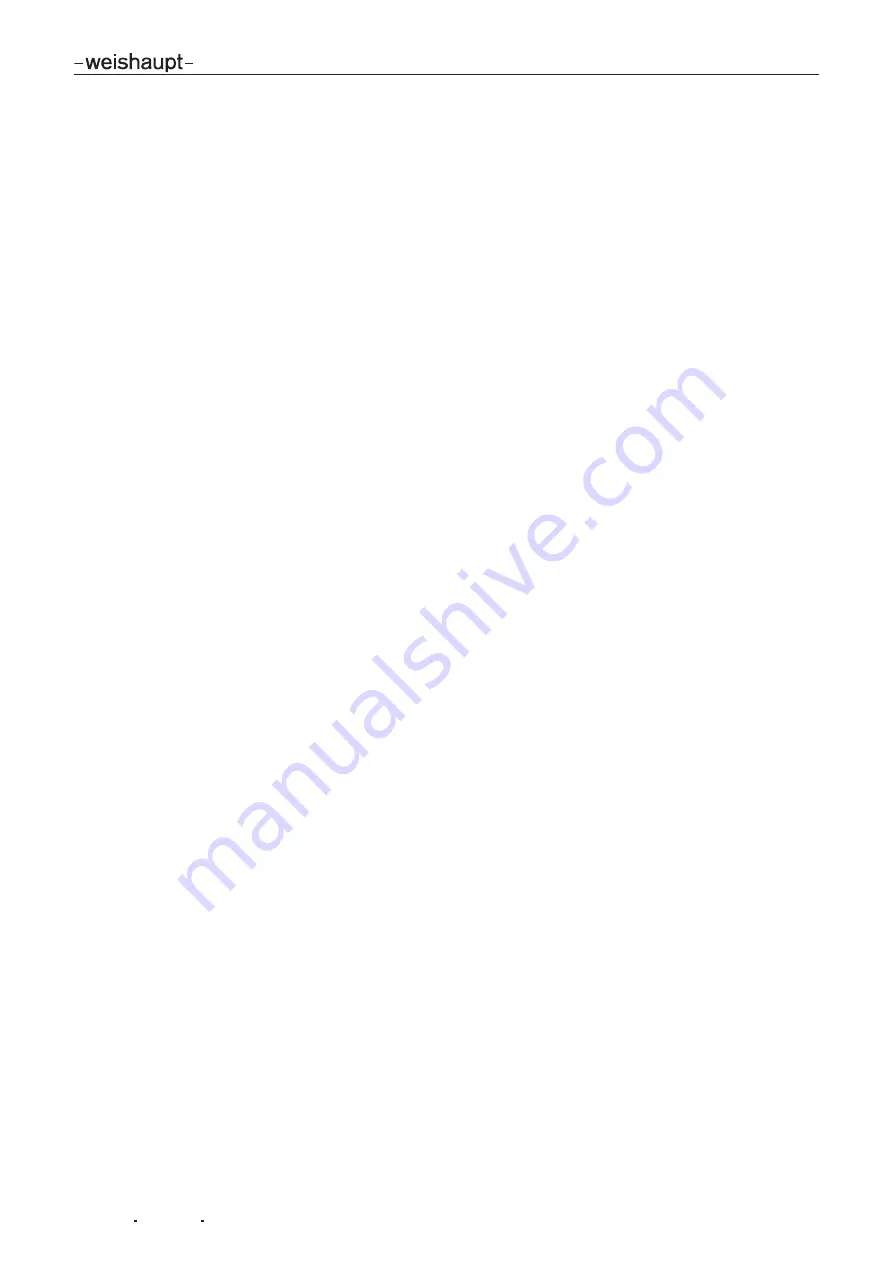
Installation and operating instruction
Oil burner WM-L20/2-A R (W-FM100/200)
3 Product description
83252902 1/2019-09 La
12-84
3.3.3 Electrical components
Combustion Manager
The combustion manager W-FM is the control unit of the burner.
It controls the sequence of operation, monitors the flame and communicates with all
components.
Display and operating unit (ABE)
The ABE is used to display and alter the operational values and parameters of the
combustion manager. It is connected by connection line and can be remove from
the burner.
Burner motor
The burner motor drives the fan wheel and the oil pump.
Without variable speed drive the combustion manager controls a contactor or star
delta switching.
With variable speed drive, a frequency converter is connected upstream.
Ignition unit
The electronic ignition unit creates a spark at the electrode, which ignites the fuel/
air mixture.
Flame sensor
The combustion manager monitors the flame signal via the flame sensor.
If the flame signal becomes too weak, the combustion manager carries out a con-
trolled shutdown.
See installation and operating manual of the Combustion Manager W-FM for flame
signal required.
Limit switch
The limit switch in the housing prevents burner start in the open position.