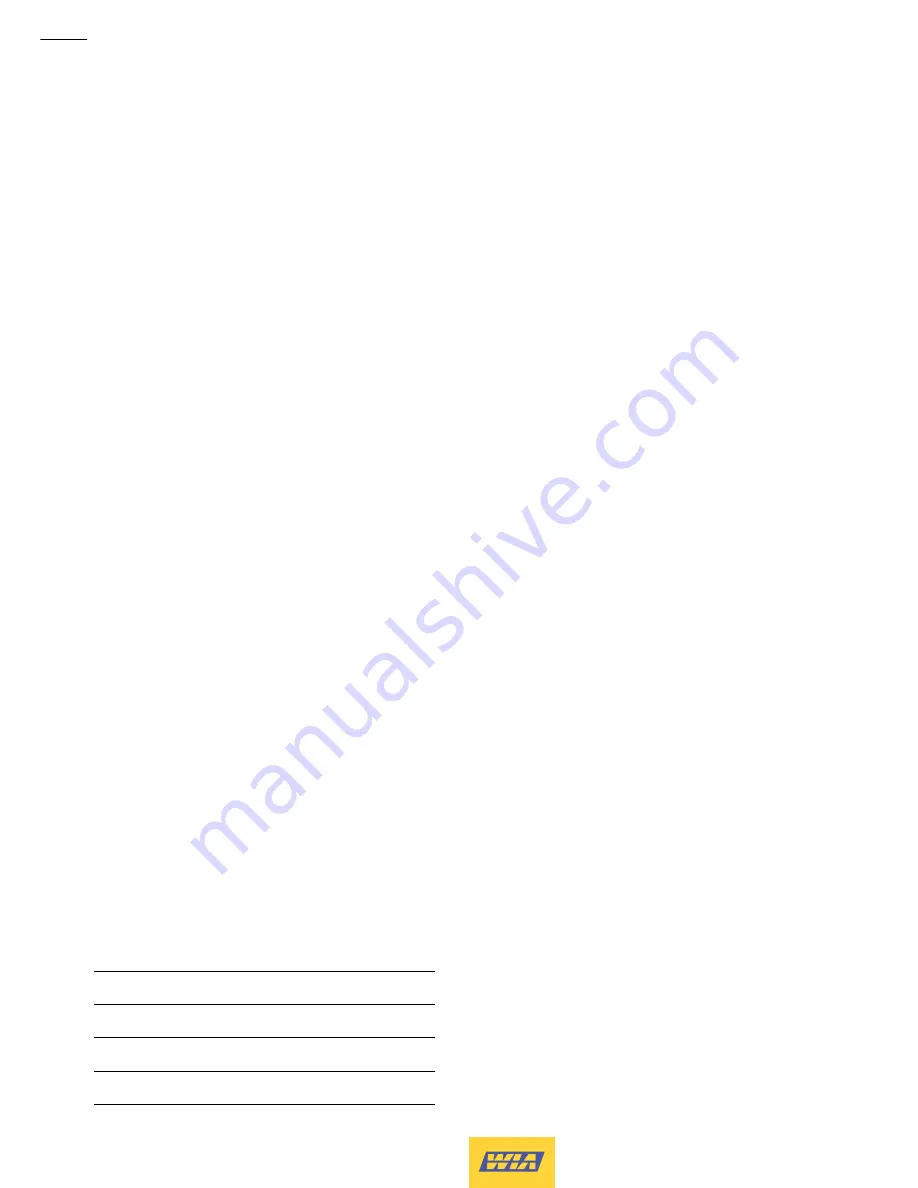
Operators Manual
10
Trusted by the best
Select an appropriate welding current for
the electrode diameter by setting the knob
on the machine front panel. WIA AUSTARC
electrodes will give the best results.
To strike the arc, drag the end of the
electrode along the work piece as if striking
a match. As the arc initiates, lift the electrode
slightly away, aiming to establish an arc
length of approximately 3mm.
As the electrode end is consumed, feed the
electrode into the arc in order to maintain
arc length. As a general rule, the arc should
be held as short as possible while still giving
stable burn off and good weld appearance.
An arc which is too long cause an unwieldy
flow of metal with a rough weld appearance
and reduced penetration. An arc too short
leads to a narrow weld deposit and “stuttery”
arc characteristics, and the electrode is liable
to freeze onto the work piece.
As the solidified weld deposit forms, move
the end of the electrode slowly along
the weld path, aiming to maintain a pool
of molten weld metal behind the arc.
Decreasing this rate of travel will result in a
wider weld deposit, and similarly increasing it
will narrow the weld deposit.
Always fill the crater which tends to form
at the end of a weld deposit, by pausing
momentarily before withdrawing the electrode
to break the arc. Unfilled craters are a point
of weakness, and can lead to weld cracking.
Current Range for General Purpose
Electrodes
Diameter (mm)
Current (Amps)
2.0
40 -60
2.5
60 - 85
3.2
90 - 130
4.0
130 - 180
TIG Welding (GTAW)
Connection for TIG Welding
For TIG Welding, the torch is connected
negative terminal. Figure 4 illustrates the
correct connection of the welding torch
and gas supply. Welding grade Argon is the
shielding gas most commonly used for DC
GTAW welding.
Before first use of the welding torch,
allow gas to purge the torch and hoses for
5 minutes at approximately 10 litres/min. For
welding purposes, the gas flow rate should
be set in the range 2-5 litres/min.
Tungsten electrodes for DC GTAW should
be 1-2% Thoriated or Witstar. This type will
provide the best arc initiation, arc stability and
tip shape retention characteristics. Thoriated
electrodes can be recognised by a red coded
end. The tungsten electrode is ground to
a point, with the grinding marks pointing
towards the tip. For welding currents less
than 20 amps, the included angle of the point
should be 30
o
, for currents greater than 20
amps, the recommended angle is 60
o
. When
set in the torch, the tungsten should protrude
6mm from the ceramic gas nozzle.
TIG Welding
Operation
Connect the Work Clamp to the work piece.
Turn on the power switch located on the rear
panel. Wait approximately 5 seconds as the
unit goes through its initiation sequence.
Use the Weld Mode Selection Switch to
select TIG Mode.
Select an appropriate welding current for the
job by setting the knob on the machine front
panel.
To initiate the arc, lightly touch the tungsten
electrode onto the work piece, then smoothly
lift it away to establish an arc length slightly
longer than the diameter of the electrode.