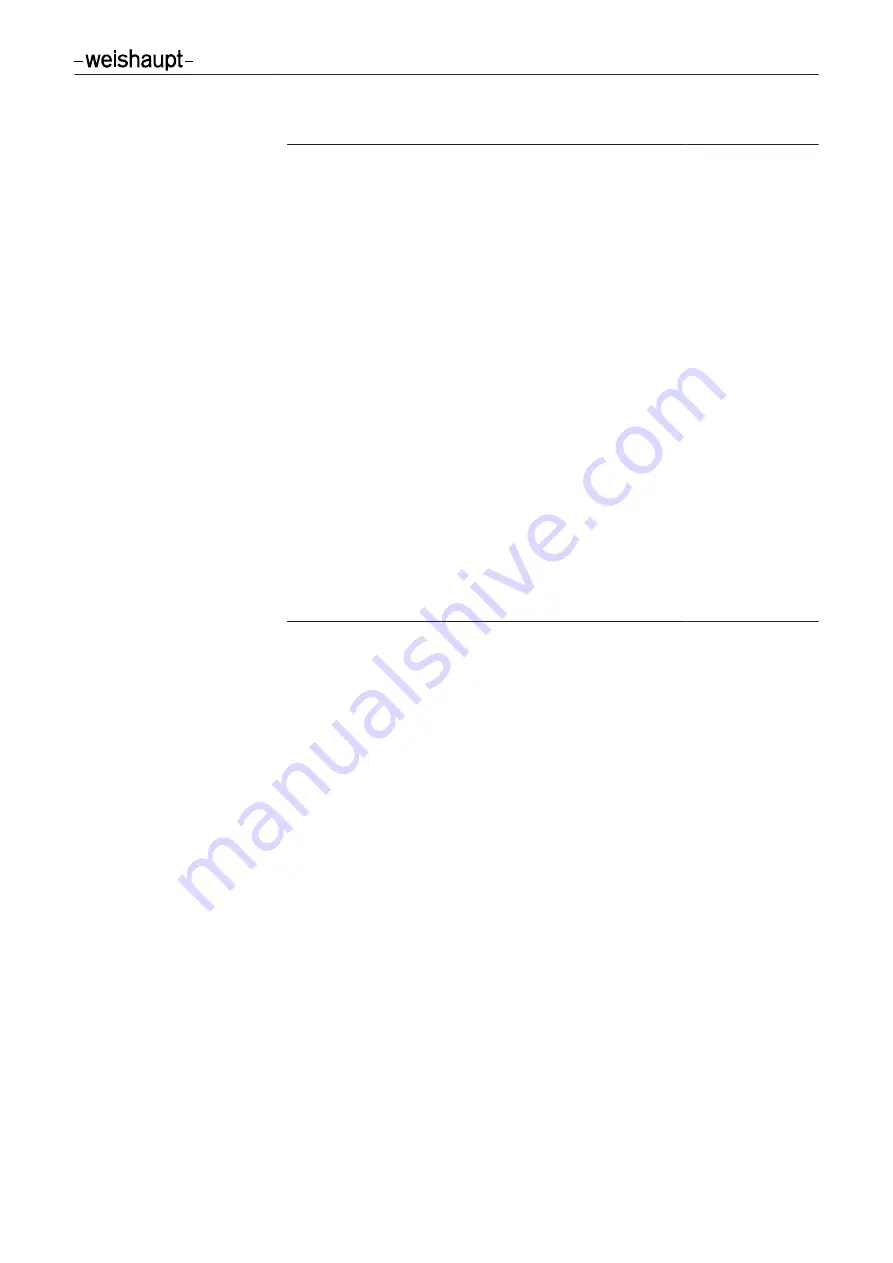
Pos.
Description
Order No.
2.28
Sludge separator complete with G½'' ball valve
511 506 00 02 2
2.29
G½'' ball valve for sludge separator
511 506 00 03 2
2.30
Distributor assembly pump HE, complete with seal
and ball valve
511 506 00 04 2
2.31
Non return valve complete
511 506 00 10 2
2.32
Circulation pump with plug complete
(heating circuit)
– WWP L 7 and WWP L 11
511 502 02 28 2
– WWP L 15
511 502 02 52 2
2.33
Circulation pump with plug complete
(domestic water feed pump)
511 502 02 29 2
2.34
Sealing washer 32 x 44 x 2 (1½")
482 301 30 43 7
2.35
Pump inlet free-floating
511 502 02 34 2
2.36
Union nut G1½'' x 42, L=18
511 502 02 36 7
2.37
Seal set pipe assembly
511 506 00 11 2
– 2 x O ring 20 x 1.5
– 2 x seals G1
– 3 x seals G1½''
2.38
Cladding distributor WWP 6-piece
511 506 00 01 2
2.39
Condensate hose
511 505 01 10 7
2.40
Flare nut connection set
511 505 01 33 2
– Flare nut connection SAE 5/8"
– Flare nut connection SAE 3/8"
Installation and operating instruction
Hydraulic unit WWP L 7 ... L 15
11 Spares
83279602 • 1/2014-05 • La
51-59