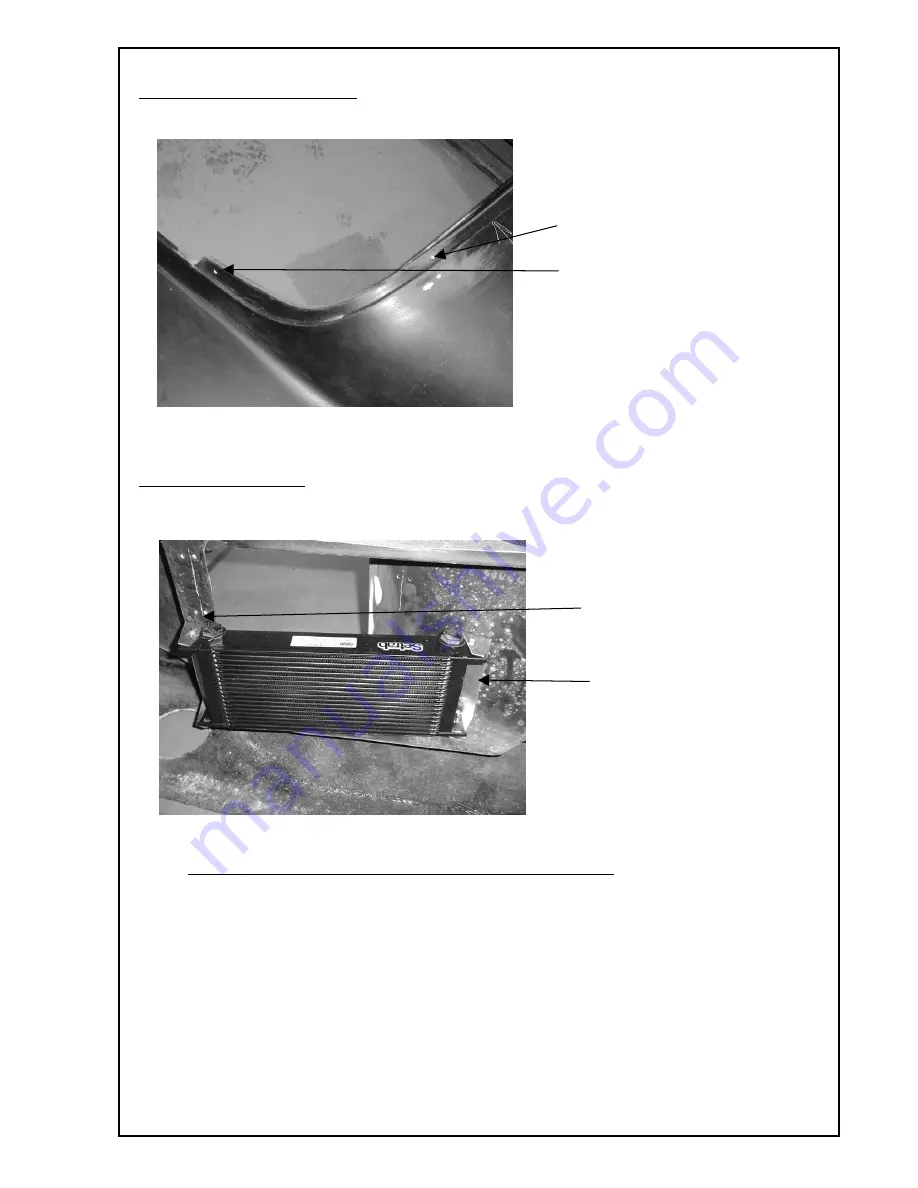
2.5
1.f. Windscreen Mounting Holes
Carefully position the windscreen
onto the pre-formed recess, and
drill through the five holes in the
screen with a 4mm drill. Then
remove the screen and drill
through the underside surface
only with a 9mm drill. This is to
allow the M4 nut to clamp up on
the correct face of the bodywork.
1.g. Oil Cooler Mounting
Oil cooler in position mounted
from two brackets supplied
and bolted through the flanges
front and rear of the right
hand side air intake. Mounted
using M6 nuts and bolts.
View from Inside Bodywork Looking At Right Hand Side of Car
Summary of Contents for XTR2
Page 3: ...1 1 Section 1 ...
Page 4: ...1 2 ...
Page 14: ...1 12 ...
Page 15: ...2 1 Section 2 ...
Page 16: ...2 2 ...
Page 22: ...3 1 Section 3 ...
Page 23: ...3 2 ...
Page 28: ...4 1 Section 4 ...
Page 29: ...4 2 ...
Page 37: ...Step 9 Main Power Cables In Engine Bay 4 10 Reverse Motor Starter Relay Reverse Solonoid ...
Page 43: ...4 15 ...
Page 46: ...5 1 Section 5 ...
Page 47: ...5 2 ...
Page 51: ...6 1 Section 6 ...
Page 52: ...6 2 ...
Page 57: ...7 1 Section 7 ...
Page 58: ...7 2 ...
Page 60: ...8 1 Section 8 ...
Page 61: ...2 2 ...
Page 63: ...9 1 Section 9 ...
Page 64: ...9 2 ...
Page 68: ...10 1 Section 10 ...
Page 69: ...10 2 ...
Page 72: ...11 1 Section 11 ...
Page 73: ...11 2 ...
Page 77: ...12 1 Section 12 ...
Page 78: ...12 2 ...
Page 81: ...13 1 Section 13 ...
Page 82: ...13 2 ...
Page 86: ...14 1 Section 14 ...
Page 87: ...14 2 ...
Page 91: ...15 1 Section 15 ...
Page 92: ...15 2 ...
Page 97: ...16 1 Section 16 ...
Page 98: ...16 2 ...
Page 103: ...17 1 Section 17 ...
Page 104: ...17 2 ...
Page 107: ...18 1 Section 18 ...
Page 108: ...18 2 ...
Page 112: ...19 1 Section 19 ...
Page 113: ...19 2 ...
Page 119: ...20 1 Section 20 ...
Page 120: ...20 2 ...
Page 126: ...20 8 ...
Page 128: ...2 1 Section 21 ...
Page 129: ...2 2 ...
Page 143: ...2 16 ...
Page 144: ...2 17 ...
Page 145: ...2 18 ...
Page 146: ...2 1 Section 22 ...
Page 147: ...2 2 ...
Page 151: ...2 6 ...
Page 152: ...2 7 ...
Page 158: ...2 6 ...
Page 159: ...2 7 Tachometer Controls ...