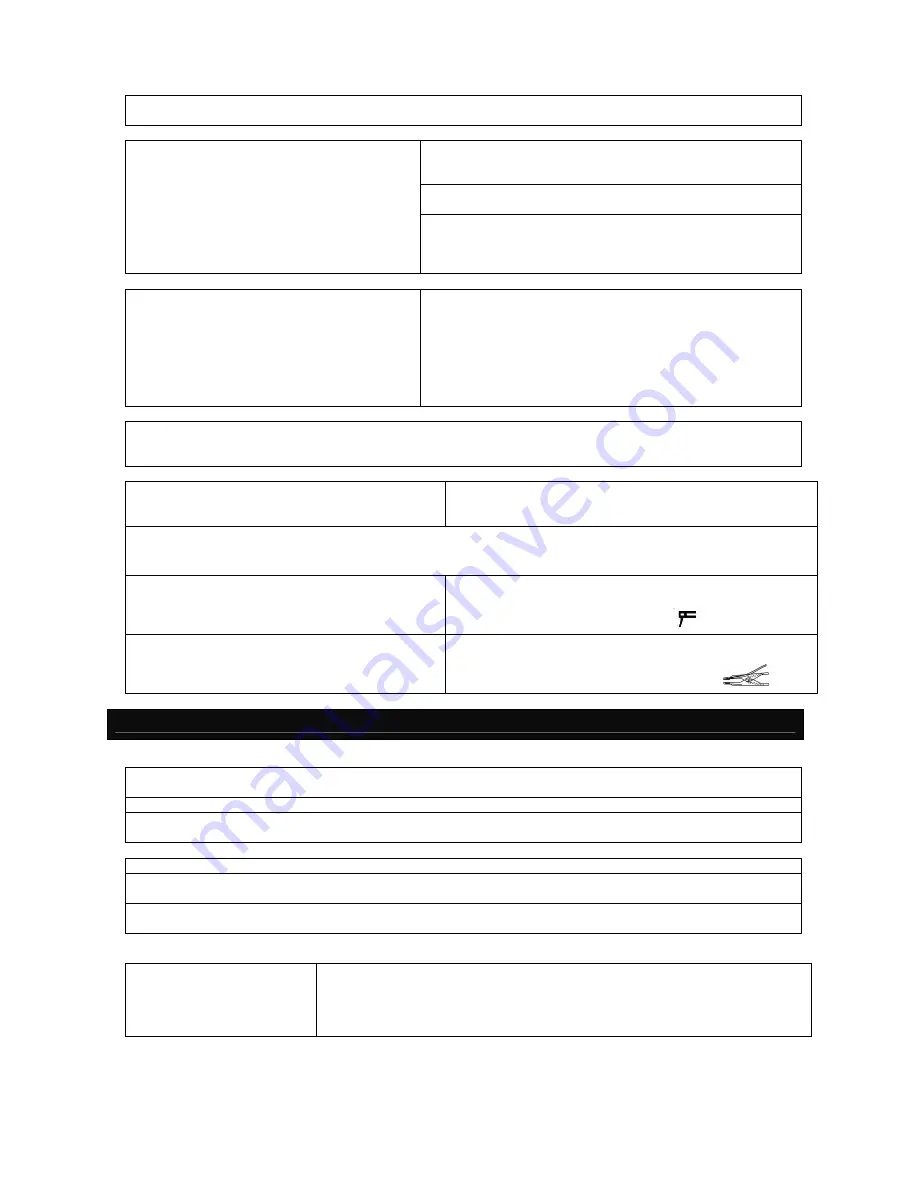
Page
7
of
10
WARNING! POSITION THE WELDING MACHINE ON A FLAT SURFACE WITH SUFFICIENT CARRYING
CAPACITY FOR ITS WEIGHT, TO PREVENT IT FROM TIPPING OR MOVING HAZARDOUSLY.
Before making any electrical connection, make sure the rating
data of the welding machine correspond to the mains voltage
and frequency available at the place of installation.
The welding machine should only be connected to a power
supply system with the neutral conductor connected to earth.
CONNECTION TO THE MAIN
POWER SUPPLY:
To comply with the requirements of the EN 61000-3-11 (Flicker)
welding procedure standard we recommend connecting the
welding machine to interface points of the power supply that
have an impedance of less than Zmax =0,2 ohm.
PLUG
AND
OUTLET.
(FOR WELDING MACHINES WITHOUT A
PLUG)
:
Connect a normalised plug (2P + T) having sufficient capacity to
the power cable and prepare a mains outlet fitted with fuses or
an automatic circuit-breaker; the special earth terminal should
be connected to the earth conductor (yellow-green) of the power
supply. Table 1 (TAB.1) shows the recommended delayed fuse
sizes in amps, chosen according to the max nominal current
supplied by the welding machine, and the nominal voltage of the
main power supply.
WARNING!
Failure to observe the above rules will make the (Class 1) safety system installed by the manufacturer
ineffective with consequent serious risks to persons (e.g. electric shock) and objects (e.g. fire).
CONNECTION
OF
THE
WELDING
CABLES
Table 1 (TAB. 1) gives the recommended values for the
welding cables depending on the maximum current supplied by
the welding machine.
WARNING! BEFORE MAKING CONNECTIONS MAKE SURE THE WELDING MACHINE IS SWITCHED OFF AND
DISCONNECTED FROM THE POWER SUPPLY OUTLET.
CONNECTING THE ELECTRODE-HOLDER
CLAMP WELDING CABLE
The electrode holder clamp (Fig F) is connected to the machine
via a direct cable or a cable via a terminal. In either case the
cable or terminal pole has the symbol:
CONNECTING THE WELDING CURRENT
RETURN CABLE
The welding current return clamp (Fig E) is connected to the
machine via a direct cable or a cable via a terminal. In either
case the cable or terminal pole has the symbol:
These welding machines consist of a drooping specification, and are suitable for welding with alternating current
using coated electrodes (E 43 R type) based on the diameters given on the data plate.
To switch on the welding machine operate the main switch (Fig. B-1).
The intensity of the supplied welding current can be adjusted continuously, by means of a manually operated
magnetic shunt (Fig. B-2), or step-by-step by means of a manually operated switch (Fig. B-3).
CHECK THE WELDING MACHINE MODEL
N.B. In the case of a welding machine with switch, current adjustment should be carried out with the main switch (Fig.
B-1) in the O position (off).
The value of the current setting, (I2) can be read in Amps on the graduated scale (Fig. B-4) on the top or side panel
of machines where it is provided.
THERMOSTATIC
PROTECTION
This welder is automatically protected from thermic overheating (thermostat
automatic re-start). When the windings reach performance temperature, the
protections cut off the supply circuit, igniting the yellow lamp on the front panel (B-5).
After a few minutes cooling the protection will reopen the supply line and turn off the
yellow lamp. The welder is ready for further use.
SECTION 8 : WELDING: DESCRIPTION OF THE PROCEDURE