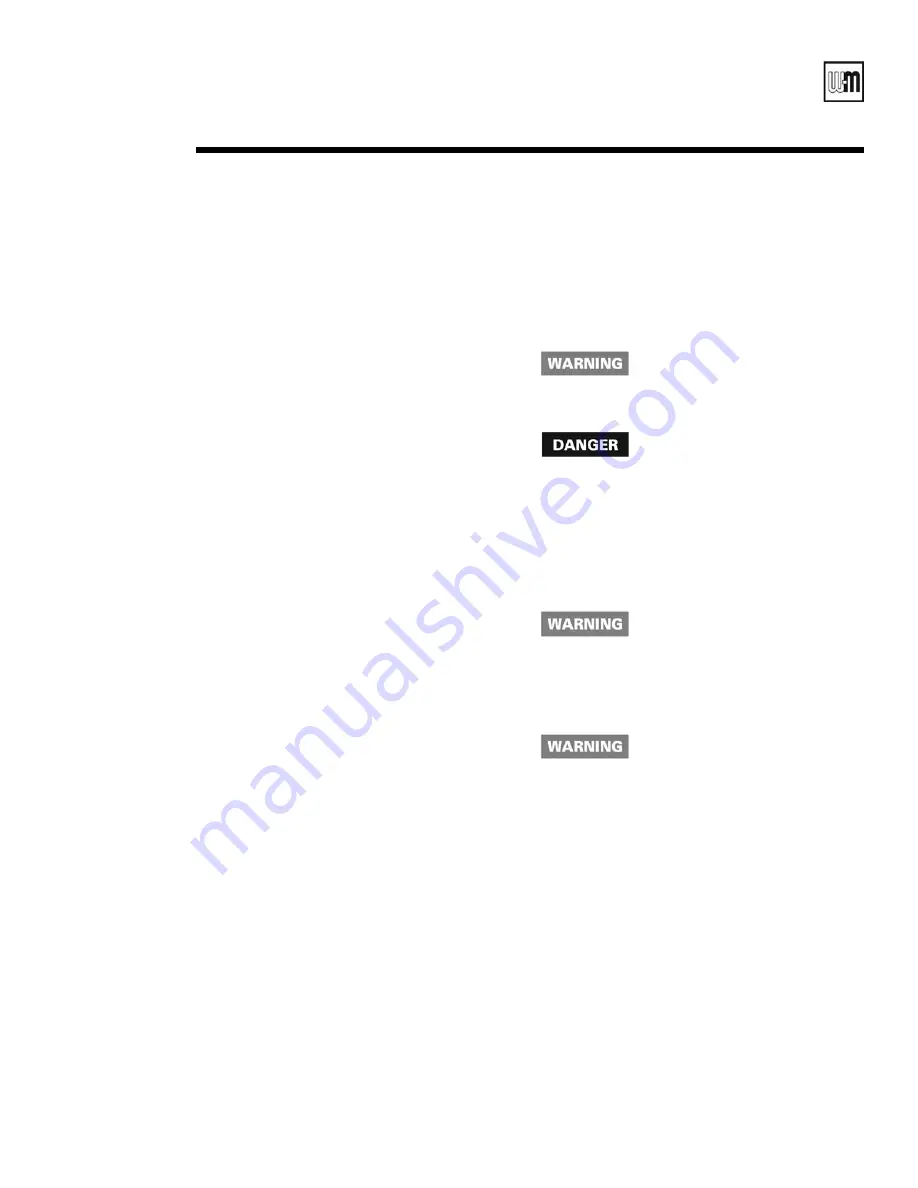
Part Number
550-110-710/0107
33
GOLD CGi Gas-Fired Water Boiler — Boiler Manual
Fill the system with water
1. Close manual and automatic
air vents
and boiler drain cock.
.
Fill to correct system pressure.
Correct pressure will vary with each
application. Typical cold water fill pressure for a residential system is
1 psi.
3.
Purge air
from system:
a. Connect a hose to the purge valve (see
drain valves
, item
6
, in
suggested piping diagrams on pages 3 through ,
Figure 18
through
Figure 23
). Route hose to an area where water can drain
and be seen.
b. Close the boiler or system isolation valve between the purge valve
and fill connection to the system.
c. Close zone isolation valves.
d. Open quick-fill valve on cold water makeup line.
e. Open purge valve.
f. One zone at a time, open the isolation valves. Allow water to run
through the zone, pushing out the air. Run until no noticeable air
flow is present. Close the zone isolation valves and proceed with
the next zone. Follow this procedure until all zones are purged.
g. Close the quick-fill water valve and purge valve and remove the
hose. Open all isolation valves. Watch that system pressure rises to
correct cold-fill pressure.
h. After the system has operated for a while, eliminate any residual
air by using the manual air vents located throughout the system.
i. If purge valves are not installed in system, open manual air vents
in system one at a time, beginning with lowest floor. Close vent
when water squirts out. Repeat with remaining vents.
4. Open
automatic air vent
(diaphragm-type or bladder-type expansion
tank systems only) one turn.
5. Open other vents:
a. Starting on the lowest floor, open air vents one at a time until
water squirts out.
b. Repeat with remaining vents.
6. Refill to correct pressure.
Inspect system water piping
After filling the boiler and system with water,
inspect all
piping
throughout the system for leaks. If found, repair
immediately. Repeat this inspection after the boiler has
been started and the system has heated up.
Leaks must be repaired at once.
Failure to do so can damage the
boiler, resulting in substantial prop-
erty damage.
Do not use
petroleum-based
cleaning or sealing compounds
in boiler system. Severe damage to
boiler will occur, resulting in sub-
stantial property damage.
Inspect base insulation
The boiler contains ceramic fiber
and fiberglass materials. Use care
when handling these materials per
instructions on
page 68
of this
manual. Failure to comply could
result in severe personal injury.
Failure to replace
damaged insu-
lation or reposition insulation can
result in a fire hazard, causing severe
personal injury, death or substantial
property damage.
Check to make sure
base insulation is secure
against
all four sides of the base. If insulation is damaged or
displaced,
do not
operate boiler. Replace or reposition
insulation.
Start-up — preparation
(continued)
7a