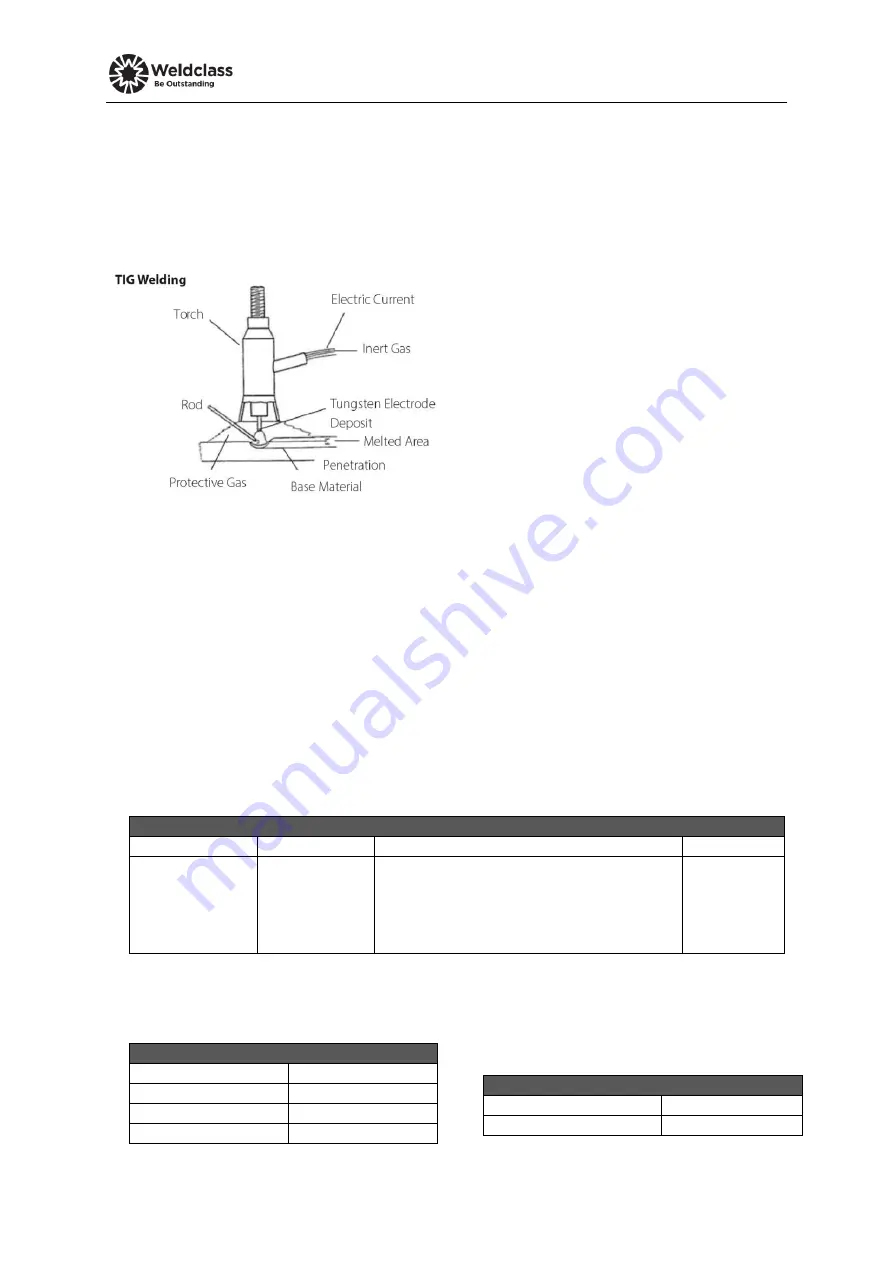
.
56
© Weldclass 2020 | E.&O.E.
13
TIG BASIC WELDING GUIDE
TIG Welding is a fusion procedure that uses an electric ARC created between an infusible tungsten electrode
and base material to be welded. For TIG welding an inert gas must be used (Argon) which protects the
welding bead. If filling material is used, it is made up of rods suitable to the material to be welded (steel,
stainless steel, copper etc.).
Figure 60
In TIG mode, welding is possible in all positions: flat, angle, on the edge, vertical and overhead.
Furthermore, with respect to other types of welding, the welding joint has greater mechanical resistance,
greater corrosion resistance and limited heating in the welded area which limits distortion. Welding can be
done even without weld material, guaranteeing a smooth, shiny weld with no impurities or slag.
13.1
TIG Electrode Selection and Preparation
13.1.1
Electrode Polarity
Connect the TIG torch to the negative (-) torch terminal and the work lead to the positive (+) work
terminal for direct current straight polarity. Direct current straight polarity is the most widely used
polarity for DC TIG welding. It allows limited wear of the electrode since 70% of the heat is concentrated
at the work piece.
Tungsten Electrode Types
Electrode Type
Application
Features
Colour Code
Rare-Earth
(Weldclass RE4)
All metals*
High-Performance, suitable for both DC (Steel,
Stainless steel etc) and AC (Aluminium)* TIG
welding. Maintains tip shape, reliable arc
striking, low burn off rate, long service life and
smooth/stable arc.
Purple
Table 18
* Note that the Weldforce 175MST machine is only capable of DC TIG welding. It cannot perform AC TIG
welding required to weld Aluminium.
Tungsten Electrode Current Ranges
Electrode Diameter
DC Current (Amps)
1.6mm (1/16”)
60 – 115
2.4mm (3/32”)
100 – 165
3.2mm (1/8”)
135 – 200
Table 19
Guide For Selecting Filler Wire Diameter
Filler Electrode Diameter
DC Current (Amps)
1.6mm (1/16”)
20 – 90