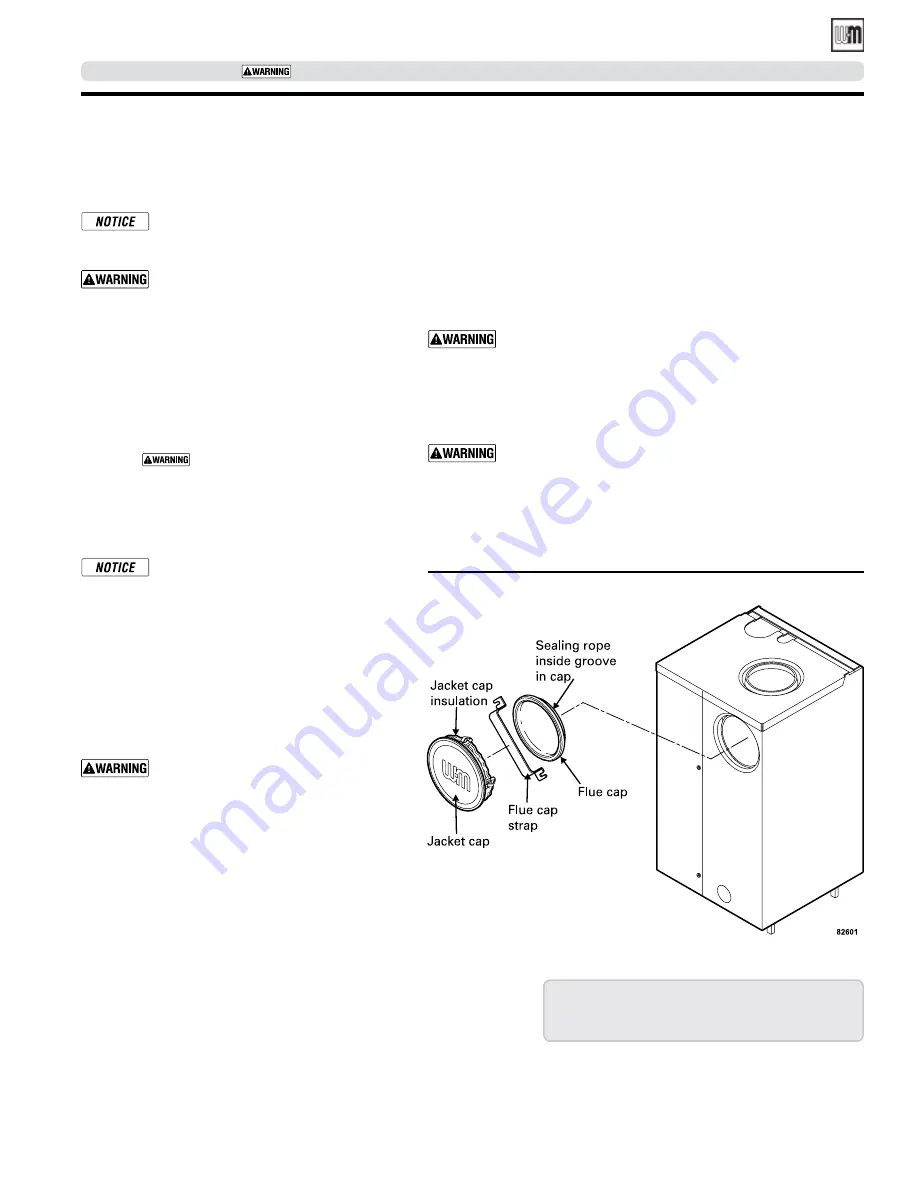
Place boiler
1. Remove boiler from pallet.
Do not drop boiler or bump jacket on
floor or pallet. Damage to boiler can
result.
Smaller sized boilers may be top heavy.
Use caution when handling to avoid
minor personal injury or property dam-
age.
2. Boiler is shipped for back flue outlet. To change to
top flue outlet (see Figure 4):
a. Remove jacket cap on top of boiler.
b. Loosen two screws holding flue cap strap to
collector hood. Remove strap and flue cap from
opening. Re-tighten screws.
c. Check rope placement inside flue cap.
(Read
under step #5 below).
d. Loosen two screws on back flue outlet. Set flue
cap on outlet. Install strap by engaging slots
in screws. Tighten screws. Make sure cap is
securely installed.
e. Snap jacket cap in back outlet opening.
Jacket cap must be in place on boiler to
avoid requiring an 18" minimum clear-
ance from back of boiler to combustible
material.
3. Check level. Shim legs, if needed.
4. Check for secure placement of insulation on target
wall, chamber floor and burner door.
5. Visually check:
a.
Flue collector hood seal.
b.
Burner mounting door seal.
Obtain gas-tight seal to prevent possible
flue gas leakage and carbon monoxide
emissions, which can lead to severe per-
sonal injury or death.
Tankless heater, if used
1. Remove tankless heater knockout in left side of
jacket panel and, for SGO-6 only, tankless heater
control knockout.
2. Remove tankless heater cover plate and gasket.
3. Install new gasket and tankless heater over studs
around opening. Secure with 3/8" nuts.
4. Install tankless heater operating control where
shown on page 23. If not furnished, use operating
control with maximum 10°F differential.
Perform hydrostatic pressure test
1. Remove steam pressure gauge furnished with boiler. Install water pres-
sure gauge for test only. Be sure gauge can handle test pressure.
2. Install air vent in tapping on top of boiler.
3. Remove pressure control and low water cutoff. Plug tappings.
4. Plug supply and return tappings.
5. Drain valve is already factory-installed.
6. Fill boiler. Vent all air. Pressure test boiler at 45-55 psig.
Do not leave boiler unattended. Cold water fill can expand
and damage cast iron, resulting in severe personal injury,
death or substantial property damage.
7. Check for maintained gauge pressure for more than 10 minutes. Visu-
ally check for leaks if gauge pressure drops.
8. Drain boiler. Repair leaks if found.
Using petroleum-based compounds to repair leaks can dam-
age system components, resulting in property damage.
9. Retest boiler after repairing leaks.
10. Remove pressure gauge, air vent and plugs. Re-install steam pressure
gauge, pressure control and low water cutoff furnished with boiler.
Figure 4
Change from back flue outlet to top flue outlet (optional)
Instructions for packaged boilers continued on
page 16.
Install boiler — packaged boilers only
Part number 550-141-829/1211
11
GOLD
SGO
OIL-FIRED NATURAL DRAFT STEAM BOILER — SERIES 3 —
Boiler Manual
SERVICE TECHNICIAN ONLY — read and follow completely.
Summary of Contents for GOLD SGO
Page 1: ......