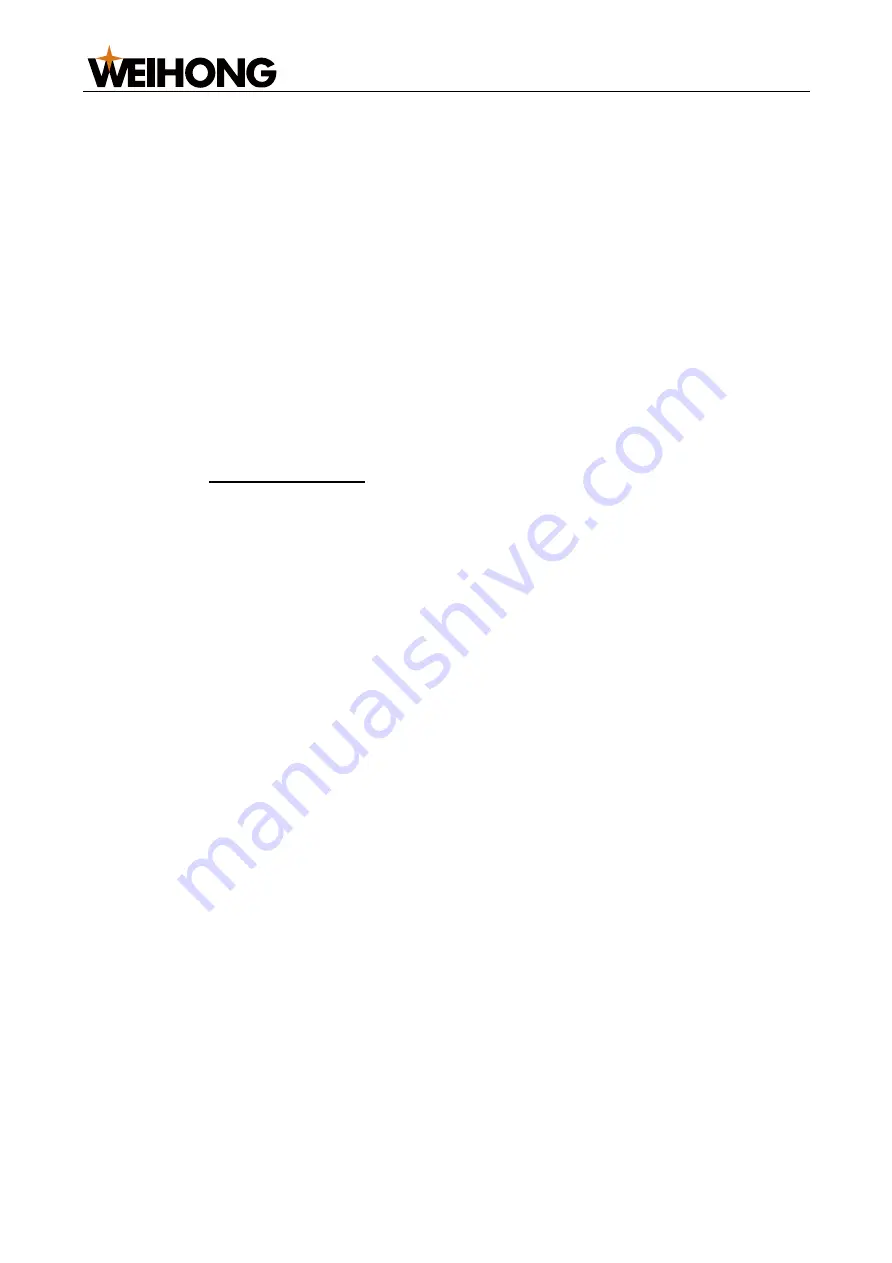
上海维宏电子科技股份有限公司
SHANGHAI WEIHONG ELECTRONIC TECHNOLOGY CO., LTD
.
57
/
116
Follow the steps below to help troubleshoot:
Modify the encoder direction parameter and see if the alarm disappears.
If not, undo the encoder direction modification and modify the axis rotation direction.
