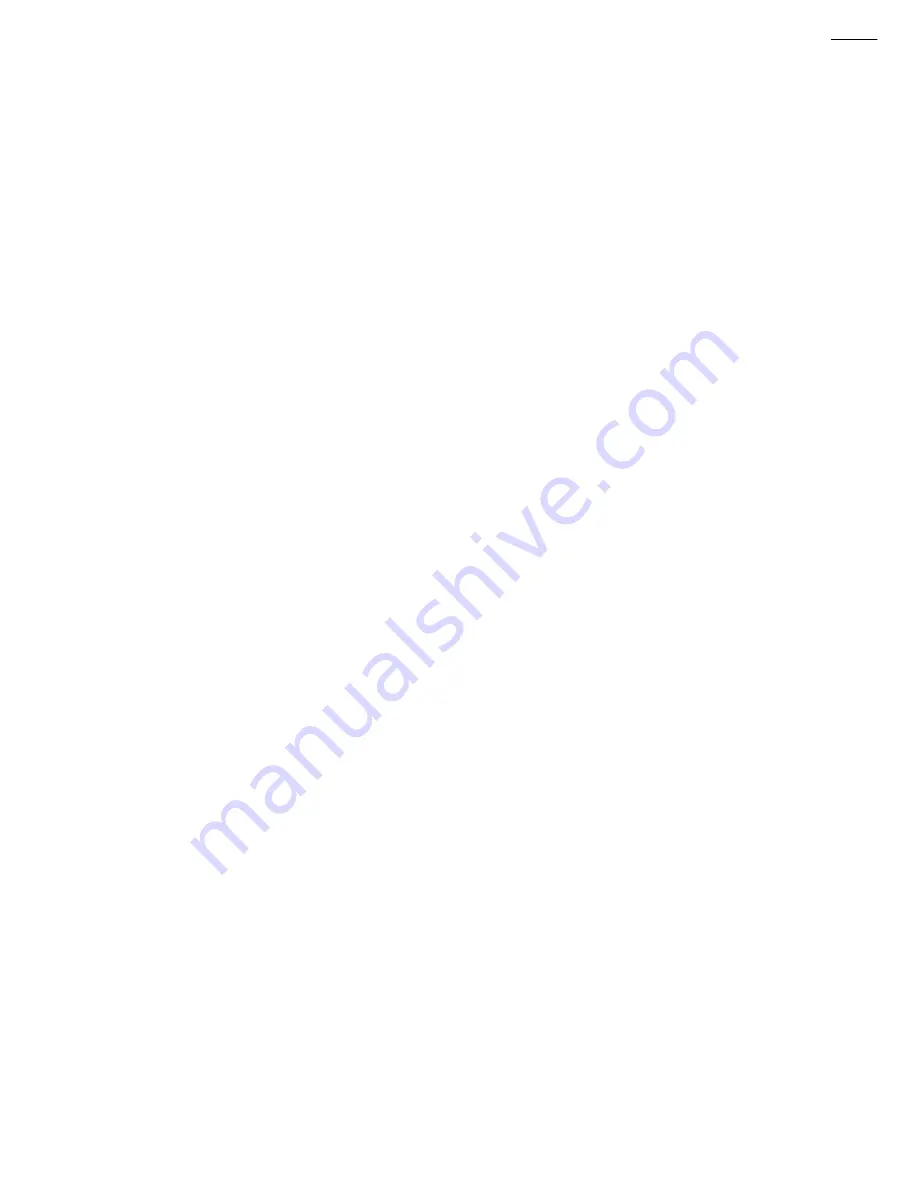
Weldmatic 180i
Model No MC103, Iss A 02/15
3
Burn protection
The welding arc is intense and visibly bright.
Its radiation can damage eyes, penetrate
light-weight clothing, reflect from light-
coloured surfaces, and burn the skin and
eyes. Burns resulting from gas-shielded arcs
resemble acute sunburn, but can be more
severe and painful.
Wear protective clothing – leather or heat
resistant gloves, hat, and safety-toed boots.
Button shirt collar and pocket flaps, and
wear cuffless trousers to avoid entry of
sparks and slag.
Avoid oily or greasy clothing. A spark may
ignite them. Hot metal such as electrode
stubs and work pieces should never be
handled without gloves.
Ear plugs should be worn when welding in
overhead positions or in a confined space.
A hard hat should be worn when others are
working overhead.
Flammable hair preparations should not be
used by persons intending to weld or cut.
Toxic fumes
Adequate ventilation with air is essential.
Severe discomfort, illness or death can
result from fumes, vapours, heat, or oxygen
depletion that welding or cutting may
produce.
NEVER
ventilate with oxygen.
Lead, cadmium, zinc, mercury, and beryllium
bearing and similar materials when welded
or cut may produce harmful concentrations
of toxic fumes. Adequate local exhaust
ventilation must be used, or each person in
the area as well as the operator must wear
an air-supplied respirator. For beryllium, both
must be used.
Metals coated with or containing materials
that emit fumes should not be heated unless
coating is removed from the work surface,
the area is well ventilated, or the operator
wears an air-supplied respirator.
Work in a confined space only while it is
being ventilated and, if necessary, while
wearing air-supplied respirator.
Vapours from chlorinated solvents can be
decomposed by the heat of the arc (or
flame) to form phosgene, a highly toxic
gas, and lung and eye irritating products.
The ultra-violet (radiant) energy of the arc
can also decompose trichlorethylene and
perchlorethylene vapours to form phosgene.
Do not weld or cut where solvent vapours
can be drawn into the welding or cutting
atmosphere or where the radiant energy
can penetrate to atmospheres containing
even minute amounts of trichlorethylene or
percholorethylene.
Fire and explosion prevention
Be aware that flying sparks or falling slag can
pass through cracks, along pipes, through
windows or doors, and through wall or floor
openings, out of sight of the operator. Sparks
and slag can travel up to 10 metres from the arc.
Keep equipment clean and operable, free of
oil, grease, and (in electrical parts) of metallic
particles that can cause short circuits.
If combustibles are present in the work
area, do NOT weld or cut. Move the work if
practicable, to an area free of combustibles.
Avoid paint spray rooms, dip tanks, storage
areas, ventilators. If the work can not be
moved, move combustibles at least 10 metres
away out of reach of sparks and heat; or
protect against ignition with suitable and
snug-fitting fire-resistant covers or shields.
Walls touching combustibles on opposite
sides should not be welded on or cut. Walls,
ceilings, and floor near work should be
protected by heat-resistant covers or shields.