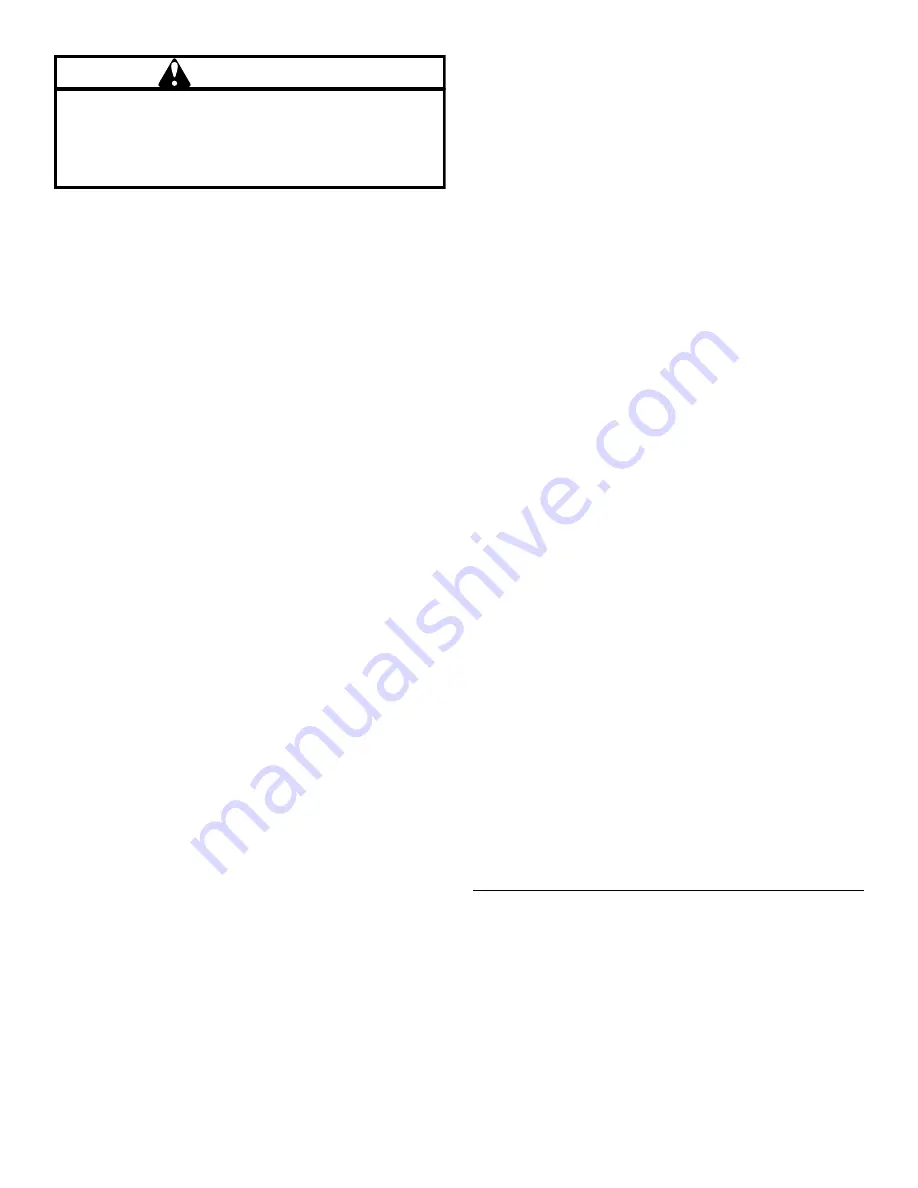
6
■
Centrally locate the furnace with respect to the proposed or
existing air distribution system.
■
Check that the temperature of the return air entering the
furnace is between 55°F and 100°F (18ºC and 38ºC) when the
furnace is heating.
■
Provide provisions for venting combustion products outdoors
through a proper venting system. Special consideration
should be given to the vent/flue pipe routing and the
combustion air intake pipe when applicable. Refer to
“Termination Locations” in “Vent/Flue Pipe and Combustion
Air Pipe” for appropriate termination locations and to
determine if the piping system from the furnace to the
termination can be accomplished within the guidelines given.
NOTE: The length of flue and/or combustion air piping can be
a limiting factor in the location of the furnace.
■
Locate the furnace so that the condensate flows downward
to the drain.
NOTE: Do not locate the furnace or its condensate drainage
system in any area subject to below freezing temperatures
without the proper freeze protection. Refer to “Condensate
Drain Lines and Trap” for further details.
