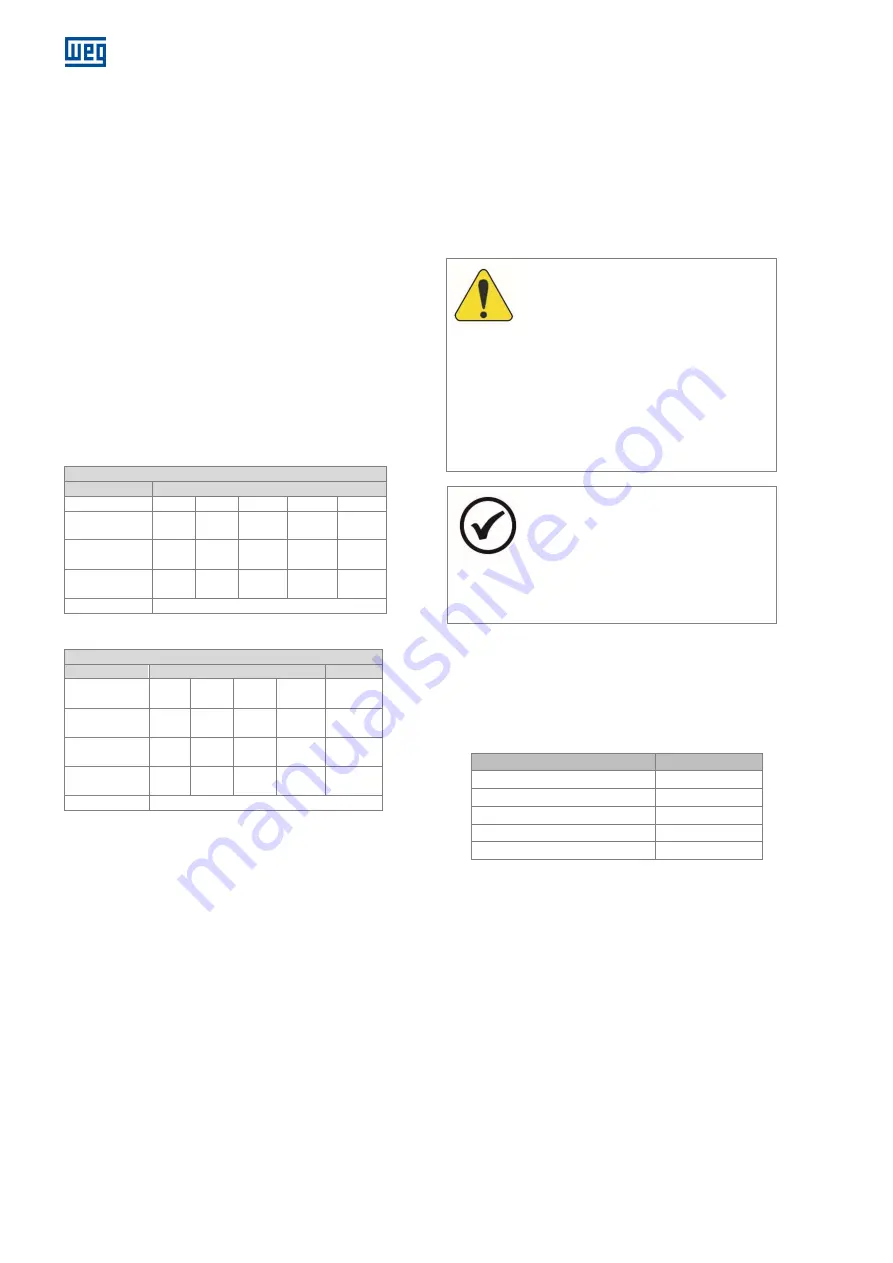
36 l
Installation, operation and maintenance manual – Squirrel cage motor – WGM20 Line 14108242
Drying oil is used to protect the motor shaft against rust
during transportation. In order to ensure the proper
operation of the grounding brush, this oil, as well as any
residue between the shaft and the brush, must be
removed before starting the motor. The brush must be
constantly monitored during operation, and it must be
replaced by another one of the same quality (granulation)
at the end of its useful life.
7.9
ENCODER MAINTENANCE
The correct installation of the encoder (if any) is very
important for its operation. Both disassembly and
assembly must be done by skilled and trained personnel,
according to the procedures contained in the specific
manual of the equipment manufacturer.
If any further explanations are necessary, consult WEG.
7.10
BEARING MAINTENANCE
7.10.1
Bearing data
Table 7.1: Bearing data: horizontal motors
Bearing data – Horizontal motors
Front and Rear
Frame
355
400
450
500
560
Rolling
Bearing
6222 6224
6228
6232
6232
Grease
quantity (g)
38
43
52,5
69,6
69,6
Lubrication
interval (h)
4500 4500
4420
3420
3420
Grease
Polirex EM 103
Table 7.2: Bearing data - vertical motors
Bearing data – Vertical motors
Front
Rear
Frame
355
400
450
500
355 to
500
Rolling
Bearing
6222 6224
6226
6232
7222
Grease
quantity (g)
41
43
46
69,6
38
Lubrication
interval (h)
4500 4500
4500
3270
2240
Grease
Polirex EM 103
7.10.2
Instructions for lubrication
The lubrication system was designed in such a way that
during the lubrication of the rolling bearings, all the old
grease is removed from the rolling bearing races and
expelled through a drain which enables the exit of the
grease, but prevents the ingress of dust or other harmful
contaminants.
This drain also prevents damage to the rolling bearings by
excessive lubrication.
It is recommended to make the lubrication with the motor
in operation in order to ensure the renewal of the grease in
the rolling bearing housing.
If that is not possible due to the presence of rotating parts
near the grease nipple (pulleys, etc.) which may put the
operator at risk, follow the procedures below:
With the motor stopped, inject approximately half of the
total intended amount of grease and operate the motor
for approximately one minute at full speed;
Stop the motor and inject the rest of the grease.
ATTENTION
The injection of all the grease with the
motor stopped may lead to the penetration
of part of the lubricant into the motor
through the internal seal of the rolling
bearing cap;
It is important to clean the grease nipples
prior to lubrication in order to prevent
foreign materials from being dragged into
the rolling bearing. For lubrication, use only
manual grease gun.
NOTE
The rolling bearing data, amount and type
of grease, and lubrication intervals are
informed in Table 7.1, Table 7.2 and on a
bearing nameplate fixed to the motor.
Check this information before performing
the lubrication.
The lubrication intervals informed consider the working
temperature of the rolling bearing of 70ºC;
Based on the operating temperature ranges listed in
Table 7.3, apply the following correction factors for the
rolling bearing lubrication intervals:
Table 7.3: Reduction factor for lubrication intervals
Bearing operating temperature Reduction factor
Below 60 ºC
1.59
Between 70 and 80 ºC
0.63
Between 80 and 90 ºC
0.40
Between 90 and 100 ºC
0.25
Between 100 and 110 ºC
0.16
7.10.3
Procedures for bearing lubrication
1.
Clean with a cotton cloth around the hole of the
grease nipple;
2.
With the rotor operating, inject the grease with a
manual grease gun until grease starts coming out from
the drain or until the proper amount of grease,
informed in Table 7.1 and Table 7.2 has been injected.
3.
Keep the motor running long enough so that the
grease excess passes through the drain;
4.
Inspect the bearing temperature to make sure there
was no significant change;