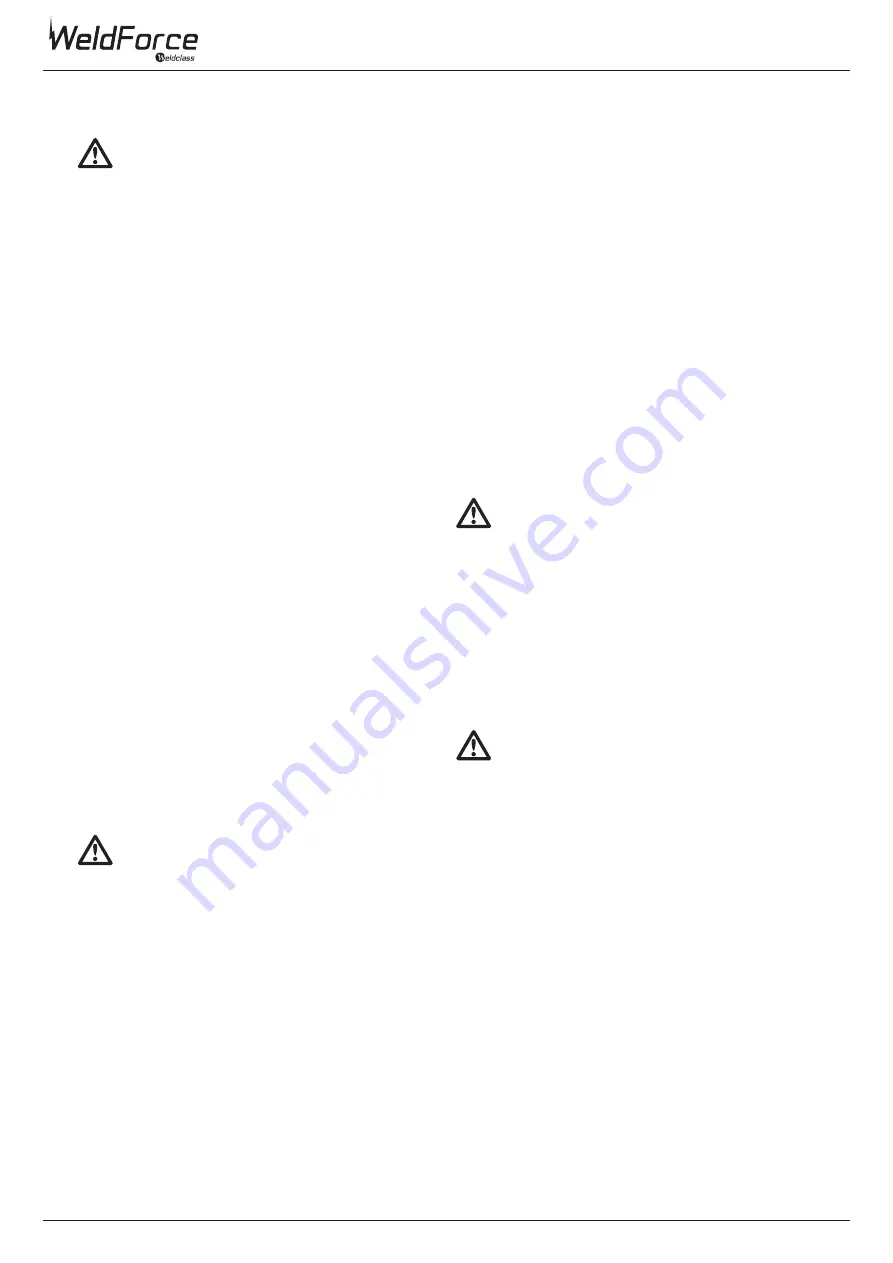
by
18
Accidental contact of electrode or welding wire to
metal objects can cause sparks, overheating, or
fire.
WARNING!
Sparks and spatter fly off from the welding arc.
The flying sparks and hot metal, weld spatter,
work piece, and hot equipment can cause fires
and burns.
Fire & Explosive Risks
1. Protect yourself and others from flying sparks
and hot metal.
2. Do not weld where flying sparks can strike
flammable material.
3. Remove all flammables within 10m of the
welding site.
4. Be alert that welding sparks and hot materials
from welding can easily go through small
cracks and openings to adjacent areas.
1. Keep your head out of the fumes. Do not
breathe the fumes.
2. If inside, ventilate the area and/or use an
exhaust at the arc to remove welding fumes
and gases. If ventilation is poor, use an
approved air-supplied respirator.
3. Read the Safety Data Sheets (SDS) and the
manufacturer’s instruction for the metals,
consumables, coatings, and cleaners.
4. Work in a confined space only if it is well
ventilated, or while wearing an air-supplied
respirator. Shielding gases used for welding
can displace air causing injury or death. Be
sure the breathing air is safe.
5. Do not weld in locations near degreasing,
cleaning, or spraying operations. The heat and
rays of the arc can react with vapours to form
highly toxic and irritating gases.
6. Do not weld on coated metals, such as
galvanized, lead, or cadmium plated steel,
unless the coating is removed from the
weld area, the area is well ventilated, and
if necessary, while wearing an air- supplied
respirator. The coatings and any metals
containing these elements can give off toxic
fumes if welded.
WARNING!
Gas cylinders contain gas under high pressure. If
damaged, a cylinder can explode. Since gas
cylinders are normally part of the welding
process, be sure to treat them carefully.
Cylinders
1. Protect compressed gas cylinders from
excessive heat, mechanical shocks, and arcs.
2. Install and secure cylinders in an upright
position by chaining them to a stationary
support or equipment cylinder rack to prevent
falling or tipping.
3. Keep cylinders away from any welding or
other electrical circuits.
4. Never allow a welding electrode to touch any
cylinder.
5. Use appropriate shielding gas, regulators,
hoses, and fittings designed for the specific
application; maintain them and their
associated parts in good condition.
6. Turn your face away from the valve outlet
when opening the cylinder valve.
5. Watch for fire, and keep a fire extinguisher
nearby.
6. Be aware that welding on a ceiling, floor,
bulkhead, or partition can cause fire on the
hidden side.
7. Do not weld on closed containers such as tanks
or drums. Connect the work lead/clamp to the
job as close to the welding area as practical to
prevent welding current from traveling long,
possibly unknown paths and causing electric
shock and fire hazards.
8. Do not use a welder to thaw frozen pipes.
9. Remove the stick electrode from the holder
or cut off the welding wire at the contact tip
when not in use.
Sparks & Hot Metal
WARNING!
Chipping and grinding causes flying metal, and
as welds cool they can throw off slag.
1. Wear an AS/NZS approved face shield or safety
goggles. Side shields are recommended.
2. Wear appropriate safety equipment to protect
the skin and body.
WARNING!
Welding produces fumes and gases. Breathing
these fumes and gases can be hazardous to
your health.
Fumes And Gases
Summary of Contents for WeldForce WF-135s stick
Page 13: ...13 MMA Stick Troubleshooting...