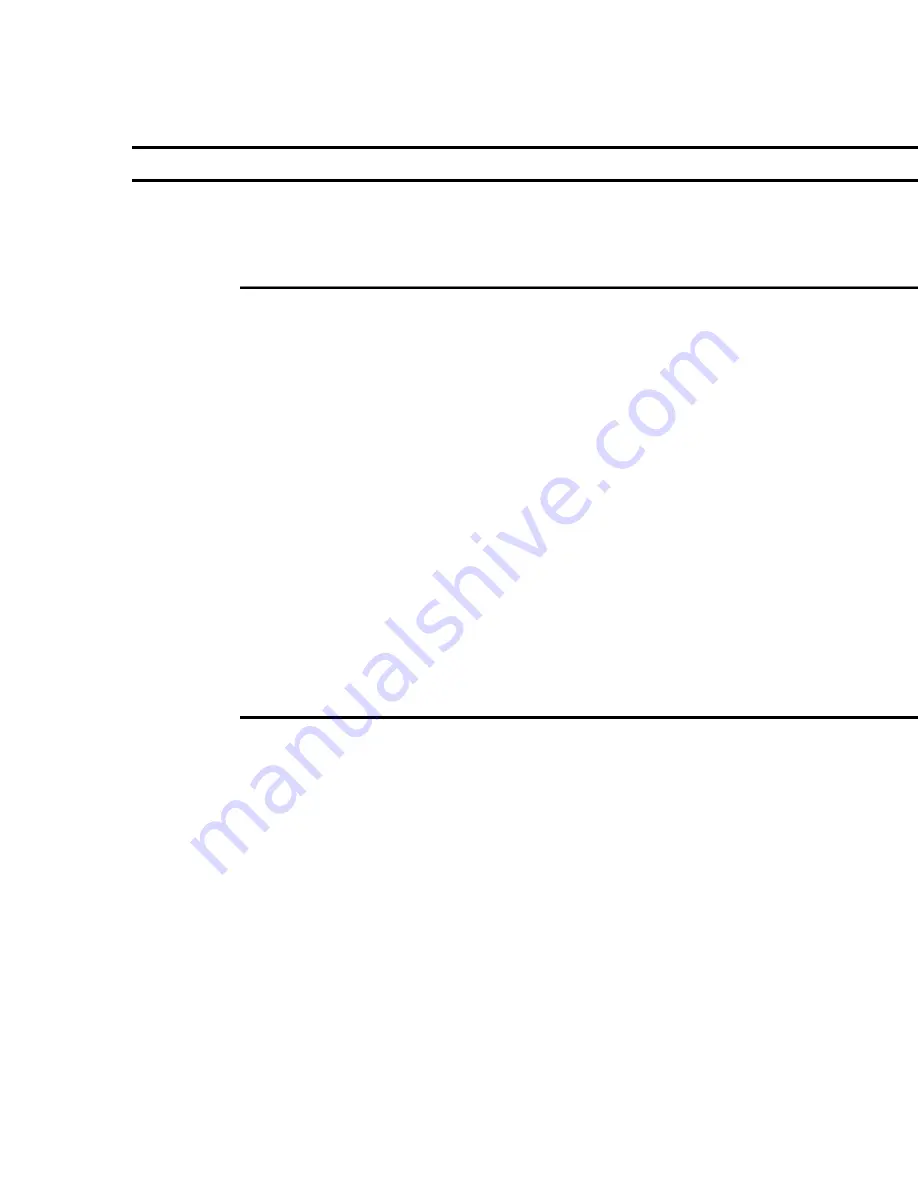
Section 6
Testing
Test Recommendations
A preoperation test of the Westco Model 16 casing tong is recommended subsequent to motor
replacement or repair, control valve replacement or repair and major parts replacement.
During the testing operations, the operator should listen for any unusual noises or grinding and
Watch for any misalignment or erratic operation.
Free Run Test
For the free run test, perform a preoperation check (Figure 6-1). During the run test, the
rotary should be free run for 15 minutes at both low and high speeds in "make" position, then
repeated in "break" position. If anything out of the ordinary is suspected, stop and investigate
before proceeding.
To perform free run operation, place the reversing pin in "make" position and place the shifting
handle in low-gear position. "Crack" the throttle handle until the rotary attains approximately
10 rpm and hold for two minutes while observing rotary action and listening for any unusual
noise. Slowly move the throttle handle to full open position and hold for two minutes. Return
the throttle handle to a slightly open position and hold for two minutes. Return the throttle
handle to neutral position, place the tong in high hear and repeat the slow-fast-slow sequence
three times.
NOTE:
The rotary plunger will make a click-clack noise as it passes the plunger pocket and
the door junctions. This noise is expected when the tong is free running. If unusual
noises do occur, check any parts that have just been repaired or replaced for
misalignment, rubbing or grinding. Refer to "Troubleshooting".
Repeat the test procedure with the reversing pin in "break" position. Should a problem be
indicated during the free run test, correct the problem and repeat the test to assure that the
corrective action was effective.
WARNING: Under no circumstances should the throttle handle be tied or in any way
secured in an operating position.
Torque-Up Test
Performing the torque test (with jaw installed) normally requires access to a mandrel or test
fixture. When a mandrel or test fixture is not available, a test should be run at the first
opportunity on "in-hole" pipe or casing (refer to "Operation").
In "make" position, pace the shifting handle in low-gear position. (For a tandem-gear
motor tong, place the motor selector valve in low-speed position.) Slowly push the throttle
handle forward. As the jaws begin gripping the pipe, observe both output torque and input
hydraulic pressure to the tong. Output torque should be a direct ratio to input hydraulic
pressure according to the ratios shown in Figure 1-6, Section 1, page 5 for the motor size
installed on the tong.
Continue pushing the throttle handle forward until approximately 70 percent of the
determined maximum torque is reached.
Back off the throttle handle, then advance to the 70 percent maximum torque. Repeat this
step once.
Advance the throttle handle and run the pipe up to specified make-up torque.
Break out of the joint and rerun to the required joint torque.
Section 6 Page 1
Summary of Contents for 16-25
Page 7: ...Figure 1 3 Schematic of drive train in high gear Figure 1 4 Low gear...
Page 28: ...Figure 7 1 Installation of 6 5 8 through 13 3 8 inch jaws Section 7 Page2...
Page 29: ......
Page 31: ......
Page 32: ......
Page 33: ......
Page 34: ......
Page 37: ......
Page 38: ......
Page 39: ......
Page 40: ...Figure 8 6 Tong case body door assembly Section 8 Page 6...
Page 41: ......
Page 42: ......
Page 43: ......
Page 44: ......
Page 45: ......
Page 46: ......
Page 47: ......
Page 48: ......
Page 49: ......