■
Check that adequate combustion air is available for the
furnace. Improper or insufficient combustion air can expose
building occupants to gas combustion products that could
include carbon monoxide. Refer to “Combustion and
Ventilation Air Requirements.”
■
Set the furnace on a level floor to enable proper condensate
drainage. If the floor becomes wet or damp at times, place
the furnace above the floor on a concrete base sized
approximately 1
¹⁄₂
" (3.8 cm) larger than the base of the
furnace. Refer to “Horizontal Applications and
Considerations” for leveling of horizontal furnaces.
■
Check that the upflow or horizontal furnaces are not installed
directly on carpeting, or any other combustible material.
NOTE: The only combustible material allowed is wood.
■
A special accessory subbase must be used for the upright
counterflow unit installations over any combustible material
(including wood). Refer to subbase instructions for installation
details.
NOTE: A subbase will not be required if an air conditioning
coil is located beneath the furnace between the supply air
opening and the combustible floor.
■
Exposure to contaminated combustion air will result in safety
and performance-related problems.
NOTE: Do not install the furnace where the combustion air is
exposed to the following substances:
Chlorinated waxes or cleaners
Chlorine-based swimming pool chemicals
Water softening chemicals
Deicing salts or chemicals
Carbon tetrachloride
Halogen-type refrigerants
Cleaning solutions (such as perchloroethylene)
Printing inks
Paint removers
Varnishes
Hydrochloric acid
Cements and glues
Antistatic fabric softeners for clothes dryers
Masonry acid washing materials
■
Seal off a nondirect vent furnace if it is installed near an area
frequently contaminated by any of the above substances.
This protects the nondirect vent furnace from airborne
contaminants. To ensure that the enclosed nondirect vent
furnace has an adequate supply of combustion air, vent from
a nearby uncontaminated room or from outdoors. Refer to
“Combustion and Ventilation Air Requirements” for details.
■
If the furnace is used in connection with a cooling coil unit,
install the furnace upstream or in parallel with the cooling coil
unit. Premature heat exchanger failure will result if the cooling
coil unit is placed ahead of the furnace.
■
If the furnace is installed in an application where the typical
operating sound level of a furnace is deemed objectionable,
an optional sound reduction kit is available. Consult your
local distributor for more details.
■
If the furnace is installed in a residential garage, position the
furnace so that the burners and ignition source are located
not less than 18" (45.7 cm) above the floor. Protect the
furnace from physical damage by vehicles.
■
If the furnace is installed horizontally, ensure the furnace
access doors are not on the “up/top” or “down/bottom” side
of the furnace.
■
Do not connect the furnace to a chimney flue that serves a
separate appliance designed to burn solid fuel.
■
On counterflow installations, the air conditioning coil must be
downstream on the supply (positive) side of the furnace heat
exchanger.
Counterflow Installation Over a Noncombustible Floor
■
Before setting the furnace over the plenum opening, ensure
that the surface around the opening is smooth and level. A
tight seal should be made between the furnace base and
floor by using a silicone rubber caulking compound or
cement grout.
Counterflow Installation Over a Combustible Floor
■
If installation over a combustible floor becomes necessary,
use an accessory subbase (see Specification Sheet
applicable for your model for details). A special accessory
subbase must be used for upright counterflow unit
installations over any combustible material including wood.
Refer to subbase instructions for installation details. Follow
the instructions with the subbase for proper installation.
NOTES:
■
Do not install the furnace directly on carpeting, tile or
other combustible material other than wood flooring.
■
The subbase will not be required if an air conditioning coil
is installed between the supply air opening on the furnace
and the floor.
Clearances and Accessibility
Installations must adhere to the clearances to combustible
materials to which this furnace has been design-certified. The
minimum clearance information for this furnace is provided on
the unit’s clearance label. These clearances must be permanently
maintained. Clearances must also accommodate an installation’s
gas, electrical, drain trap and drain line connections. If the
alternate combustion air intake or vent/flue connections are
used, additional clearance must be provided to accommodate
these connections. Refer to “Vent/Flue Pipe and Combustion Air
Pipe” for details.
NOTE: In addition to the required clearances to combustible
materials, a minimum of 24" (61 cm) service clearance must be
available in front of the unit.
Goodman 48
Possible property damage, personal injury or death due
to fire, explosion, smoke, soot, condensation, electrical
shock or carbon monoxide may result from improper
installation, repair, operation or maintenance of this
product.
WARNING