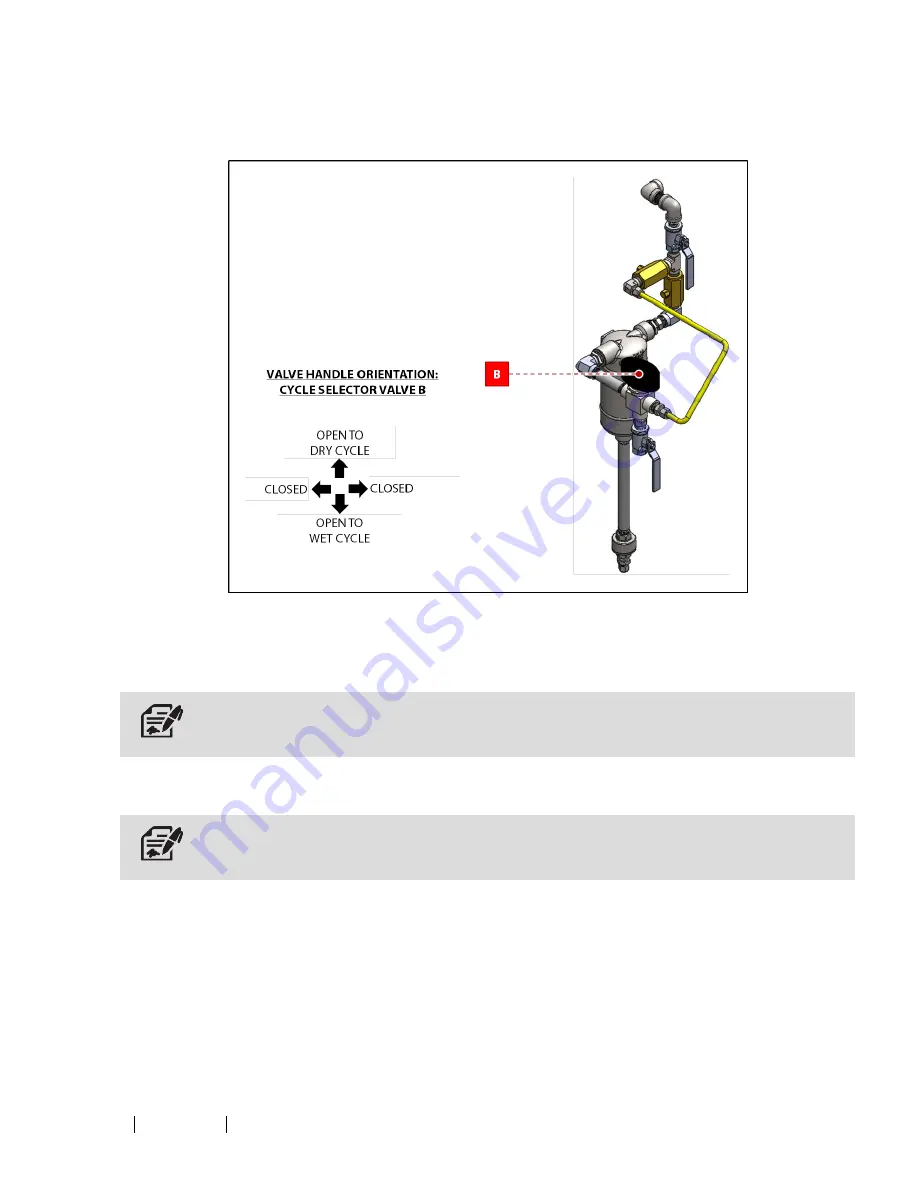
Wet Cycle
15.
Manually turn the handle on cycle selector valve B so that the arrow on the handle points away from the steam separator
(
). This will open the valve to the wet cycle.
Figure 6: Cycle Selector Valve B Orientation
16.
Open collection header wet cycle inlet valve F for all installed SCs (
or
).
17.
Open steam inlet valve A to start the wet cycle (
). Saturated contaminants will drain to the container connected
to the drain.
During the wet cycle, the steam generator generates saturated steam, which dissolves and flushes contaminants from the
sample cylinders.
18.
Allow the wet cycle to run for the appropriate amount of time.
The time required to completely clean the sample cylinders is dependent on the set temperature of the steam generator, the
water inlet pressure, the type of contaminant(s), and the number of sample cylinders.
19.
Once the sample cylinders are free of visible contaminants or considered clean in accordance with the end user's
specifications, close steam inlet valve A (
). This ends the wet cycle.
15
IOM-128
MODEL: CSVC
REV: B
13839 West Bellfort Street Sugar Land, TX 77498
welker.com
Service Department 281.491.2331