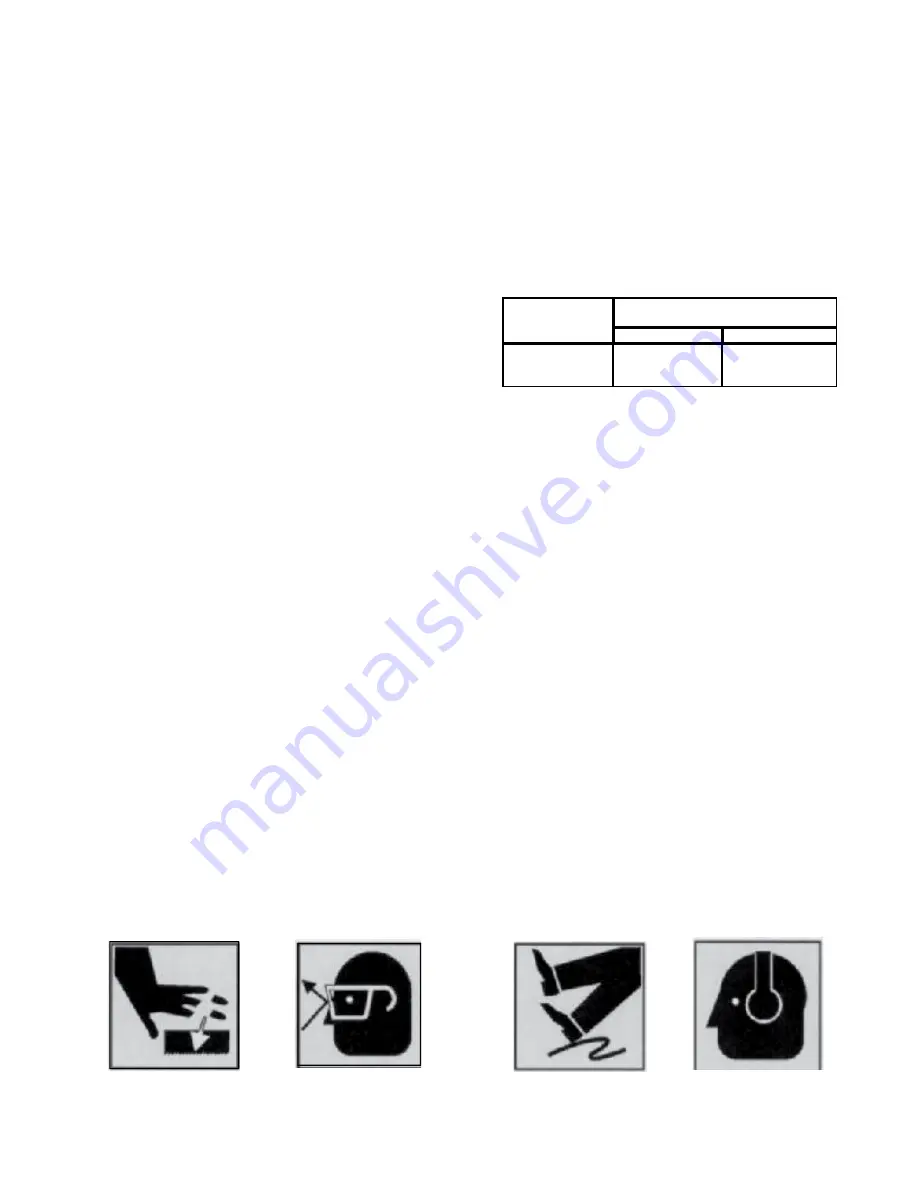
7
19. Some dust created by power sanding, sawing, grinding,
drilling and other construction activities contains chemicals
known to cause cancer, birth defects or other reproductive
harm. Some examples of these chemicals are:
-Lead from lead based paint
-Crystalline silica from bricks and cement and other masonry
products, and
-Arsenic and chromium from chemically treated lumber
20. Your risk from those exposures varies, depending on how
often you do this type of work. To reduce your exposure to
these chemicals: work in a well ventilated area, and work with
approved safety equipment, such as those dust masks that are
specifically designed to filter out microscopic particles.
1. Always wear leather gloves when handling a saw blade.
The operator shall not wear gloves when operating the
machine.
2. All doors shall be closed, all panels replaced, and all other
safety guards in place prior to the machine being started or
operated.
3. Be sure that the blade is not in contact with the workpiece
when the motor is started. The motor shall be started and you
should allow the saw to come to full speed before bringing the
workpiece into the saw blade.
4. Keep hands away from the blade area.
See figure A.
5. Remove any cut off piece carefully while keeping your
hands free from the blade area.
6. Saw must be stopped and electrical supply must be cut off
before any blade replacement or adjustment of blade support
mechanism is done, or before any attempt is made to change
the drive belts or before any periodic service or maintenance is
performed on the saw.
7. Remove all loose items and any unnecessary work pieces
from the area before starting machine.
8. Bring adjustable saw guides and guards as close as possible
to the work piece.
Figure A Figure B
General Electrical Cautions
This saw should be grounded in accordance with the National
Electrical Code and local codes and ordinances. This work
should be done by a qualified electrician. The saw should be
grounded to protect the user from electrical shock.
Wire sizes:
Caution: for circuits which are far away from the electrical
service box, the wire size must be increased in order to deliver
ample voltage to the motor. To minimize power losses and to
prevent motor overheating and burnout, the use of wire sizes
for branch circuits or electrical extension cords according to
the following table is recommended:
Conductor Length AWG (American wire gauge) number
240 volt lines
120 volt lines
0-50 feet
No. 14
No. 14
50-100 feet
No. 14
No. 12
Over 100 feet
No. 12
No. 8
9. Always wear protective eye wear when operating, servicing
or adjusting machinery. Eye wear shall be impact resistant,
protective safety glasses with side shields complying with
ANSI Z87.1 specifications. Use of eye wear which does not
comply with ANSI Z87.1 specifications could result in severe
injury from breakage of eye protection.
See figure B.
10. Non-slip footwear and safety shoes are recommended.
See
figure C.
11. Wear ear protectors (plugs or muffs) during extended
periods of operation.
See figure D.
12. The workpiece, or part being sawed, must be securely
clamped before the saw blade enters it.
13. Remove cut off pieces carefully, keeping hands away
from saw blade.
14. Saw must be stopped and electrical supply cut off or
machine unplugged before reaching into cutting area.
15. Avoid contact with coolant, especially guarding your
eyes.
Figure C Figure D
Safety instructions on sawing systems