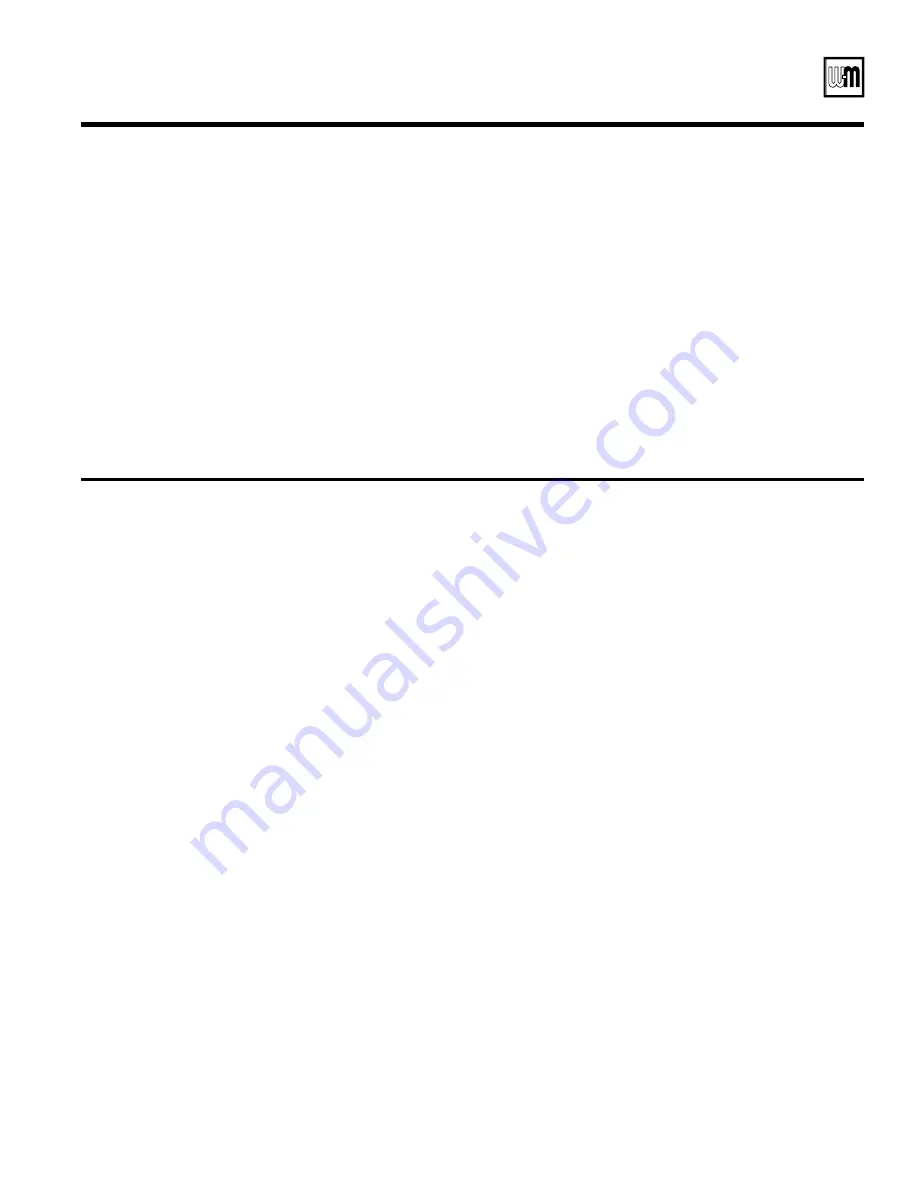
Part number 550-141-396/0801
9
PER Series 3 Electric-Hydronic Boilers Installation Instructions
Checkout procedure
After filling and purging, start the boiler as follows:
❏
Turn the thermostat to its lowest setting so that there is no call for
heat.
❏
Set the limit control as recommended in the Installation Instructions.
❏
Turn on the main electric switch to the boiler.
❏
Set the thermostat above actual room temperature. Check for proper
sequencing of elements. Heat the entire system to about 200°F so that
dissolved air and gases in the system water will be emitted and vented.
❏
Check limit control operation by lowering the
control settings as described in the
“Troubleshooting” section on page 7.
❏
Restore the limit control settings to their
recommended values and set the thermostat to the
desired room temperature.
❏
Fill in “Installation and service certificate” below.
❏
If the boiler operates incorrectly or fails to start,
refer to “Troubleshooting” on page 7.
Boiler model __________________ Series __________ CP number ___________ Date installed _______________
Measured Btuh input ____________
Installer ________________________ ________________________________ ______________________________
(company) (address) (phone)
_____________________________________
(installer’s signature)
Installation and service certificate
❏
Installation instructions have been followed.
❏
Checkout sequence has been performed.
❏
Above information is certified to be correct.
❏
Information received and left with owner/maintenance person.