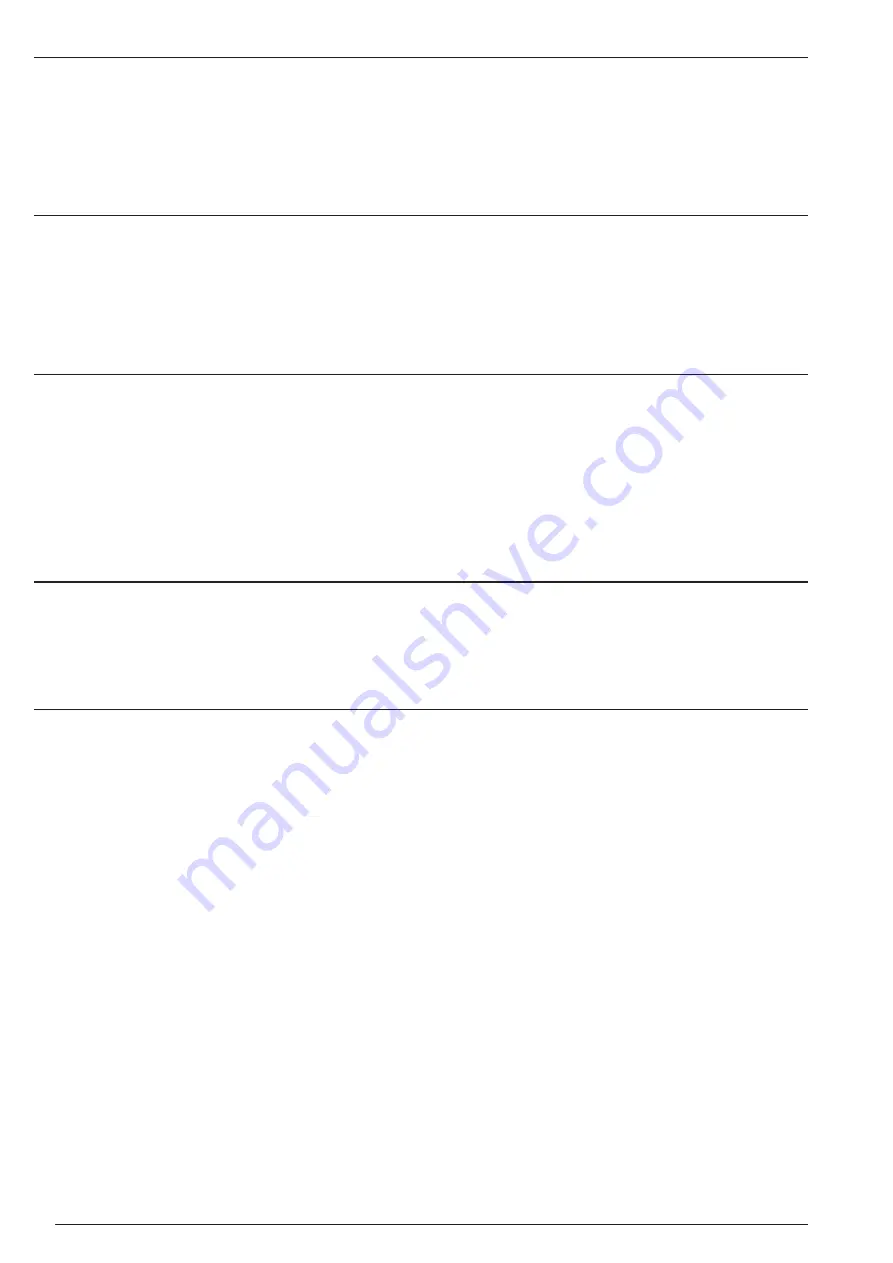
22
Condition
Cause
Rectification
Combustion head
Heavy soot deposits
Defective nozzle
Replace nozzle
Burner incorrectly set
Correct settings
Amount of combustion air changed
Reset burner
Boiler room insufficiently ventilated
Ensure sufficient boiler room
ventilation as per local regulations
Diffuser
heavily soiled
Burner incorrectly set
Correct settings of mixing head
(CH. 7.5) and check burner setting
Wrong nozzle
Chose different nozzle, if stability
allows use 45° nozzle
Pump pressure too high
Select next larger nozzle size and
adjust pump pressure
Voltage supply
Signal lamp flashes orange / red
Voltage supply low voltage < 170 V
Check external supply voltage
Internal fuse F7 has tripped
Replace fuse (6·3A slow)
(see Ch. 7.13)
Signal lamp flashes 3 x red/orange
Voltage supply has excess
Check external voltage supply
then short pause
voltage > 260 V
Signal lamp remains off at
No voltage available
Check voltage supply
heat request from boiler control
Combustion manager defective
Replace combustion manager
Solenoid valve
Solenoid valve does not open
Coil defective
Replace coil
Signal lamp flashes red/green
Extraneous light
Find source of light and eliminate
Solenoid valve does not close
Foreign particles on valve seat
Replace oil pump
tightly
or in the protective filter
Servomotor
Servomotor does not run
Plug connection incorrect
Check plug connection
Servomotor defective
Replace servomotor (CH. 7.11)
Servomotor starts briefly,
Setting of limit switches incorrect
Correct setting of limit switches,
then goes to lockout
closed, partial load and switch point
(ST0/ST1/MV2) must not be set
above full load (ST2).
Switch point (MV2) must not be set
below partial load (ST1).
Servomotor does not run to
Servomotor defective
Check servomotor, if necessary
the set limit switch value
replace
Air damper or angle drive seized
Check air damper and angle drive
and replace if necessary