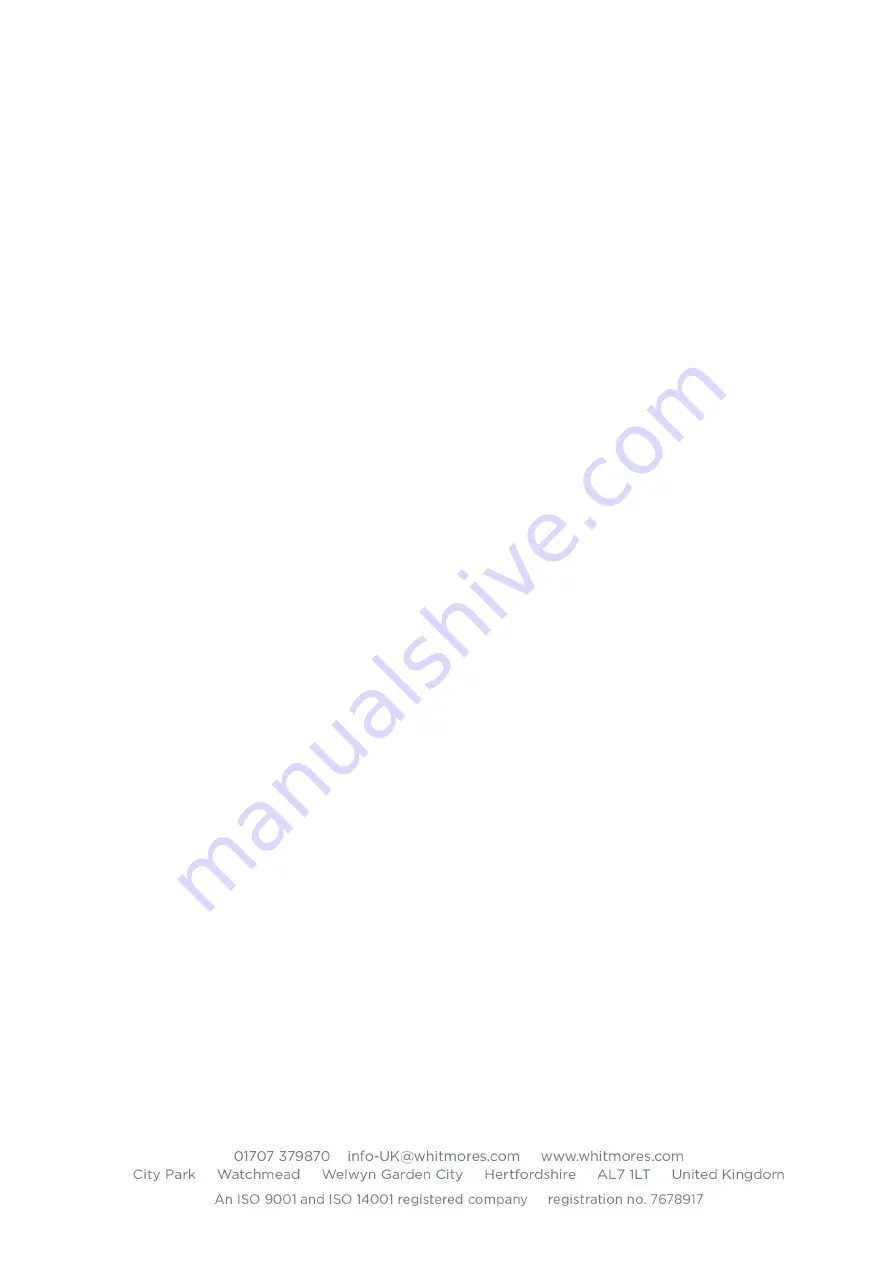
14
7.2
Checking for Leaks
7.2.1
The lubricator should be checked for leaks. With some leaks it will be necessary to take the
leak into consideration in regards to the grease output that was registered.
7.2.2
Leaks on the primary side (i.e. feed hoses or inlet assembly) of the lubricator will cause an
increase in grease output that is not due to the settings of the lubricator.
7.2.3
Tighten any hose clips or nuts / bolts / screws that might be the cause of the leak and / or
replace the faulty part that is causing the leak.
7.3
Cleaning the Lubricator and Surrounding Site
7.3.1
It is at this stage that the lubricator must be cleaned. The reasons are that when the checks
are made, you will be able to register measurements and assess the operations of the
lubricator accurately and carry out the works in a cleaner environment. The reason why
the lubricator must not be cleaned before this stage, is that once it is clean, you will have
removed evidence of the leak.
7.3.2
The whole of the lubricator must be cleaned thoroughly.
7.3.3
The site must be cleared of excess grease.
7.3.4
If oil absorbent granules are being used, the existing, soiled granules should be removed
and replaced with fresh granules. This must be done with extreme caution, if the granules
are allowed to get into the lubricator system via the filling valve, the system may become
blocked or worse the non-return valve can be held open.
7.3.5
The surrounding rail chairs and clips, all rails in the immediate vicinity and the insulator
pots need to be cleaned. The 3rd and 4th rail are required to be cleaned to ensure they
are free of grease and dirt, this is to avoid causing a fire risk and hazardous under footing.
7.3.6
Do not attempt to clean live traction current rails with the current switched on.
7.4
Measuring the Plunger Height
7.4.1
This section is for the initial measurements of the plunger height. The height to be
measured is the distance between the levels of the top of the plunger head, and the crown
of the rail.
7.4.2
The plunger heights must be measured and recorded. The plunger height must be
measured to the nearest 0.25 of a millimetre.
7.4.3
If the lubricator has not used the amount of grease that is required as expected since the
last time that it was maintained.
7.4.4
Check that the plunger height is the same as when the lubricator was last maintained.
7.4.5
You may find that the plunger height has changed due to loose bolts on the pump unit
bracket causing the pump unit to move, check the bolts and tighten if necessary. If
necessary reset the plunger height once all the other checks have been carried out.
7.4.6
If the plunger height is lower than previously although the bolts are all tight, check that the
plunger has not become flat, if so change them, also the plunger may be stuck down due
to defective springs, this will be detected by the plunger operation test later in this
Manual.
7.4.7
If the plunger height has been reset on this visit record the new height.
Summary of Contents for EasiPoint
Page 18: ...18 10Exploded Views of System Elements 10 1 EasiPump Schematic ...
Page 19: ...19 ...
Page 20: ...20 ...
Page 21: ...21 10 2 EasiPoint Schematic ...
Page 22: ...22 ...
Page 23: ...23 10 3 Blades ...
Page 24: ...24 ...
Page 25: ...25 10 4 Reservoirs ...
Page 26: ...26 ...
Page 27: ...27 ...