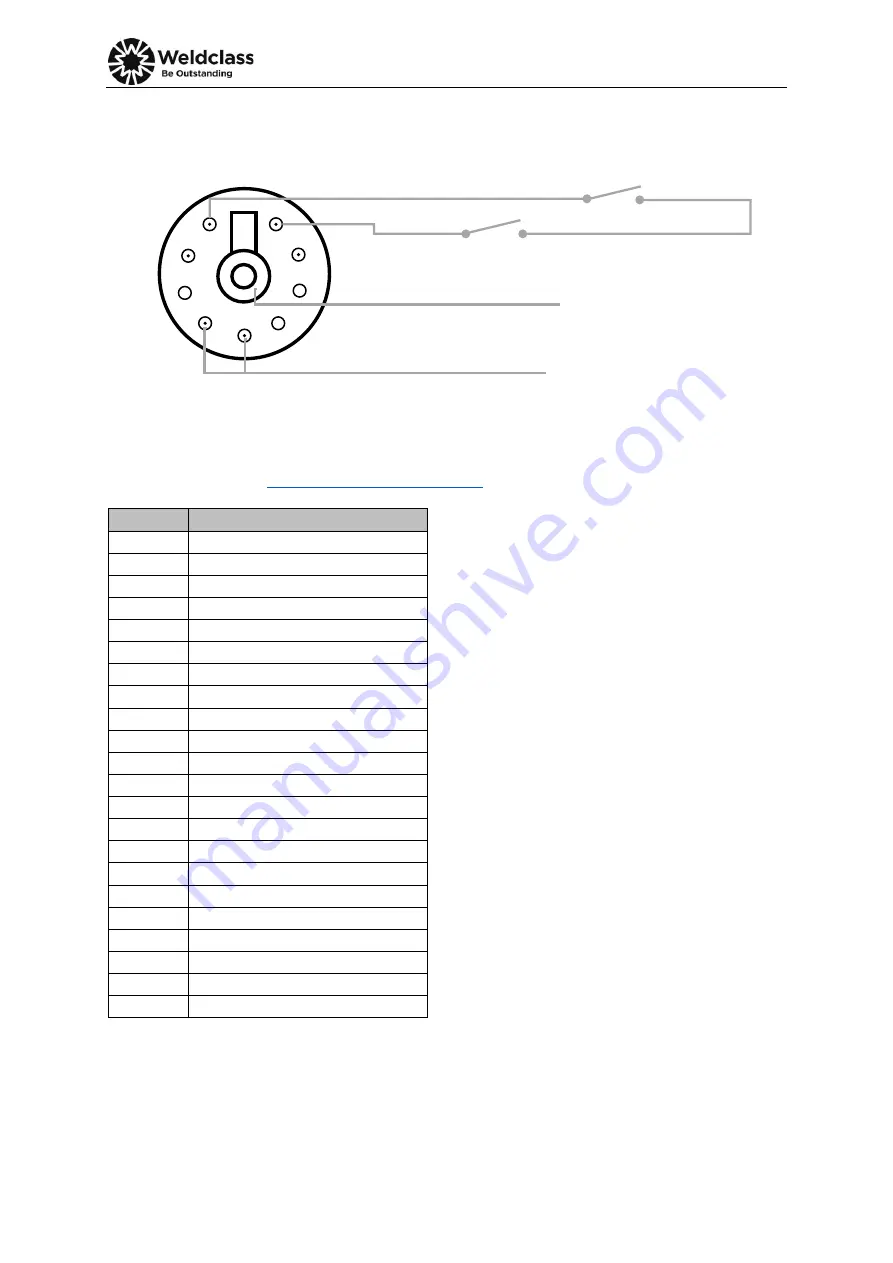
.
18
© Weldclass 2020 | E.&O.E.
8.3
Plasma Torch Pin Configuration
8.4
Machine Spare Parts for 43P
or contact your Weldclass distributor.
Ref.
Description
1
Thermostat
2
Solenoid Valve
3
Air Pressure Regulator
4
Earth Lead + Dinse
5
Mains Power Cable
6
Cooling Fan
7
Earth Clamp
8
Torch Connection Socket
9
Plasma Torch
10
Snap-in Capacitor Kit
11
IGBT + Diode Kit
12
Power PCB kit
13
Front panel PCB Kit
14
Metal Panel Kit
15
Diodes Kit
16
Control PCB kit
17
Power Supply Components Kit
18
Aux Components Kit
19
Power Switch
20
Dinse Socket
21
Potentiometer Kit
22
Plastic Panel Kit
Table 6
1
2
6
5
4
3
8
9
7
Trigger
Cap Safety Switch
Pilot Arc
Cutting Current