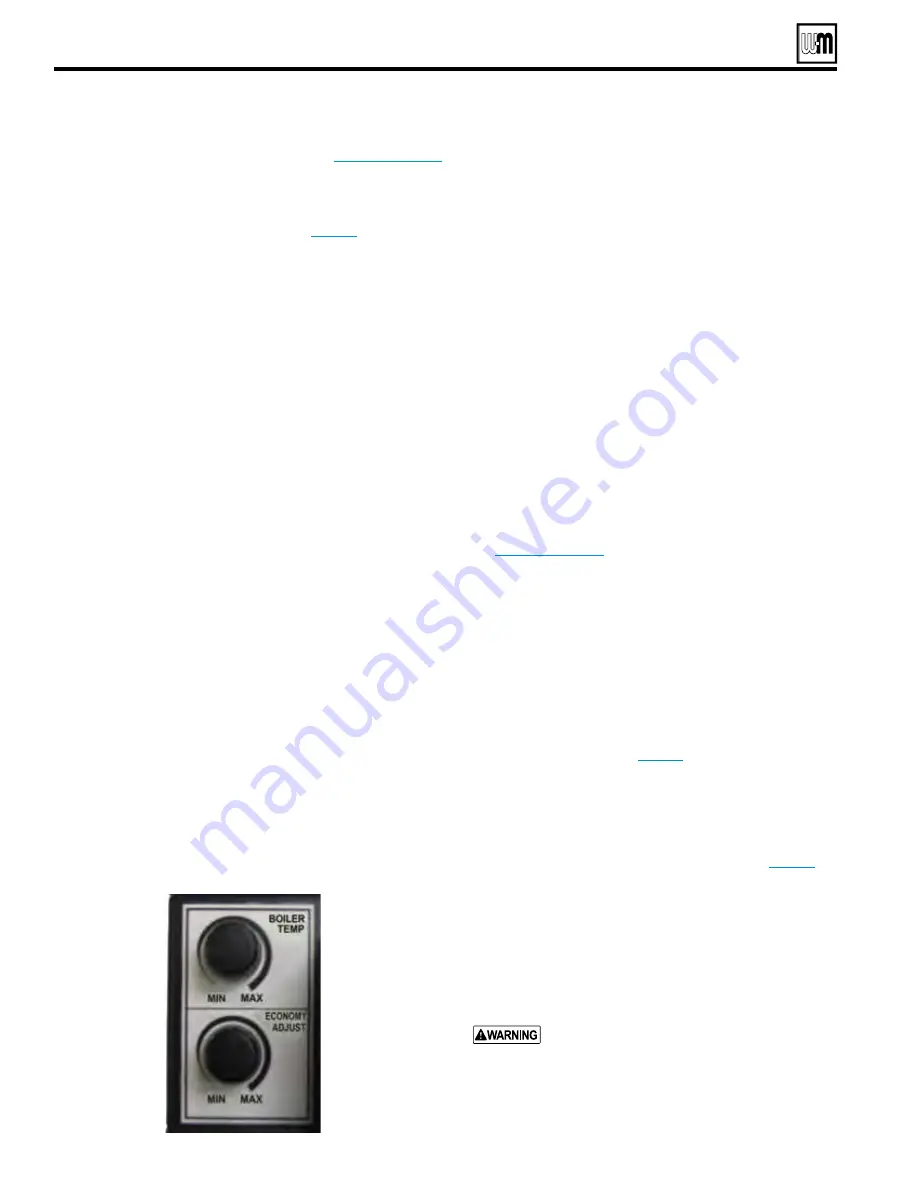
Part number 550-143-010/1021
62
GV90+
series
2
gas-fired water boiler – boiler manual
Final checks before starting boiler
Review the boiler sequence of operation in
.
Verify that the boiler and system are full of water and all system
components are correctly set for operation.
High altitude locations (over 5,500 feet) — verify that the high
altitude pressure switch is installed per
Verify that condensate trap has been filled with water.
Verify electrical connections are correct and securely attached.
Inspect vent piping and air piping for signs of deterioration from
corrosion, physical damage or sagging. Verify air piping and
vent piping are intact and correctly installed per this manual.
Adjust boiler control settings
BOILER OPERATING TEMPERATURE
With power turned on, control module receives a signal from
the temperature/LWCO sensor and displays boiler temperature.
The control knob labeled
BOILER TEMP
is used to adjust the
operating temperature setpoint, turning clockwise to increase
temperature setting and counterclockwise to decrease. When the
knob is turned to adjust temperature the display will brighten to
indicate adjustment mode. After temperature is set to desired
value, display will dim after approximately 5 seconds to indicate
measurement mode.
• ADJUST BOILER OPERATING TEMPERATURE TO
DESIRED SETPOINT.
BOILER ECONOMY SETTING
To comply with Department of Energy regulations, the control
module circulates available hot water before turning on the boiler to
attempt to satisfy a call for heat. While attempting to satisfy the heat
demand, the control module also monitors the boiler temperature
changes via the temperature/LWCO sensor and determines whether
or not the available hot water will satisfy the demand, adjusting the
time delay to turn on the boiler until it determines that additional
heat will be needed. The knob labeled
ECONOMY ADJUST
provides an adjustment between maximize
(MAX)
and minimize
(MIN)
the delay. The maximum
(MAX)
adjustment position
should be used to maximize energy savings. Turning the knob
counterclockwise decreases the delay time and should only be used
in the event that the heated space becomes uncomfortable.
• ADJUST ECONOMY TO DESIRED POSITION (MAX IS
THE PREFERRED SETTING).
IMPORTANT
In accordance with Section 325 (f) (3) of the Energy Policy
and Conservation Act, this boiler is equipped with a feature
that saves energy by reducing the boiler water temperature
as the heating load decreases. This feature is equipped with
an override which is provided primarily to permit the use of
an external energy management system that serves the same
function.
THIS OVERRIDE MUST NOT BE USED UNLESS AT LEAST
ONE OF THE FOLLOWING CONDITIONS IS TRUE:
• An external energy management system is installed
that reduces the boiler water temperature as the
heating load decreases.
• This boiler is part of a modular or multiple boiler
system having a total input of 300,000 BTU/hr or
greater.
• This boiler is equipped with a tankless coil.
To start the boiler
1. Turn OFF the boiler ON/OFF switch.
2. Read and follow the Operating Instructions,
If boiler does not start correctly
1. Check for loose connections, blown fuse or service switch
off?
2. Is external limit control (if used) open? Is boiler water
temperature above boiler limit setting?
3. Is thermostat set below room temperature?
4. Is gas turned on at meter or boiler?
5. Is incoming gas pressure less than 4” w.c.?
6. If none of the above corrects the problem, refer to Trouble-
shooting, beginning on
.
Check system and boiler after start-up
Check water piping
1. Check system piping for leaks. If found, shut down boiler
and repair immediately. (See WARNING on
re-
garding failure to repair leaks.)
2. Vent any remaining air from system using manual vents.
Air in the system will interfere with circulation and cause
heat distribution problems and noise.
Check vent piping and air piping
Check for gas-tight seal at every connection and seam of air
piping and vent piping.
Venting system must be sealed gas-tight to
prevent flue gas spillage and carbon monoxide
emissions which will result in severe personal
injury or death.
Start-up
(continued)