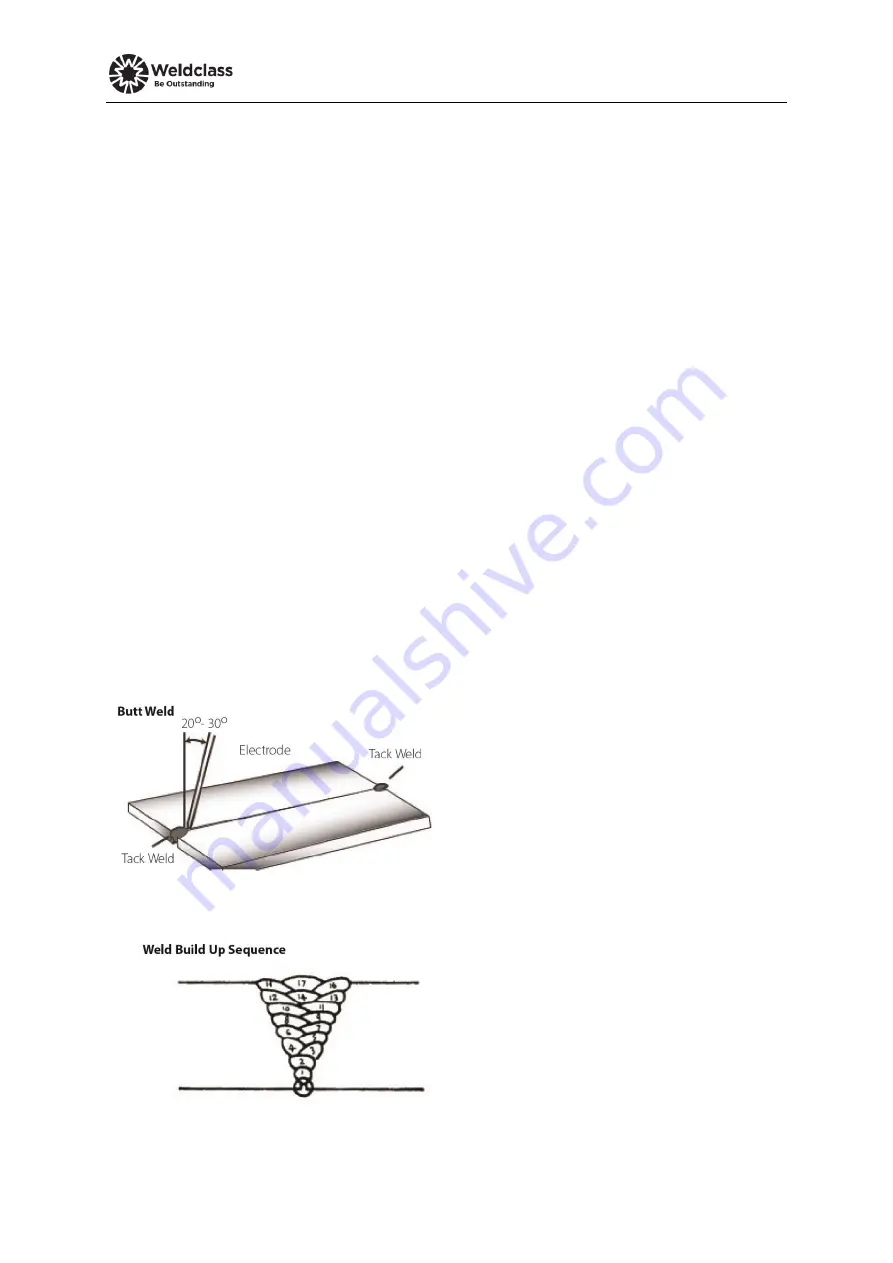
.
50
© Weldclass 2020 | E.&O.E.
12.8
Making Welded Joints
Having attained some skill in the handling of an electrode, you will be ready to go on to make up welded
joints.
12.8.1
Butt Welds
Set up two plates with their edges parallel, as shown in Figure 46, allowing 1.6mm to 2.4mm gap
between them and tack weld at both ends. This is to prevent contraction stresses from the cooling weld
metal pulling the plates out of alignment.
Plates thicker than 6.0mm should have their mating edges beveled to form a 70º to 90º included angle.
This allows full penetration of the weld metal to the root. Using a 3.2mm Weldclass 12V Stick electrode
at 100 amps, deposit a run of weld metal on the bottom of the joint.
Do not weave the electrode, but maintain a steady rate of travel along the joint sufficient to produce a
well-formed bead. At first you may notice a tendency for undercut to form, but keeping the arc length
short, the angle of the electrode at about 20º from vertical, and the rate of travel not too fast, will help
eliminate this.
The electrode needs to be moved along fast enough to prevent the slag pool from getting ahead of the
arc. To complete the joint in thin plate, turn the job over, clean the slag out of the back and deposit a
similar weld.
Heavy plate will require several runs to complete the joint. After completing the first run, chip the slag
out and clean the weld with a wire brush. It is important to do this to prevent slag being trapped by the
second run. Subsequent runs are then deposited using either a weave technique or single beads laid
down in the sequence shown in Figure 47. The width of weave should not be more than three times the
core wire diameter of the electrode.
When the joint is completely filled, the back is either machined, ground or gouged out to remove slag
which may be trapped in the root, and to prepare a suitable joint for depositing the backing run. If a
backing bar is used, it is not usually necessary to remove this, since it serves a similar purpose to the
backing run in securing proper fusion at the root of the weld.
Figure 46
Figure 47