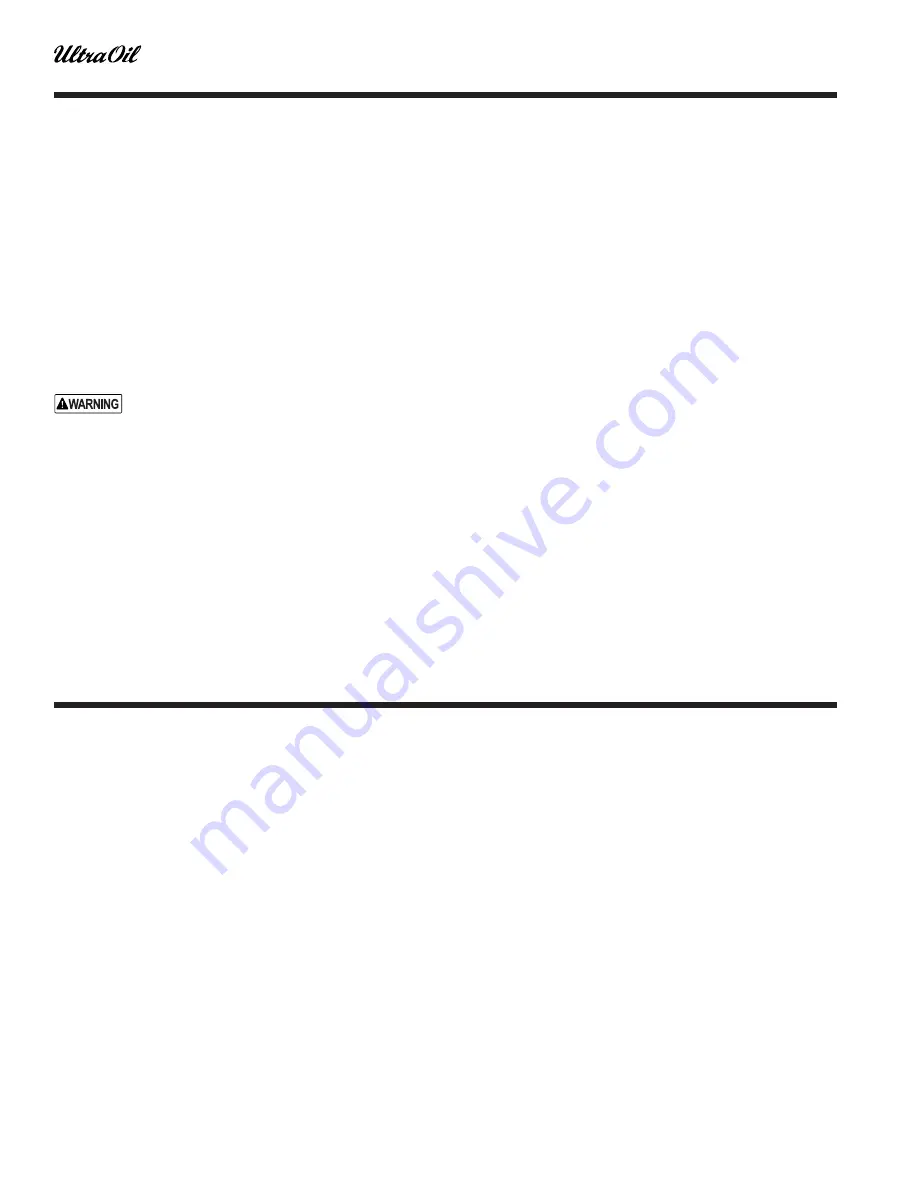
®
Series 3
WATER
BOILER
— Boiler Manual
Check-out procedure
❏
1. Boiler and heat distribution units fi lled with water?
❏
2. Automatic air vent, if used, opened one full turn?
❏
3. Air purged from system? Piping checked for leaks?
❏
4. Air purged from oil piping? Piping checked for leaks?
❏
5. Burner door closed, sealed and bolts tight? Observation
port bolt tight? Burner harness plugged in and boiler
ON/OFF switch on?
Obtain gas-tight seal to prevent possible fl ue gas
leakage and carbon monoxide emissions, leading
to severe personal injury or death.
❏
6. Proper draft and burner fl ame? Final adjustment made
with combustion test equipment?
❏
7. Test limit control: While burner is operating, adjust limit
control below actual boiler water temperature. Burner
should go off while circulator continues to operate. Raise
setting on limit control above water temperature and
burner should re-ignite.
❏
8. Test additional fi eld-installed controls: If boiler has a low
water cutoff, additional high limit or other controls, test
for operation as outlined by manufacturer. Burner should
be operating and should go off when controls are tested.
When controls are restored, burner should re-ignite.
❏
9. Limit control set to system temperature requirements
(max. 220 °F)?
❏
10. For multiple zones, fl ow adjusted to distribute heat in all
zones?
❏
11. Thermostat heat anticipator setting (if available) set
properly? Refer to “Thermostat wiring,” page 19.
❏
12. Boiler cycled with thermostat? Raise to highest setting and
verify boiler goes through normal start-up cycle. Lower
to lowest setting and verify boiler goes off.
❏
13. Observed several operating cycles for proper operation?
❏
14. Set room thermostat(s) to desired room temperature?
❏
15. Completed
Installation Certifi cate
below?
❏
16. Reviewed User’s Information Manual with owner or
maintenance person and instructed person to keep for
future reference?
❏
17. Returned all instructions provided with boiler to its en-
velope and placed with boiler for future reference?
Installation Certifi cate
Boiler model
__________________________ Series _________
CP number
_______________________
Date installed
__________________________________________
Nozzle size, GPH ____________ Fuel unit pressure, PSIG __________
❏
Installation instructions have been followed.
❏
Check out sequence has been performed.
❏
Above information is certifi ed to be correct.
❏
Information received and left with owner/maintenance person.
Installer
________________________________ (company) ________________________________ (phone)
________________________________ (address)
________________________________ (address)
_______________________________________
(Installer’s signature)
Comments:
_______________________________________
_______________________________________
_______________________________________
_______________________________________
_______________________________________
_______________________________________
Part number 550-142-182/1014
24