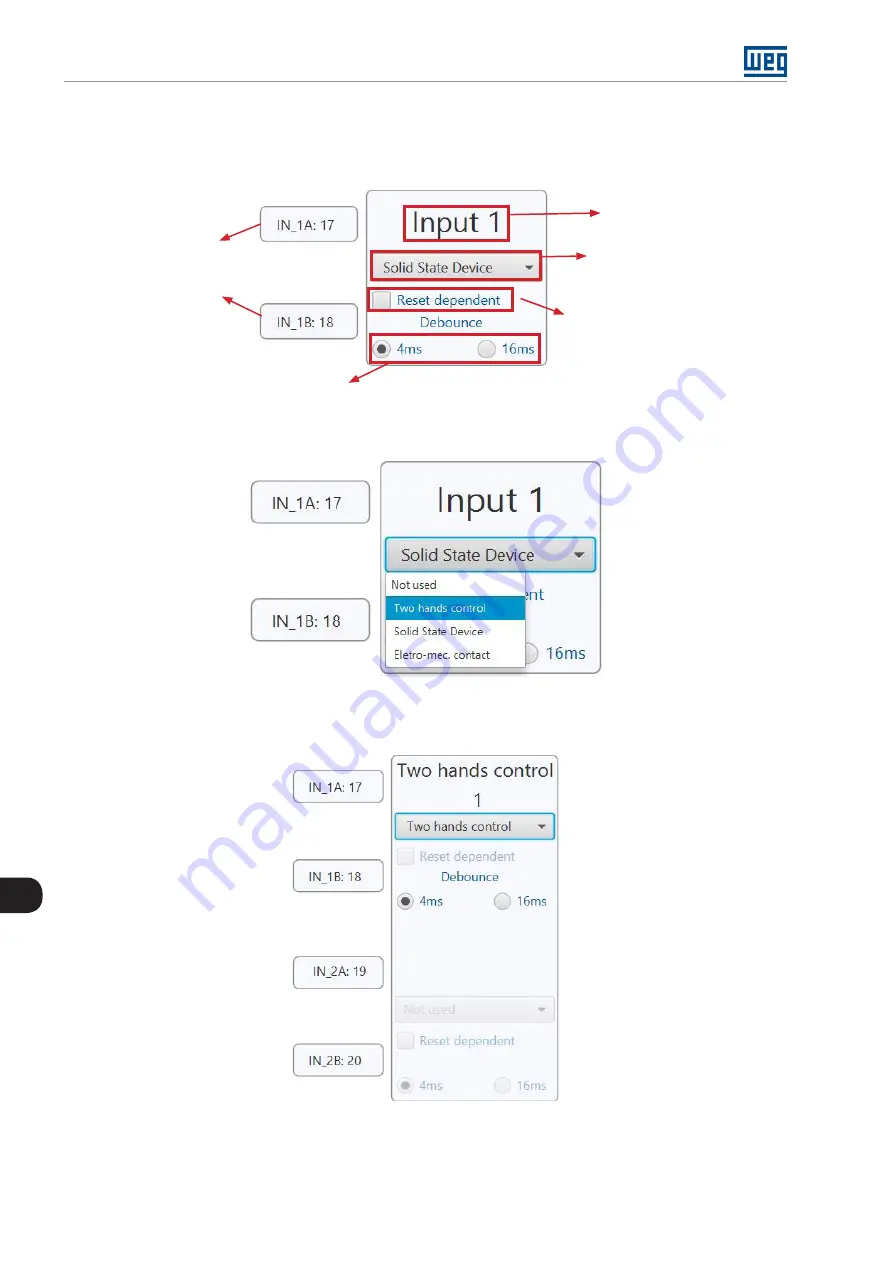
9
Programming With WPS
9-12 | PSRW
9.5.1 Configuring the Inputs
The component block used to configure the inputs is described below.
De-bounce: it selects a time filter to prevent
contacts bouncing being interpreted as
input activation.
Physical terminal
names – same
names present in
PSWR label.
Input type:
it selects
what kind of device will be
connected on PSRW input.
Input name
Reset dependent:
It
defines whether the input
depends on a manual
reset or is automatic. For
manual reset, this option
must be selected
The options for Input type combo-box are:
If the input type is “Two hands control”, the block changes to a big one containing the next block, as the figure
bellow shows.
The two hands control type is only allowed between inputs 1 and 2 or between inputs 3 and 4. For this option, the
reset option remains disabled for automatic reset of the two-hand control.
Summary of Contents for PSRW
Page 2: ......
Page 3: ...User s Manual Series PSRW Language English Document 10005909449 01 Publication Date 05 2019...
Page 10: ...Introduction 1 4 PSRW 1...
Page 12: ...Description 2 2 PSRW 2...
Page 18: ...Operation Diagram 4 2 PSRW 4...
Page 24: ...Signals 5 6 PSRW 5...
Page 28: ...Diagnosis 7 2 PSRW 7...
Page 34: ...Connection Examples 8 6 PSRW 8...
Page 56: ...Product Use With Safety 10 2 PSRW 10...
Page 58: ...11 Modifications 11 2 PSRW...
Page 59: ...Declaration Of Conformity PSRW 12 1 12 12 DECLARATION OF CONFORMITY...