If both the axis direction and encoder direction are incorrect, reverse both the
encoder direction and axis rotation values.
4.4.9 Follow In-position Waiting Timeout
Reason
The value of
INposition Tolerance
is too small.
Calibration data error.
Influence of external slag discharge during machining.
Follow overshooting.
Solution
Follow the steps below to help troubleshoot:
Check the
INposition Tolerance
value.
The recommended value is 0.1.
Execute Execute Calibration again.
Adjust the cutting technic settings.
Check the follow parameters and drive parameter settings.
Ensure that they are set correctly.
4.4.10 Large Follow Error Alarm
Reason
Within a certain period of time, the follow error is larger than the out-of-edge tolerance
setting.
Solution
Follow the steps below to help troubleshoot:
If this alarm was reported when the material surface is quite flat, it may have been
caused by follow overshooting. In this case, check the servo drive gain value.
If the value is too small, increase it as needed.
If this alarm was reported during cutter lifting, the follow gain value may have been
too small.
4.4.11 System Reports Material Collision Alarm when Follow is Enabled in Idle Status or
During Machining
Reason
The current capacitance is equal to or smaller than the
Touch Part Capacitance
value.
Solution
Follow the steps below to help troubleshoot:
1. Set
Touch Part Capacitance
to a proper value.
It is recommended that you use the default value (0).
2. If the alarm is reported when enabling the follow function:
a. Ensure that
Pulse Equivalent
,
Feedback Pulse Count
,
Speed Gain
are set
correctly.
b. Ensure that the drive gain parameter is set correctly.
3. If the alarm is reported during machining:
a. Ensure that there is no exception under manual following.
Summary of Contents for LS6000M
Page 75: ...SHANGHAI WEIHONG ELECTRONIC TECHNOLOGY CO LTD 72 116 With brake lines 50P HD plug...
Page 76: ...SHANGHAI WEIHONG ELECTRONIC TECHNOLOGY CO LTD 73 116 Without brake lines 50P HD plug...
Page 78: ...SHANGHAI WEIHONG ELECTRONIC TECHNOLOGY CO LTD 75 116 One to two...
Page 81: ...SHANGHAI WEIHONG ELECTRONIC TECHNOLOGY CO LTD 78 116 Fuji alpha5 plus axis X Y1 Y2...
Page 83: ...SHANGHAI WEIHONG ELECTRONIC TECHNOLOGY CO LTD 80 116 Delta ASDA B...
Page 84: ...SHANGHAI WEIHONG ELECTRONIC TECHNOLOGY CO LTD 81 116 Delta ASDA B one to two...
Page 86: ...SHANGHAI WEIHONG ELECTRONIC TECHNOLOGY CO LTD 83 116 MR JE with brake cable...
Page 87: ...SHANGHAI WEIHONG ELECTRONIC TECHNOLOGY CO LTD 84 116...
Page 91: ...SHANGHAI WEIHONG ELECTRONIC TECHNOLOGY CO LTD 88 116 ESDA...
Page 93: ...SHANGHAI WEIHONG ELECTRONIC TECHNOLOGY CO LTD 90 116 R series...
Page 96: ...SHANGHAI WEIHONG ELECTRONIC TECHNOLOGY CO LTD 93 116 With brake lines 50P HD plug...
Page 97: ...SHANGHAI WEIHONG ELECTRONIC TECHNOLOGY CO LTD 94 116 Without brake lines 44P interface...
Page 105: ...SHANGHAI WEIHONG ELECTRONIC TECHNOLOGY CO LTD 102 116 Delta ASDA B2...
Page 112: ...SHANGHAI WEIHONG ELECTRONIC TECHNOLOGY CO LTD 109 116 The button definitions are shown below...
Page 114: ...SHANGHAI WEIHONG ELECTRONIC TECHNOLOGY CO LTD 111 116 The button definitions are shown below...
Page 115: ...SHANGHAI WEIHONG ELECTRONIC TECHNOLOGY CO LTD 112 116...
Page 117: ...SHANGHAI WEIHONG ELECTRONIC TECHNOLOGY CO LTD 114 116...