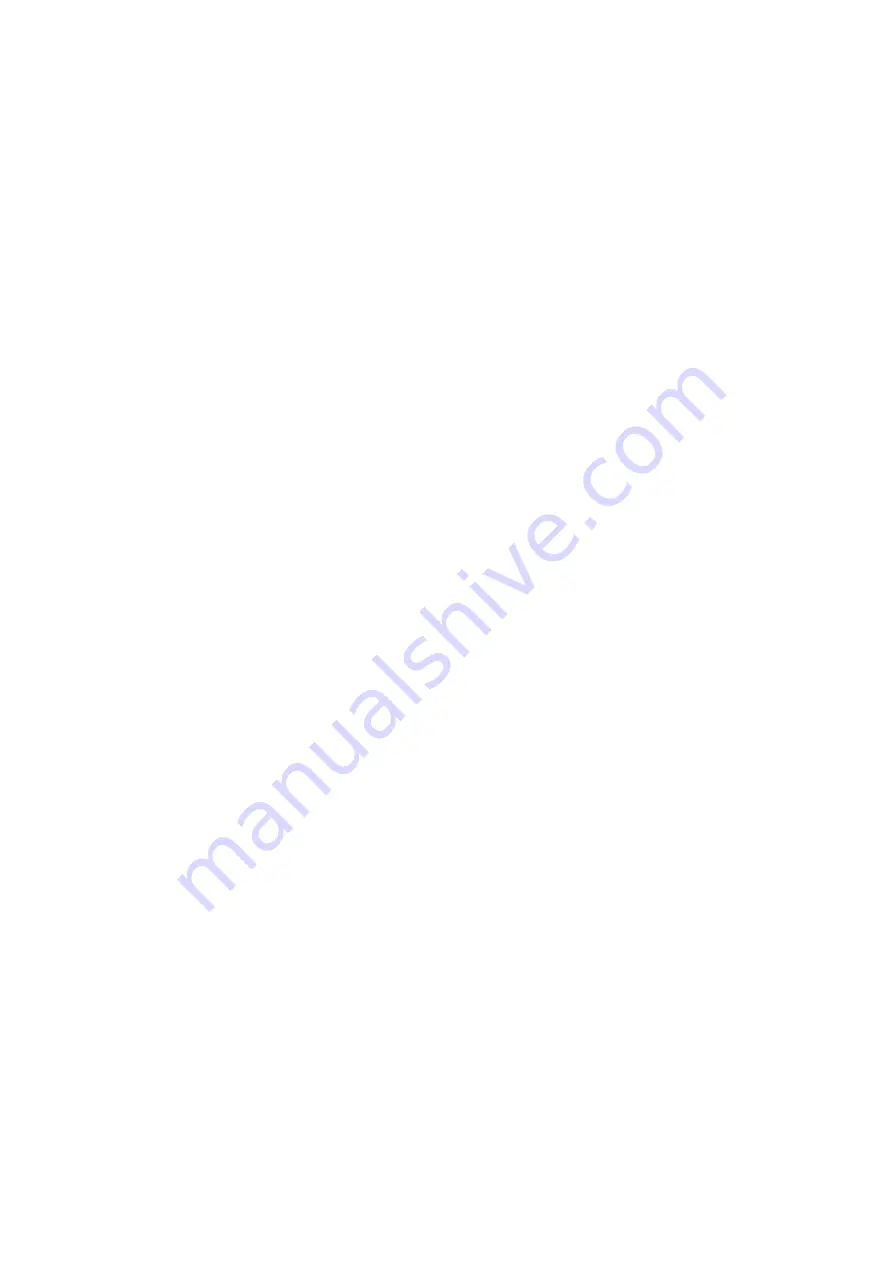
10
When coming into contact with fuels, the rubber-bonded metal
buffers of the machine may become damaged or ineffective.
Therefore, wipe spilled fuel carefully off the rubber-bonded
metal buffers.
Fuel vapors are easily flammable. Do not smoke and keep
away from open fire while refueling the machine.
The machine must not be fueled unless the engine is switched
off.
Cleaning work
Use clear water for cleaning. Do not use flammable solvents.
The vapors of the solvents may ignite upon contact with hot
components or other sparks.
Perform cleaning tasks only in rooms that are suitable and
have been approved for that purpose. Residual oil and
lubricants that may have been rinsed off have a negative
impact on the environment and must be collected by suitable
means (e.g. oil separator).
Safe handling of combustion
engines
Combustion engines pose a particular risk during operation.
Their exhaust emissions contain carbon monoxide, a colorless
and odorless gas that is extremely hazardous, which, if inhaled
even briefly, can cause unconsciousness and death.
Therefore, never inhale the exhaust gas.
Inspection
The machine must be inspected in accordance with the
corresponding implementation conditions and operating
conditions to ensure its operationally safe status. This
inspection should be performed as needed by an expert
- however, no less than once a year. The findings of the
inspection must be stored in writing until the time of the next
inspection.