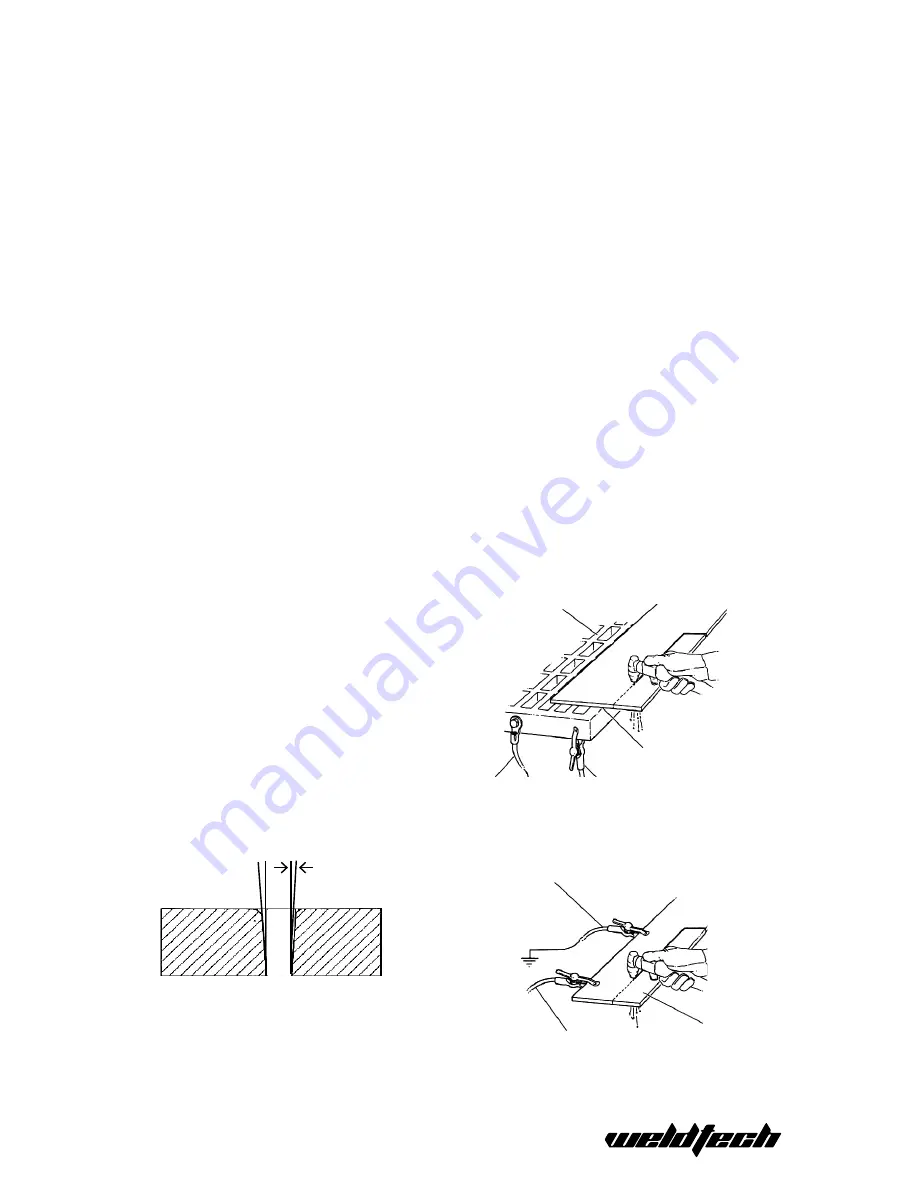
13
Grounded
work table
Be sure work is in good
contact with table
Earth ground
Work Cable
Grate Cutting
For rapid restarts, such as grate or heavy mesh
cutting, do not release the torch switch. This
avoids the 2 second preflow portion of the cutting
cycle.
Edge Starting
For edge starts, hold the torch perpendicular to
the workpiece with the front of the tip near (not
touching) the edge of the workpiece at the point
where the cut is to start. When starting at the
edge of the plate, do not pause at the edge and
force the arc to “reach” for the edge of the metal.
Establish the cutting arc as quickly as possible.
Drag Cutting
Position torch tip slightly above workpiece, press
torch switch and lower torch tip forward work-
piece until contact is made and cutting arc is
established. After cutting arc is established, move
the torch in the desired direction keeping the
torch tip slightly angled, maintaining contact with
the workpiece. Avoid moving too fast as would be
indicated by sparks radiating from the topside of
the workpiece. Move the torch just fast enough to
maintain sparks concentration at the underside
of the workpiece and making sure the material is
completely cut through before moving on. Adjust
drag speed as desired/required.
Direction of Cut
In the torches, the plasma gas stream swirls as it
leaves the torch to maintain a smooth column of
gas. This swirl effect results in one side of a cut be-
ing more square than the other. Viewed along the
direction of travel, the right side of the cut is more
square than the left.
Side Characteristics of Cut
Right Side
Cut Angle
Left Side
Cut Angle
To make a square – edged cut along an inside di-
ameter of a circle, the torch should move counter
clockwise around the circle. To keep the square
edge along an outside diameter cut, the torch
should travel in a clockwise direction.
Quality Cuts
Dross (slag) is the excess material that spatters
and builds- up on the underside of the work-piece
as you cut.
Dross occurs when the operating procedure and
technique is less than optimal. It will require prac-
tice and experience to obtain cuts without dross.
Although less than optimal cuts will contain dross,
it is relatively easy to remove by breaking it off
using pliers or chipping off with a chisel or scrap-
ing or grinding the finished cut as needed and is
generally only a minor inconvenience.
A combination of factors contributes to the build-
up of dross. They include; material type, material
thickness , amperage used for the cut, speed of
the torch across the work-piece, condition of the
torch tip, input line voltage, air pressure, etc. Gen-
erally there is an inversely proportional relation-
ship between output current and speed of cut.
Do not use more output current than is necessary
and adjust speed of cut toward minimizing dross
build-up on underside of cut. Experiment with
adjusting current and speed to minimize dross.
When dross is present on carbon steel, it is com-
monly referred to as either ‘high speed, slow
Earth ground
Do not attach
earth cable to
piece being
cut free
Work cable
Summary of Contents for SC40C
Page 1: ...OPERATING INSTRUCTIONS SC40C 40A INVERTER PLASMA CUTTER www weldtech net nz ...
Page 16: ...16 ...
Page 18: ...18 ...
Page 19: ...19 ...