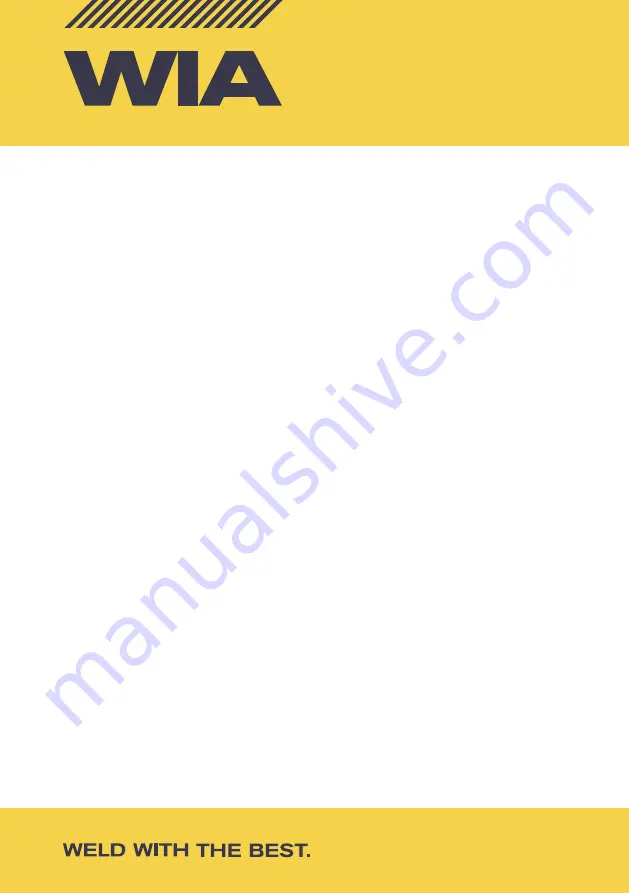
Weldarc 135, 145, 185 | Operator Manual | Model No MC110-0 / MC111-0 / MC112-0
PB
32
WELDING INDUSTRIES
AUSTRALIA
A Division of ITW Australia Pty Ltd
ABN: 63 004 235 063
1300 300 884
Email: [email protected]
WELDWELL
NEW ZEALAND
A Division of ITW New Zealand
NZBN: 9 429 039 833 129
GST NO: 080177186
0800 9353 9355
Email: [email protected]
MC112-40 RevB