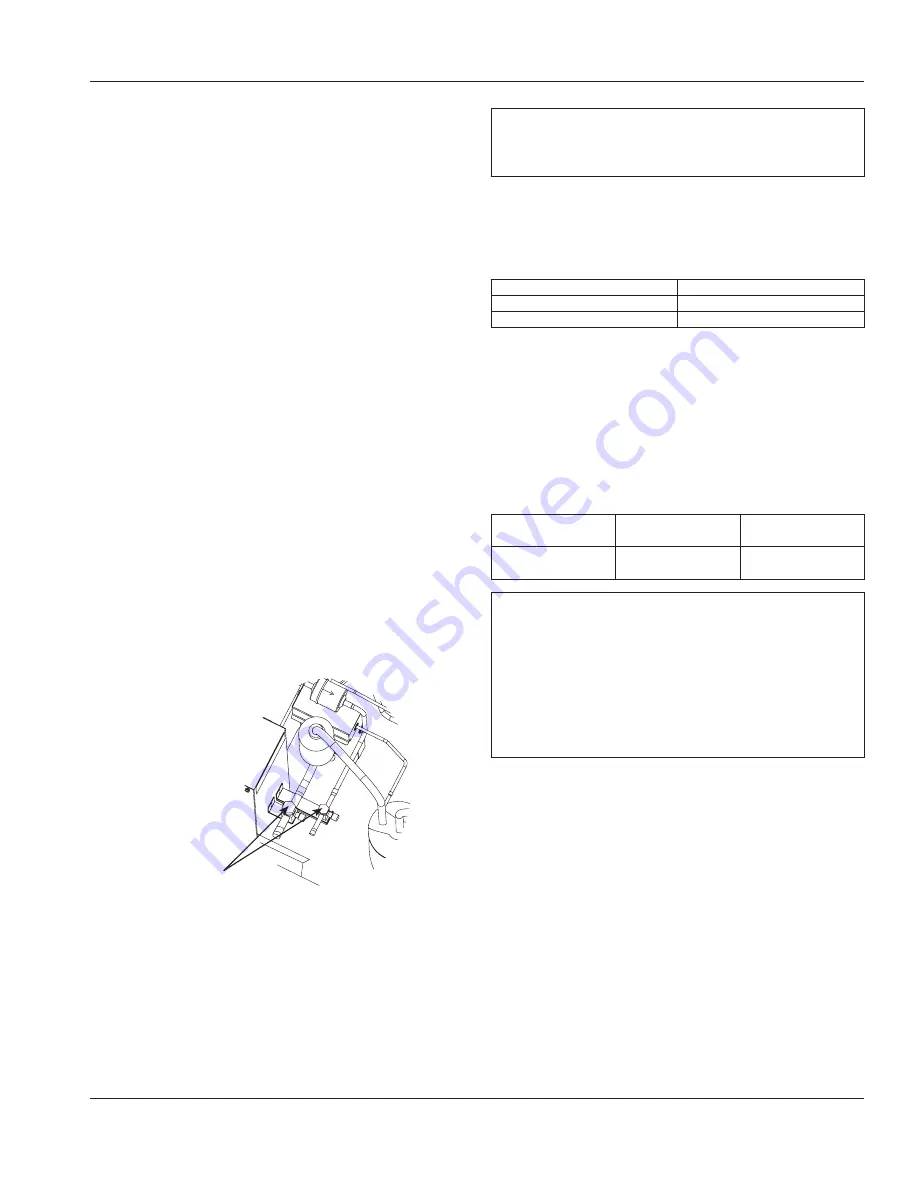
Part Number 000016034 Rev 00 07/19 21
Step 5 Pressure Test and Evacuate Line Set and Ice
Machine Head Section
• Pressure testing and evacuation can be performed from
the ice machine head section or CVD condensing unit
shut-off valves.
• Schrader valve core removal tools that allow for removal
and installation of the valve cores without removing
manifold gauge set hoses are recommended to decrease
the evacuation time.
• Pressure test @ 1000 kPa for a minimum of 15 minutes.
• Minimum evacuation level is 500 microns.
Step 6 Leak Check the Refrigeration System
Leak check the new line set connections at the ice machine
head section, condensing unit and S trap as well as all factory
joints throughout the entire system. Disconnect power to the
remote condensing unit. Place the rocker switch into the ON
position. This allows the low side and high side pressures to
equalize for leak checking. Place the rocker switch in the OFF
position. Connect power to the remote condensing unit and
allow system to pump down after leak checking is complete.
Step 7 Open the Valves Prior to Starting the Ice
Machine
If the valves were not opened during the installation process,
they must be opened before operating the ice machine.
A. Backseat (open-turn counterclockwise) the suction
line shutoff valve.
B. Backseat (open-turn counterclockwise) the liquid
line shutoff valve.
Verify suction and liquid line
shut-off valves are open before
operating the ice machine
Important
All refrigeration valve caps must be reinstalled to prevent
future refrigeration leaks.
Verify O-ring in Schrader valve caps are intact and reinstall on
shutoff valves to prevent refrigerant leakage. Replace shutoff
valve access caps and torque to the following specifications.
Torque Values
Stem
24.4-27.1 Nm
Caps
16.3-20.3 Nm
Schrader Core
0.17-0.34 Nm
Step 8 Insulation Requirements
To prevent condensation, the entire suction line must be
insulated. All insulation must be airtight and sealed at both
ends.
The following insulation requirements prevent condensation
at 32°C ambient 90% Relative Humidity. If higher humidity is
expected, increase insulation thickness.
The entire suction line set requires:
Suction Line
Liquid Line
Min. Insulation
Thickness
16 mm
10 mm
9 mm Suction Line
9 mm Liquid Line
Important
To prevent condensation, the entire suction line must be
insulated. All insulation must be airtight and sealed at
both ends.
The minimum requirements are for conditions at or below
90% humidity and 32°C ambient. When higher humidity
will be experienced, or local code requires, insulation wall
thickness will need to be increased.