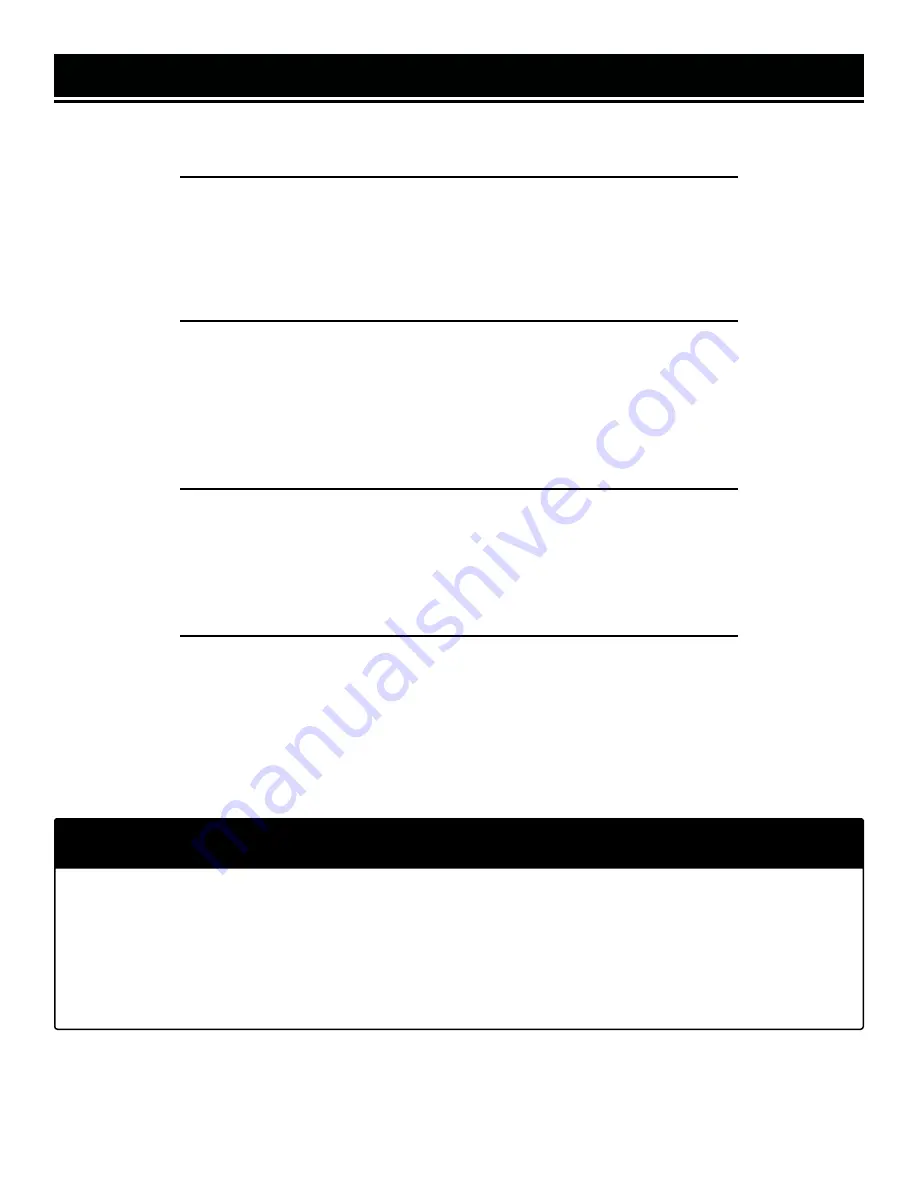
CONTENTS
WELCOME 3
Introduction ..................................................................................................... 3
Specifications ................................................................................................... 3
SAFETY 4
General Safety Rules ........................................................................................ 4
Spindle Sander Safety Warnings ...................................................................... 6
Electrical Information ....................................................................................... 8
BEFORE OPERATING
9
Know Your Spindle Sander ...............................................................................9
Assembly & Adjustments ............................................................................... 10
OPERATION & MAINTENANCE
13
Operation ....................................................................................................... 13
Maintenance ....................................................................................................14
Troubleshooting Guide ................................................................................... 15
Exploded View & Parts List .............................................................................17
Warranty Statement ........................................................................................20
To purchase accessories and replacement parts for your tool, visit
WENPRODUCTS.COM
80-Grit Sanding Sleeves
(Model 6510SP80)
120-Grit Sanding Sleeves
(Model 6510SP120)
150-Grit Sanding Sleeves
(Model 6510SP150)
240-Grit Sanding Sleeves
(Model 6510SP240)
Assorted Sanding Sleeve Combo Pack
(Model 6510SPC)
2