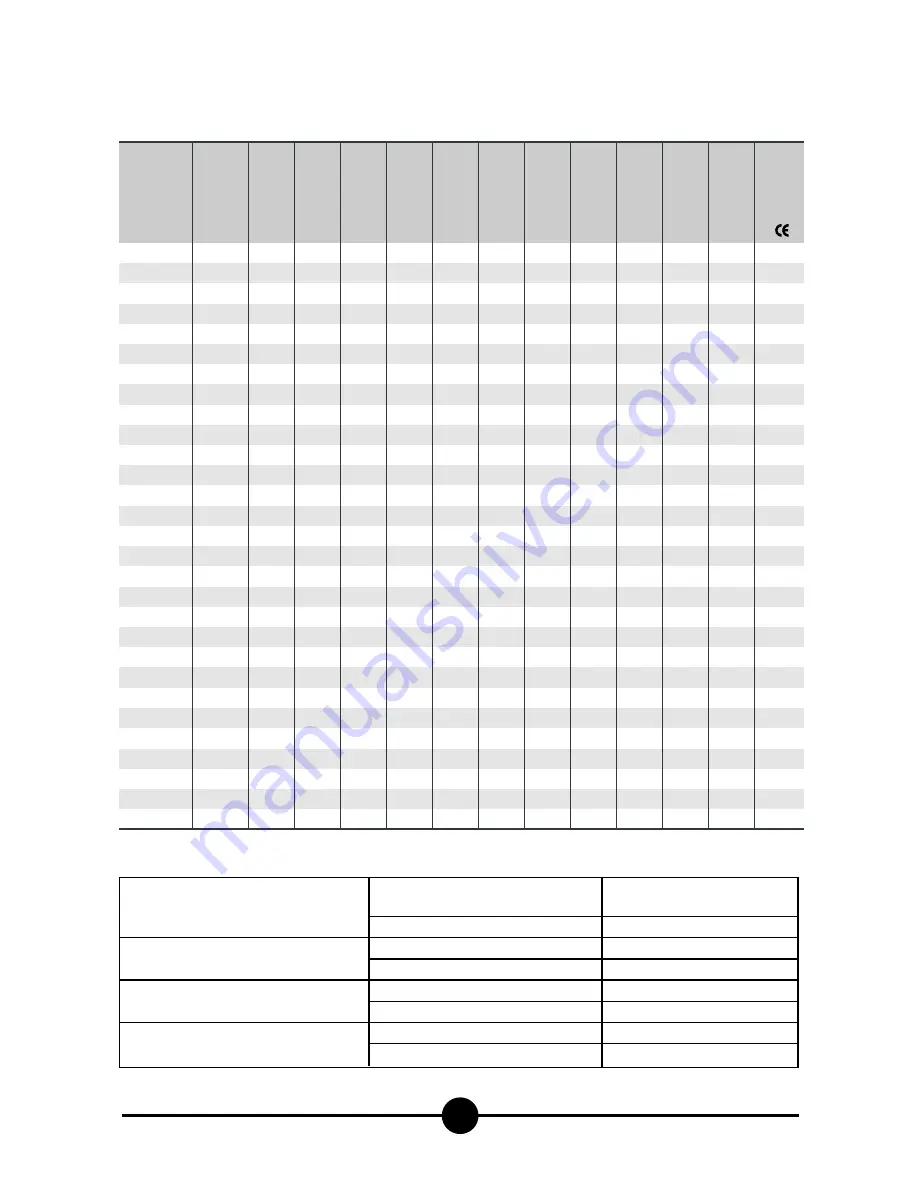
032-03 - Gas kettles
8
TECNICAL DATA
600
600
750
900
900
600
600
750
900
900
600
600
750
900
900
600
600
750
900
900
600
600
600
600
600
600
600
600
100
140
200
300
535
100
140
200
300
535
100
135
200
300
535
100
140
200
300
535
100
100
140
140
100
100
140
140
-
-
-
-
-
-
-
-
-
-
0,5
0,5
0,5
0,5
0,5
0,5
0,5
0,5
0,5
0,5
0,5
0,5
0,5
0,5
0,5
0,5
0,5
0,5
-
-
-
-
-
0,05
0,05
0,05
0,05
0,05
-
-
-
-
-
0,05
0,05
0,05
0,05
0,05
-
0,05
-
0,05
-
0,05
-
0,05
50-300
50-300
50-300
50-300
50-300
50-300
50-300
50-300
50-300
50-300
50-300
50-300
50-300
50-300
50-300
50-300
50-300
50-300
50-300
50-300
50-300
50-300
50-300
50-300
50-300
50-300
50-300
50-300
51BS3469
51BS3469
85BL0620
85BL0620
85BL0620
51BS3469
51BS3469
85BL0620
85BL0620
85BL0620
51BS3469
51BS3469
85BL0620
85BL0620
85BL0620
51BS3469
51BS3469
85BL0620
85BL0620
85BL0620
51BS3469
51BS3469
51BS3469
51BS3469
51BS3469
51BS3469
51BS3469
51BS3469
N.
