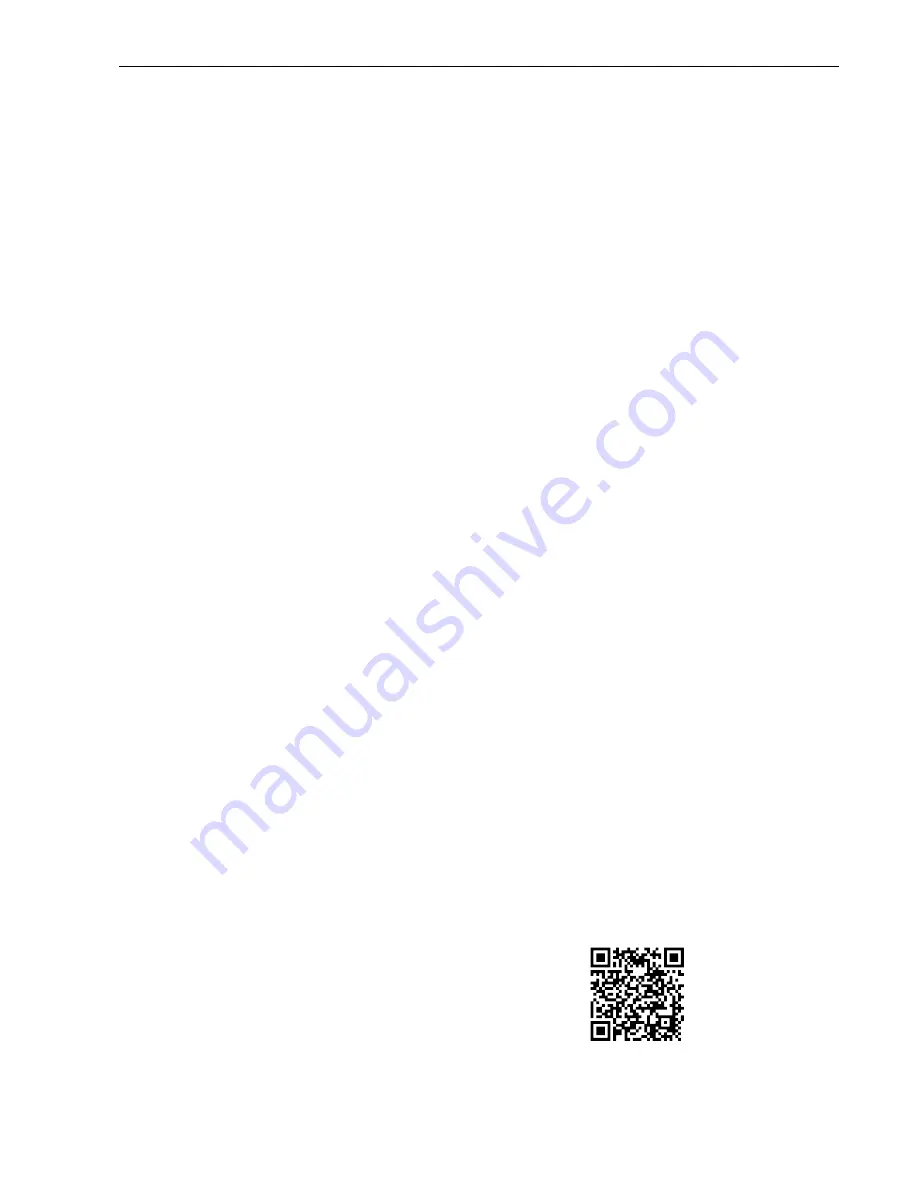
19
WT140ARC
Welding Machine
www.weldtech.net.nz
As part of an on-going commitment to excellence
in product support, Euroquip offers a comprehensive
product warranty program.
In order to qualify for full warranty support, your
product must be registered.
Product not registered with Euroquip is supported
by a base 12 month warranty only. Spare parts and
technical support will not be available for an unreg-
istered product outside of this base warranty period.
If a Euroquip dealer has not already registered your
product, please register it online at www.euroquip.
co.nz. Under ‘Contact Us’ link. To request a physical
registration form, please contact Euroquip customer
service on 0800 387 678.
Registered warranty period for the WT140ARC:
Commercial Use: 12 Months
Domestic Use: 24 Months
Warranty covers failure caused by manufacturing
and material defects in the product, during the war-
ranty period specified. The warranty period begins
when the product is purchased by the end user. War-
ranty is not transferrable and is only claimable by the
original purchaser.
Warranty does not cover parts that are subject to
wear and tear from usage.
Warranty covers failure of a product caused by defec-
tive materials and/or manufacturing for the period
given and the usage specified by Euroquip. The war-
ranty period begins when the product is purchased
by the end user. Warranty is not transferrable and is
only claimable by the original purchaser.
Warranty also does not cover failure caused by the
untimely replacement or service of the above wear-
ing parts. Evidence must be provided that the prod-
uct has been maintained and serviced suitably for a
claim to be considered under warranty.
Failure caused by incorrect operation of the product,
lack of proper care and maintenance of the product,
external damage, external circumstances such as
contaminated fuel or poor water supply, modifica-
tions to the product, attempted repair/ service by a
party other than an Approved Service Agent, is not
covered under warranty.
Warranty does not cover pre delivery service and ad-
justment, or failure that may occur as a result of lack
of/ incorrect pre delivery service and adjustment.
Warranty does not cover any incidental, indirect or
consequential loss, damage or expense that may re-
sult from any defect, failure or malfunction of a prod-
uct.
Should any issue be found to be a combination of a
warranty failure and a non-warranty issue, the repair
cost component to rectify and repair the non-warran-
ty failure is the customers’ full responsibility.
The decision that an issue with a product qualifies as
a warranty claim is made at the sole jurisdiction of Eu-
roquip.
No costs incurred will be considered under warranty
if repairs are carried out by a party other than a Euro-
quip Approved Service Agent, unless with prior con-
sent in writing from Euroquip.
It is the responsibility of the purchaser to deliver a
product under warranty to the nearest relevant ser-
vice agent or product reseller. Warranty does not cov-
er call outs, mileage and freight costs.
If a product is repaired under warranty, parts and
labour required for the repair will be supplied at no
charge. Warranty assessment and repair will be sched-
uled and executed according to the normal work flow
at the service location and depending on the avail-
ability of suitable replacement parts.
This warranty policy is an additional benefit and does
not affect the legal rights of any end user, reseller or
service agent.
Warranty
Scan here to register your product