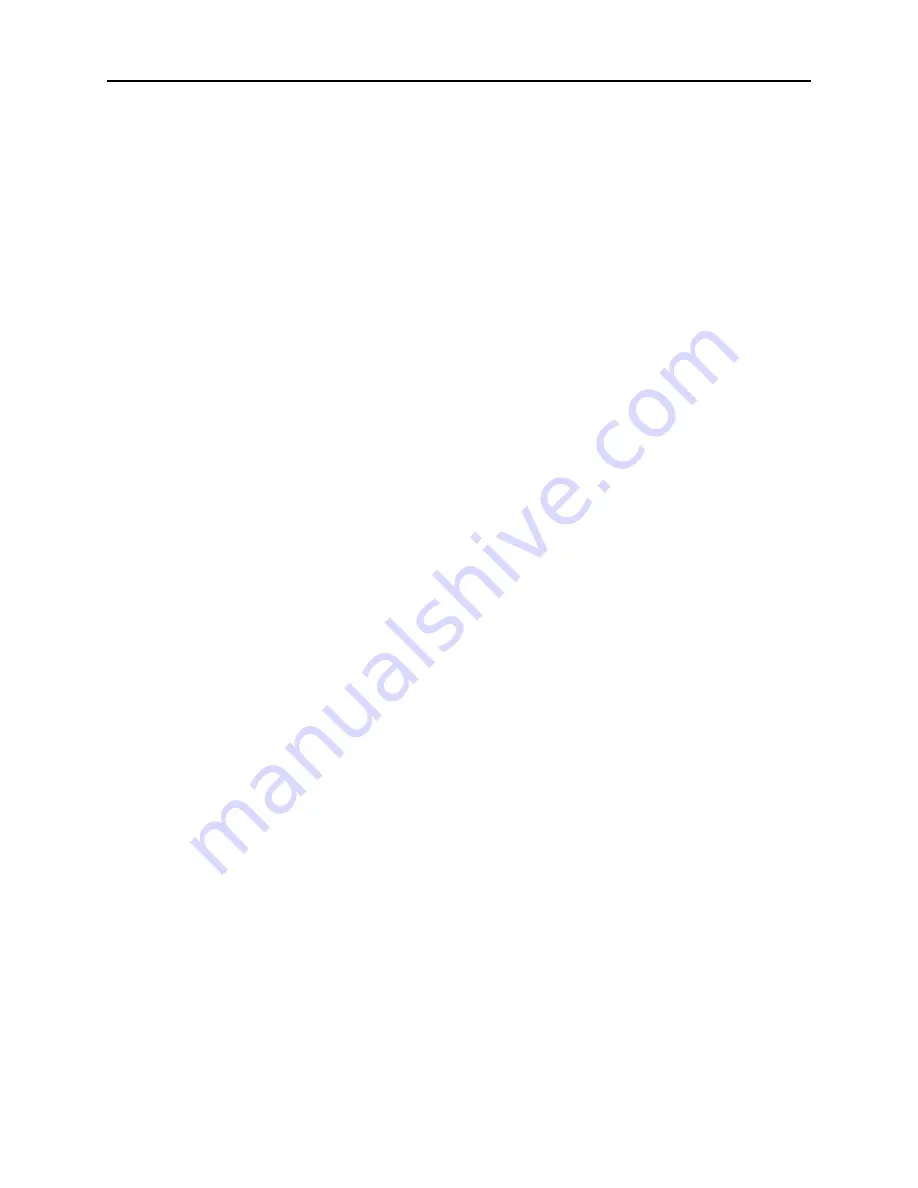
61
20 W Stereo Audio Amplifier
– Crimp the green wire on pin 4 of V1. Solder in place. When soldering, make sure the heat-
shrink tubing is pushed back on the wire so it is not near the soldering point. If the heat-
shrink tubing gets hot it will be very difficult to slide into position later.
– Crimp the brown wire on pin 5 of V1. Solder in place, keeping in mind the caution about
the heat-shrink tubing.
– Slide the heat-shrink tubing into position at the base of the socket. Apply a stream of hot
air to shrink the tubing over the pins. Be careful to not apply too much heat.
– Replace the standoff removed from the V1 socket. The screws should be finger-tight.
Remember to include the lockwasher on the component side of the board. The heater leads
should straddle the standoff.
– Twist the wires together and route to socket V2 (see Figure 5.2
d
for placement). The wires
should be placed at socket-level. In this way they will be resting against the chassis when
the board is inserted in the chassis. Do not dress the wires against the PWB as this may
increase hum in the output of the amplifier.
– Trim the wire lengths as needed to comfortably reach V2. As before, slip a piece of heat-
shrink tubing over each wire. Crimp the brown wire on pin 5, and then crimp the green on
pin 4. Do not solder.
– Cut one 9-inch piece of #22 green wire and one 9-inch piece of #22 brown wire. Slip the
brown wire through the heat-shrink tubing on the lead already connected to pin 5 of V2.
Route the wire to the pin and crimp in place. Solder, keeping the heat-shrink tubing away
from the hot wires and the soldering iron. Slip the green wire through the heat-shrink
tubing on the lead already connected to pin 4 of V2. Route the wire to the pin and crimp in
place. Solder, keeping the heat-shrink tubing away from the hot wires and the soldering
iron.
– Slide the heat-shrink tubing into position at the base of the socket. Apply a stream of hot
air to shrink the tubing over the pins. Be careful to not use too much heat.
– Replace the standoff removed from the V2 socket. The screws should be finger-tight.
Remember to include the lockwasher on the component side of the board. The heater leads
should straddle the standoff.
Summary of Contents for J C Whitaker 20 W Stereo Audio Amplifier
Page 1: ...20 W Stereo Amplifier WhitakerAudio 20 W Stereo Audio Amplifier...
Page 10: ...10 WhitakerAudio Figure 1 1 b...
Page 14: ...14 WhitakerAudio Figure 1 2 The preamplifier power supply PWB...
Page 20: ...20 WhitakerAudio Figure 1 4 Power management expansion circuit for the 40 W Stereo Amplifier...
Page 37: ...37 20 W Stereo Audio Amplifier Figure 3 1 Component layout for the Amplifier PWB 1 right board...
Page 39: ...39 20 W Stereo Audio Amplifier Figure 3 2 Rectifier PWB component layout...
Page 42: ...42 WhitakerAudio Figure 3 3 Component layout for the Amplifier PWB 2 left board...
Page 46: ...46 WhitakerAudio Figure 3 5 Layout of the preamplifier power supply PWB...
Page 86: ...86 WhitakerAudio Figure 5 7 Power management expansion PWB a component side b foil side a b...
Page 135: ...135 20 W Stereo Audio Amplifier Figure 5 15 Chassis view of the 20 W Stereo amplifier...
Page 179: ......
Page 180: ...20 W Stereo Amplifier WhitakerAudio 20 W Stereo Audio Amplifier...
Page 184: ...184 WhitakerAudio Figure 1 1 Completed cable assembly...