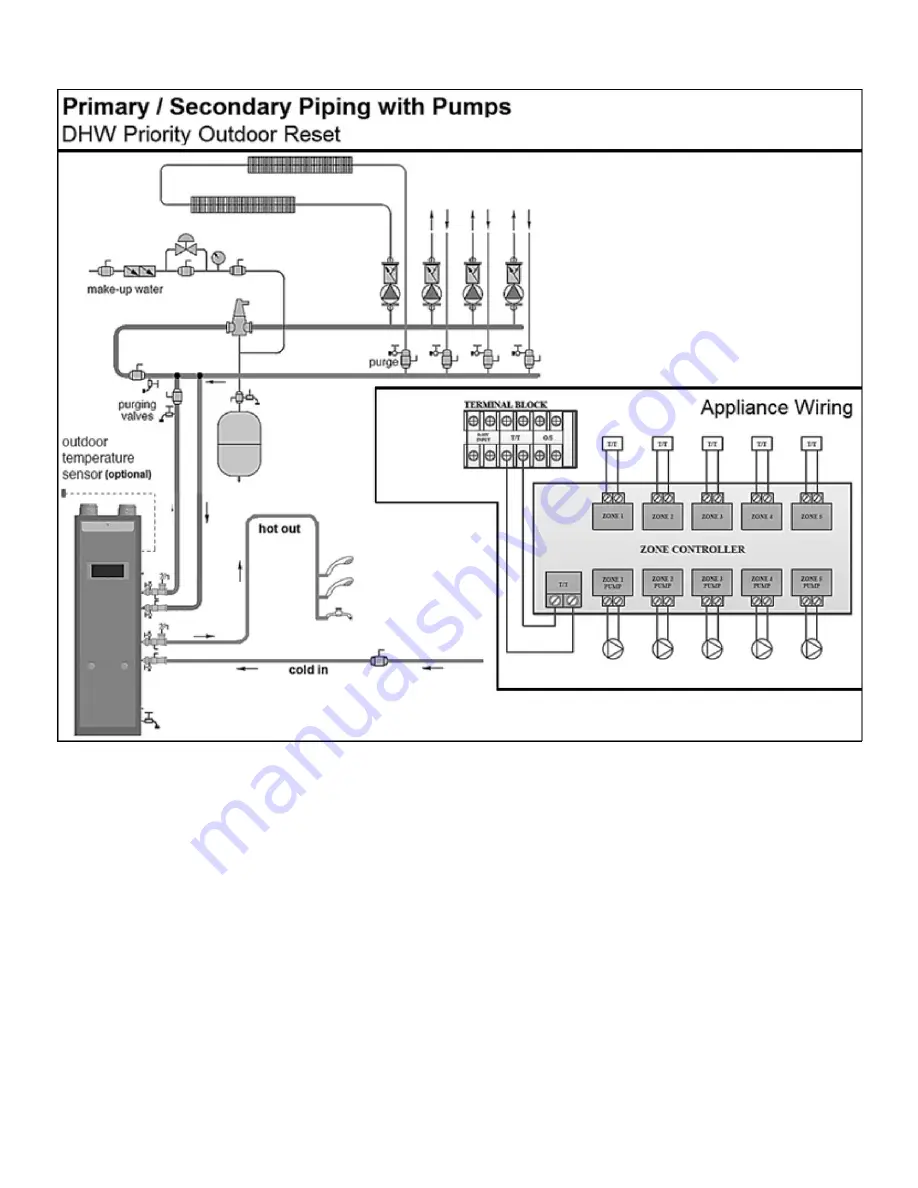
35
WHL-015 REV. 5.20.16
Figure 23
– CH Piping – Zoning with Pumps
NOTES:
1. This drawing is meant to show system piping concept only. Installer is responsible for all equipment and detailing required by local
codes.
2. All closely spaced tees shall be within 4 pipe diameters center to center spacing.
3. A minimum of 6 pipe diameters of straight pipe shall be installed upstream and downstream of all closely spaced tees.
4. The
minimum
pipe size of DHW piping should be ¾” diameter and CH piping should be 1” in diameter.
5. Circulators are shown with isolation flanges. The alternative is standard flanges with full port ball valves. Purge valves can be used
with circulator flanges as an alternative.
6. Piping shown is Primary/Secondary. System flow (secondary loop) must be greater than the appliance
’s primary loop flow.
7. Install a minimum of 12 diameters of straight pipe upstream of all circulators.
8.
VERY IMPORTANT
– Minimum flow rates outlined in this manual must be maintained through the heat exchanger to minimize short
cycling.
9. Each heating zone of a pump-based system has its own circulator with turns on when a zone thermostat calls for heat.
Summary of Contents for WBRC**140F
Page 2: ...2 WHL 015 REV 5 20 16 ...
Page 42: ...42 WHL 015 REV 5 20 16 Figure 29 140F Model Electrical Wiring Diagram ...
Page 43: ...43 WHL 015 REV 5 20 16 Figure 30 140F Model Ladder Diagram ...
Page 44: ...44 WHL 015 REV 5 20 16 Figure 31 199F Model Electrical Wiring Diagram ...
Page 45: ...45 WHL 015 REV 5 20 16 Figure 32 199F Model Ladder Diagram ...
Page 86: ...86 WHL 015 REV 5 20 16 ...
Page 87: ...87 WHL 015 REV 5 20 16 ...