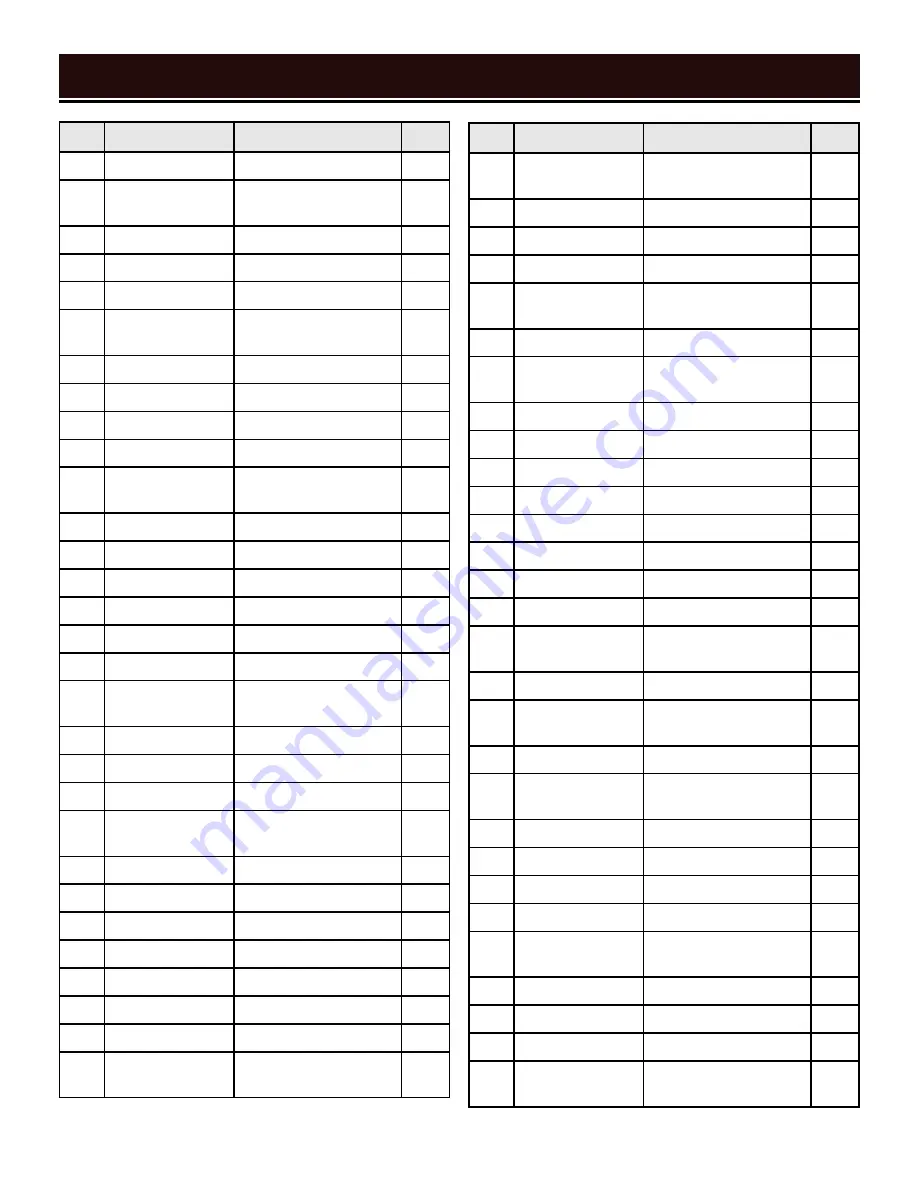
EXPLODED VIEW & PARTS LIST
No.
Part No.
Description
Qty.
60
3975-060
Driven Wheel
1
61
3975-061
Flat Head Screw,
M8x12
1
62
3975-062
Key, 4x4x20mm
1
63
3975-063
Drive Wheel
1
64
3975-064
Flat Washer
1
65
3975-065
Flat Head Screw,
M6x12
1
66
3975-066
Frame
1
67
3975-067
Spring Washer
8
68
3975-068
Blade Tension Knob
1
69
3975-069
Cord Clamp
2
70
3975-070
Pan Head Screw,
M5x8
2
71
3975-071
Set Screw, M6x8
1
72
3975-072
Lock Handle
1
73
3975-073
Flat Washer, 6mm
1
74
3975-074
Nut, M6
4
75
3975-075
Lock Washer, 6mm
4
76
3975-076
Flat Washer, 6mm
4
77
3975-077
Rear Blade Guide
Block
1
78
3975-078
Ball Bearing, 625ZZ
2
79
3975-079
Flat Washer, 5mm
4
80
3975-080
Pin, 5x24mm
1
81
3975-081
Socket Head Screw,
M6x25
1
82
3975-082
Lock Washer, 6mm
1
83
3975-083
Blade Guard
1
84
3975-084
Flat Washer, 6mm
4
85
3975-085
Ball Bearing, 607ZZ
8
86
3975-086
Shaft
4
87
3975-087
Flat Washer, 6mm
2
88
3975-088
Lock Washer, 6mm
2
89
3975-089
Socket Head Screw,
M6x25
2
No.
Part No.
Description
Qty.
90
3975-090
Socket Head Screw,
M5x10
1
91
3975-091
Flat Washer, 5mm
1
92
3975-092
Guard Plate
1
93
3975-093
Pin, 5x35mm
1
94
3975-094
Front Blade Guide
Block
1
95
3975-095
Nut, M6
1
96
3975-096
Socket Head Screw,
M6x25
1
97
3975-097
Nut, M16-1.5
1
98
3975-098
Center Shaft
1
99
3975-099
Torsion Spring
1
100
3975-100
Lock Handle
1
101
3975-101
Flat Washer, 10mm
1
102
3975-102
Swivel Support
1
103
3975-103
Flat Washer, 12mm
1
104
3975-104
Nut, M12
1
105
3975-105
Hex Head Bolt,
M6x25
1
106
3975-106
Nut, M6
1
107
3975-107
Socket Head Screw,
M6x35
1
108
3975-108
Flat Washer, 6mm
1
109
3975-109
Socket Head Screw,
M5x10
2
110
3975-110
Positive Stop Cam
2
111
3975-111
Bushing
1
112
3975-112
Retaining Ring, 8mm
1
113
3975-113
Lock Pin
1
114
3975-114
Pan Head Screw,
M4x8
2
115
3975-115
Angle Scale
1
116
3975-116
Base
1
117
3975-117
Foot
4
118
3975-118
Carriage Bolt,
M10x40
1
18
Summary of Contents for BA4555
Page 16: ...EXPLODED VIEW PARTS LIST 16 ...