Model
Type of heating
(A) Width
(mm)
(B) Depth
(mm)
(C) Height
(mm)
Vat diameter
(mm)
Vat usable volume
(lt)
Pressure in the vat
(bar)
Jacket pressure
(bar)
Hot water
connection
(mm)
Cold water
connection
(mm)
Water pressure
(kPa)
Gas connection
(R")
direct
direct
direct
direct
direct
direct
direct
direct
direct
direct
indirect
indirect
indirect
indirect
indirect
indirect
indirect
indirect
indirect
indirect
direct
direct
direct
direct
indirect
indirect
indirect
indirect
10
10
1/2"
1/2"
1/2"
10
10
1/2"
1/2"
1/2"
10
10
1/2"
1/2"
1/2"
10
10
1/2"
1/2"
1/2"
10
10
10
10
10
10
10
10
10
10
1/2"
1/2"
1/2"
10
10
1/2"
1/2"
1/2"
10
10
1/2"
1/2"
1/2"
10
10
1/2"
1/2"
1/2"
10
10
10
10
10
10
10
10
1/2"
1/2"
3/4"
3/4"
3/4"
1/2"
1/2"
3/4"
3/4"
3/4"
1/2"
1/2"
3/4"
3/4"
3/4"
1/2"
1/2"
3/4"
3/4"
3/4"
1/2"
1/2"
1/2"
1/2"
1/2"
1/2"
1/2"
1/2"
800
800
1000
1150
1250
800
800
1000
1150
1250
800
800
1000
1150
1250
800
800
1000
1150
1250
800
800
800
800
800
800
800
800
900
900
1150
1300
1400
900
900
1150
1300
1400
900
900
1150
1300
1400
900
900
1150
1300
1400
900
900
900
900
900
900
900
900
875
875
875
875
875
875
875
875
875
875
875
875
875
875
875
875
875
875
875
875
735
735
735
735
735
735
735
735
AGB 373/WP
AGB 378/WP
AGB 387/WP
AGB 393/WP
AGB 379/WP
AGB 388/WP
AGB 394/WP
AGB 371/WP
AGB 374/WP
AGB 383/WP
AGB 389/WP
AGB 376/WP
AGB 385/WP
AGB 391/WP
AGB 397/WP
AGB 402/WP
AGB 403/WP
AGB 395/WP
AGB 398/WP
Nominal main pressure
Gas family 2 – Natural
20 mbar
for the different types of gas
Gas family 3 – LPG
28-30/37 mbar
Operation permissible it pressure
Gas family 2 – Natural
da 17 a 25 mbar
is in the range:
Gas family 3 – LPG
da 20/25 a 35/45 mbar
Operation non permissible it pressure
Gas family 2a – Natural
17 mbar
is lower than:
Gas family 3a – LPG
20/25 mbar
Operation non permissible it pressure
Gas family 2 – Natural
25 mbar
is higher than:
Gas family 3 – LPG
35/45mbar
Gas inlet pressure