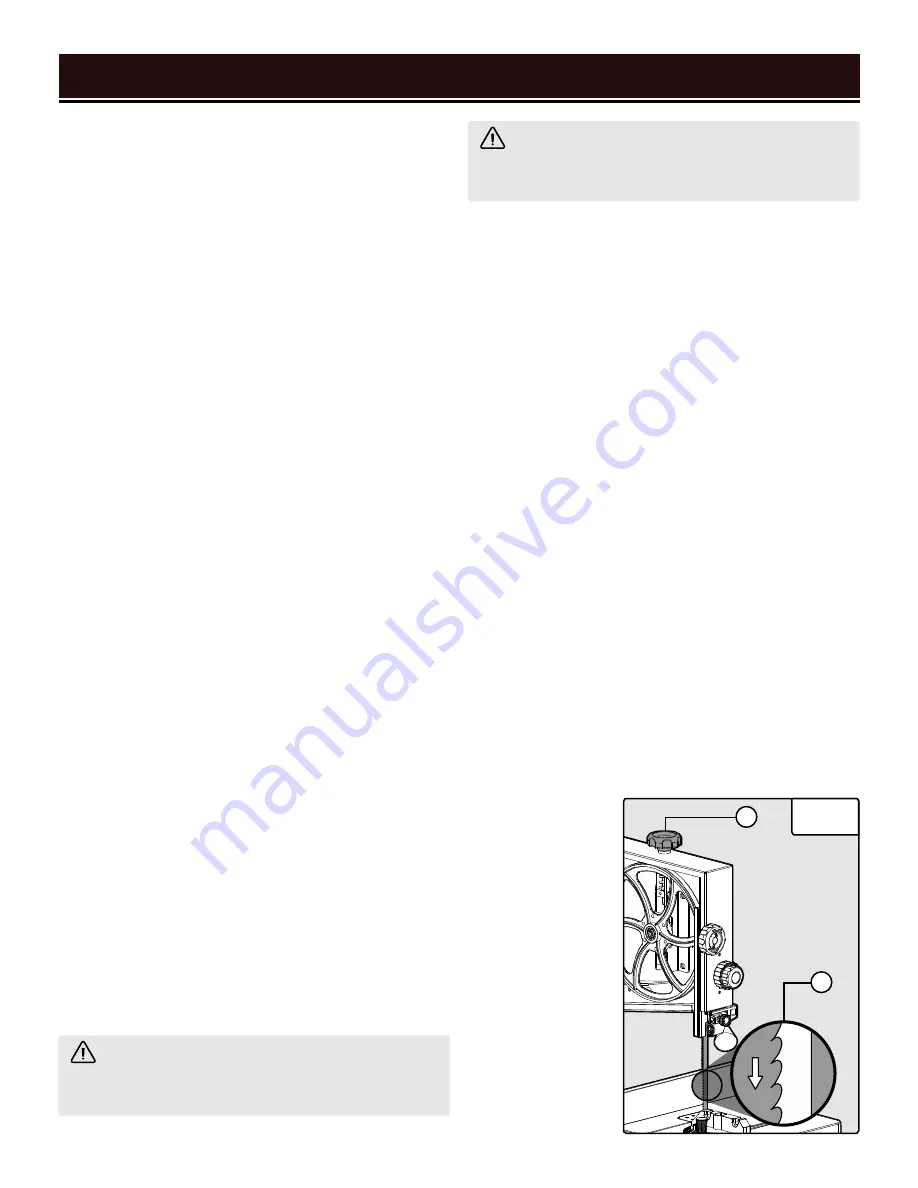
17
16
CAUTION! Saw blades are sharp. Always wear
ANSI Z87.1-approved eye protection, as well as
protective gloves, while handling saw blades.
CAUTION! Always be sure that the band saw
is turned OFF and unplugged before making any
adjustments.
OPERATION
Fig. 22
GENERAL CUTTING GUIDELINES
1. Make a test cut on scrap wood to test the settings and
get the hang of operating the band saw.
2. Make all adjustments with the band saw turned OFF
and unplugged.
3. Make sure the upper guard is close to the upper face
of your workpiece (see Adjusting the Upper Blade Guide
on page 14). Always use a push stick when cutting in-
tricate or narrow workpieces. Keep fingers, hands, and
other beloved body parts away from the blade!
4. Do not force the workpiece against the blade. Let the
tool do the work. Light contact gives easier cutting and
prevents excess friction, which will prolong the life of
the blade and prevents workpiece burning.
5. Always use dust collection. A dust port is located on
the back of the saw, next to the motor (p. 10 - O). Use a
hose clamp (if necessary) to secure the adapter or dust
hose to the dust port.
6. The band saw is most suitable for straight-line cut-
ting (cross-cutting, ripping, miter cutting, beveling,
compound cutting, and resawing). While it can certainly
cut curves, it is not a scroll saw, and cannot perform the
same kinds of cuts. Do not cut sharp corners; instead,
saw around corners.
CUTTING CURVES
When cutting curves, carefully turn the workpiece so
that the blade follows the cut line without twisting. If the
curve is so sharp that you repeatedly back up and cut
new kerf, use a narrower blade, or a blade with more set
(that is, the teeth are further apart). When a blade has
more set, the workpiece turns more easily, but you will
get a rougher cut.
When changing a cut, do not withdraw the workpiece
from the blade – the workpiece may drag the blade off
the wheels. Instead, turn the workpiece and cut out
through the scrap section of the workpiece. When cut-
ting long curves, make relief cuts as you go along.
CHANGING BLADES (FIG. 22)
1. Double-check that the band saw is turned OFF and
disconnected from the power source. Open the upper
and lower doors.
2. Loosen the four guide rail lock knobs (you do not
have to completely remove the knobs), and slide the
guide rail off.
3. Turn the blade tension knob (A) to relieve tension on
the blade.
4. Remove the blade from the wheels and from between
the upper and lower bearing guides. Guide it through
the table slot. Store the blade in a safe place.
5. Guide the new blade through the table slot, spine
first. The blade teeth should be facing you, pointing
down towards the table (B).
6. Place the blade on the upper and lower wheels, and
between the bearing guides.
7. Tension the blade (see Adjusting the Blade Tension
on page 14).
8. Adjust the blade tracking (see Adjusting the Blade
Tracking on page 13).
9. Adjust the upper
and lower bearing
guides (see on
page 14 - 15).
10. Replace the
guide rail. Tighten
the lock knobs.
11. Make a test cut
on a scrap piece
of wood before
resuming cutting.
B
A