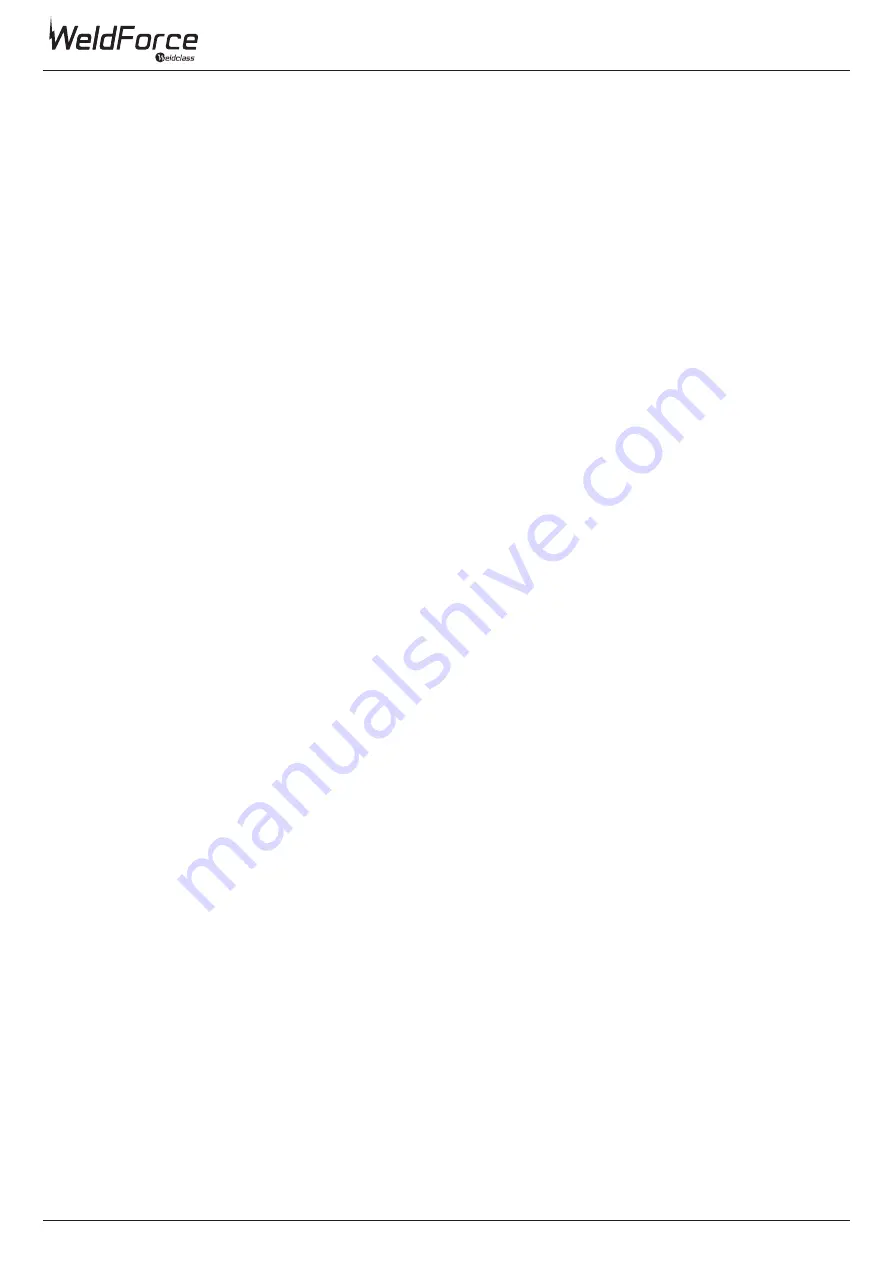
by
6
Power Supply
The WF-135S is designed to operate on a 10A 240V
AC power supply.
Electrical Connection
This machine has a wide input power variation
tolerance (~170-265V), allowing it to operate off
generator power. However, this machine is NOT
designed for
frequent
generator use and is NOT
protected against poor quality power or voltage
spikes. Any damage caused by generator power
supply is not covered under warranty.
If generator power must be used, generator size
should be not less than 7kva. Avoid using poor, low
quality generators as these have the greatest risk
of power spikes etc. A suitable quality generator
should have a THD (total harmonic distortion)
rating of not more than 6%. Most reputable
generator supplier will be able to specify the THD
ratings on their product.
Generator Use
If an extension cord must be used, it should be
minimum cable core size 2.0mm
2
for length of
up to 10m, or minimum 2.5mm2 for length up to
20m. Using extension leads of over 20m is not
recommended.
Extension Leads
Adequate ventilation is required to provide proper
cooling for the WF-135S. Ensure that the machine
is placed on a stable level surface where clean
cool air can easily flow through the unit. The WF-
135S has electrical components and control circuit
boards which may be damaged by excessive dust
and dirt, so a clean operating environment is
essential.
Operating Environment
Basic Operation - ARC/ MMA
1.1 Connect the earth cable quick connector to
the negative welding power output socket
(4) Connect the earth clamp to the work
piece. Contact with the work piece must be
a firm contact, with clean bare metal, with no
corrosion, paint or scale at the contact point.
1.2 Insert an electrode into the electrode holder
and connect the electrode holder and work
lead to the positive welding power output
socket (5).
NOTE:
This polarity connection configuration is valid
for most GP (General Purpose) MMA electrodes. There
are variances to this. If in doubt, check the electrode
specifications or consult the electrode manufacturer.
1.3 Connect the machine to suitable mains power
using the mains input power lead (6). Switch
the mains power switch (7) to ‘on’ to power up
the machine.
1.4 Select the required output current using the
current control knob (3). You are now ready to
weld!
Tips & Tricks
Welding duty cycle is the percentage of actual
welding time that can occur in a ten minute cycle.
E.g. 15% at 105 amps - this means the welder can
weld at 105 amps for 1.5 minutes and then the unit
will need to be rested for 8.5 minutes. All duty cycle
ratings are based on an ambient air temperature of
40°C with 50% humidity, which is the international
standard for such a rating.
In an environment with temperatures exceeding
40°C, the duty cycle will be less than stated. In
ambient temperature less than 40°C, duty cycle
performance will be higher.
The WF-135S is not designed to be used for lift TIG
operation, for lift TIG welding, the WF-140ST or WF-
180ST models are recommended.
For more useful tips & tricks on welding or selecting
the right tool for the job, please visit
www.weldclass.com.au
Duty Cycle Rating
Lift TIG Operation
Summary of Contents for WeldForce WF-135s stick
Page 13: ...13 MMA Stick Troubleshooting...