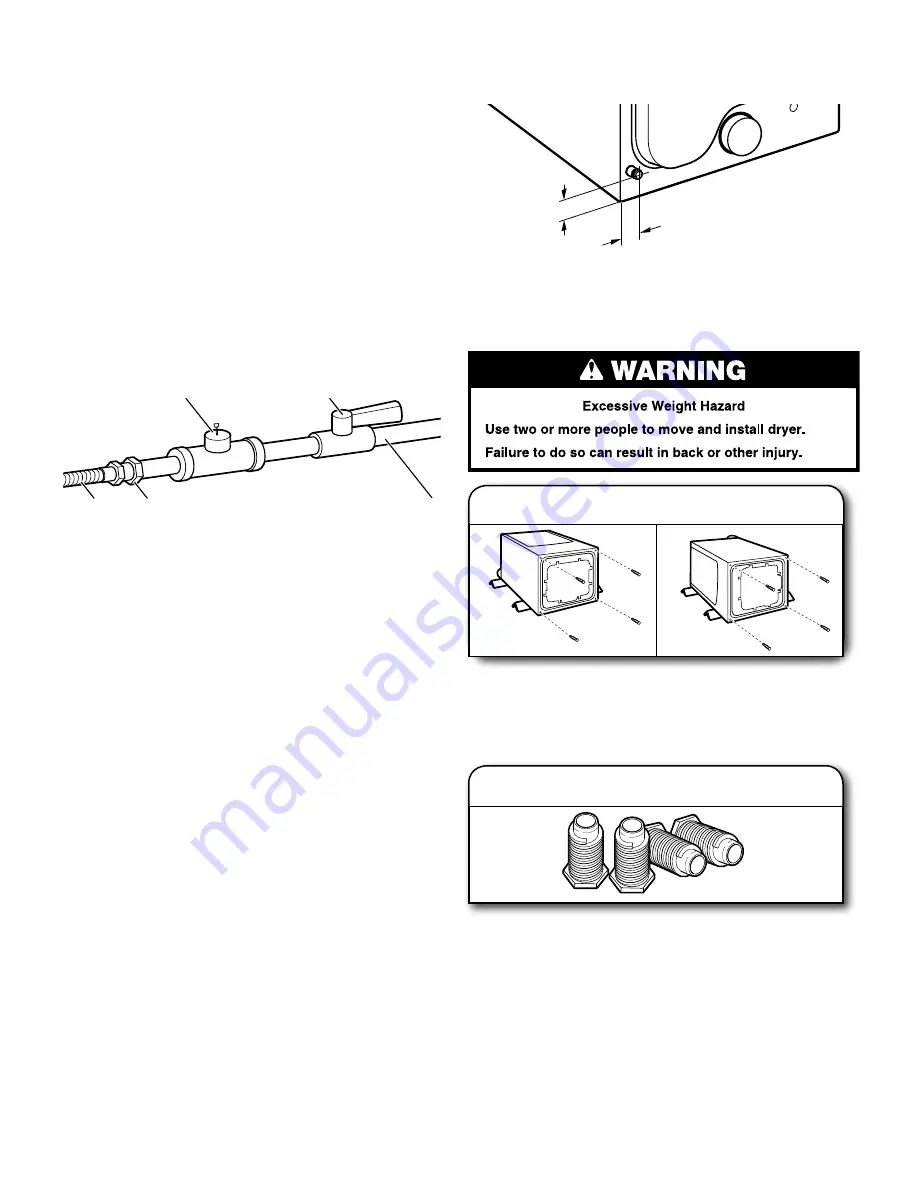
9
3/8" NPT dryer pipe
NOTE:
For a garage installation, the gas pipe height must be an
additional 18" (460 mm) from the floor.
GAS SUPPLY CONNECTION REQUIREMENTS
■
Use an elbow and a 3/8" flare x 3/8" NPT adapter fitting
between the flexible gas connector and the dryer gas pipe,
as needed to avoid kinking.
■
Use only pipe-joint compound. Do not use TEFLON
®†
tape.
■
This dryer must be connected to the gas supply line with a
listed flexible gas connector that complies with the standard
for connectors for gas appliances, ANSI Z21.24 or CSA 6.10.
BURNER INPUT REQUIREMENTS
Elevations above 2,000 ft. (610 m):
■
When installed above 2,000 ft. (610 m) a 4% reduction of the
burner Btu rating shown on the model/serial number plate is
required for each 1,000 ft. (305 m) increase in elevation.
Gas supply pressure testing
■
The dryer must be disconnected from the gas supply piping
system during pressure testing at pressures greater than
1/2 psi.
A. 3/8" flexible gas connector
B. 3/8" pipe to flare adapter fitting
C. 1/8" NPT minimum plugged tapping
D. 1/2" NPT gas supply line
E. Gas shutoff valve.
■
Lengths over 20 ft. (6.1 m) should use larger tubing and
a different size adapter fitting.
■
If your dryer has been converted to use LP gas, 3/8" LP
compatible copper tubing can be used. If the total length of
the supply line is more than 20 ft. (6.1 m), use larger pipe.
NOTE:
Pipe-joint compounds that resist the action of
LP gas must be used. Do not use TEFLON
®†
tape.
■
Must include shut-off valve
In the U.S.A.:
An individual manual shut-off valve must be installed within
six (6) ft. (1.8 m) of the dryer in accordance with the National
Fuel Gas Code, ANSI Z223.1. The location should be easy to
reach for opening and closing.
In Canada:
An individual manual shut-off valve must be installed in
accordance with the B149.1, Natural Gas and Propane
Installation Code. It is recommended that an individual
manual shutoff valve be installed within six (6) ft. (1.8 m) of
the dryer. The location should be easy to reach for opening
and closing.
E
B
A
D
C
†®TEFLON is a registered trademark of E.I. Dupont De Nemours and Company.
3"
(77 mm)
1
3
/
8
"
(35 mm)
DRYER GAS PIPE
■
The gas pipe that comes out through the rear of your dryer
has a 3/8" male pipe thread.
INSTALL LEVELING LEGS
Prepare dryer for leveling legs
1.
Firmly grasp dryer body (not console panel) and gently lay
dryer down on back cardboard corner posts.
IMPORTANT:
If laying dryer on its back, use the cardboard
corner posts the dryer was packed with to avoid damaging
the back of the dryer.
Screw in leveling legs
2.
Using a wrench and tape measure, screw leveling legs into
leg holes until bottom of foot is approximately 1" (25 mm)
from bottom of dryer.
Now stand the dryer on its feet. Slide the dryer until it is
close to its final location. Leave enough room to connect
the exhaust vent.