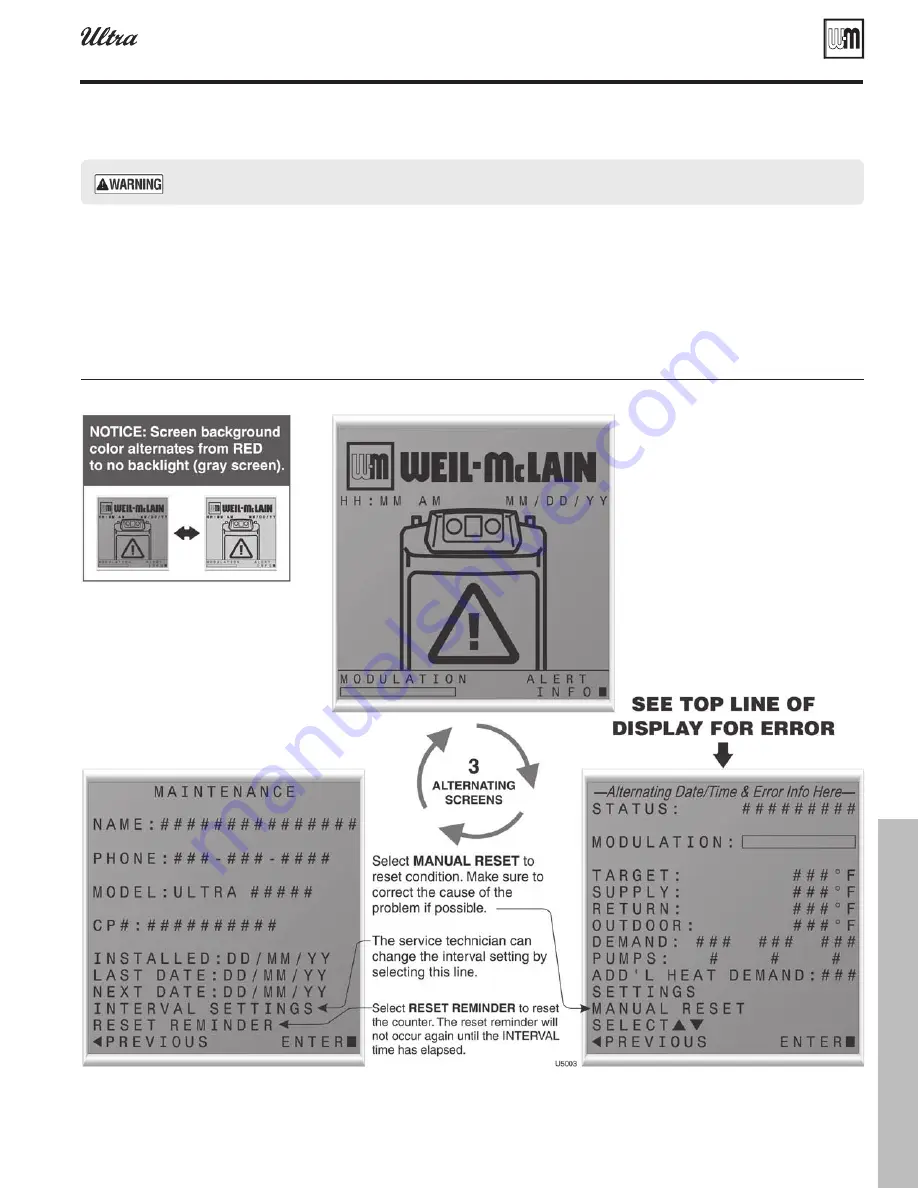
Part number 550-100-090/0809
101
gas
-
fired
water
boiler
—
Boiler Manual
MAINTENANCE & SPECIFICA
TIONS
U-Control display toggles when in lockout, with screen flashing red to gray
Figure 111
Troubleshooting
(continued)
U-Control fault indications
The U-Control provides diagnostic information for
1.
both automatic reset conditions and manual reset
conditions. See Figure 104, page 90 for information
available on the U-Control display.
2. Figure 111 shows the screen behavior during an
automatic or manual reset condition. The table
below the display illustration lists manual reset conditions and how
to reset from them.
3. Figure 112, page 102 lists conditions that will cause the control to dis-
play a constant red screen. The boiler will automatically restart if the
condition self-corrects or the technician uses the U-Control’s manual
reset screens to reset.
Make sure to determine the causes of outages. Do not leave the boiler operating without a complete diagnosis.