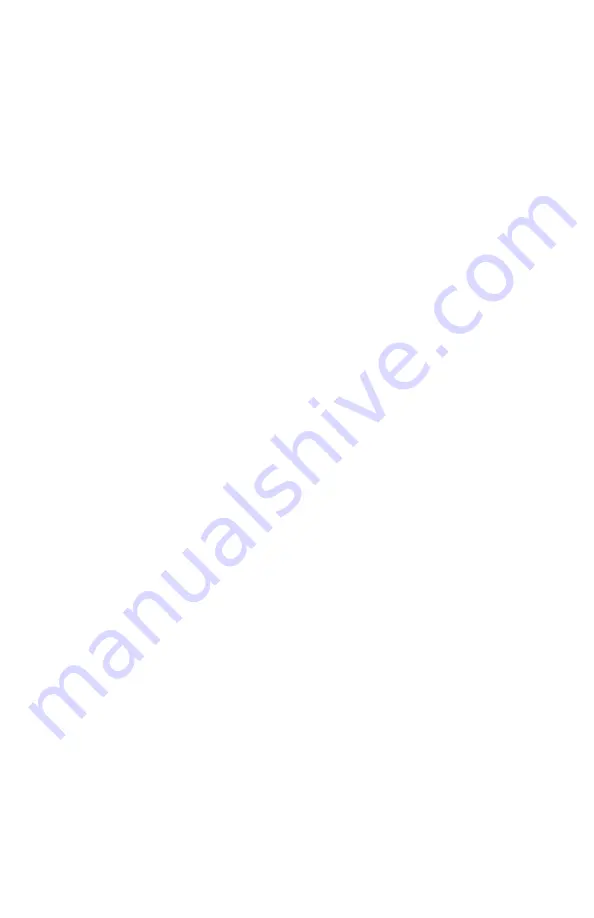
5.3 Dynamic Balance of the Propeller
Your Whirl Wind Propeller System has been statically
balanced at the factory. However, it is recommended to have
the engine/propeller dynamically balanced before the first
flight.
Repeat the same inspection after balancing as for first run-up.
All engine RPM and power settings limitations must be
followed when operating the Whirl Wind 400A Series propeller.
Refer to your Whirl Wind propeller data sheet for propeller
operation limitations.
5.4 Inspection after First 2 Hours of Flight
Repeat entire inspection done in section 5.2 “Inspection after
first run-up” after the first two hours of flight.
All engine RPM and power settings limitations must be
followed when operating the Whirl Wind 400A Series
propeller. Refer to your Whirl Wind propeller data sheet
for propeller operation limitations.
5-3