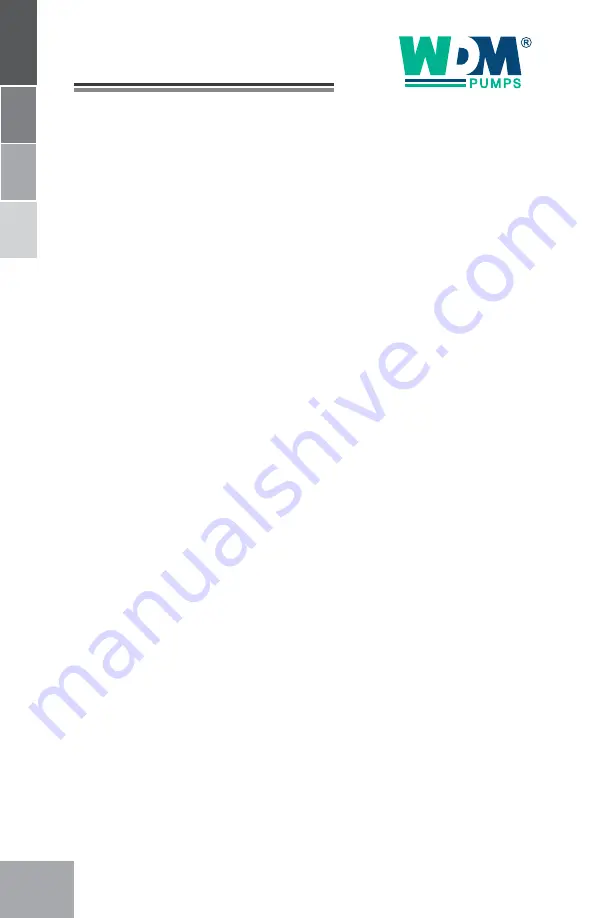
Operation Manual.
4
•
The pump should not be operated without the proper safety
devices in place. If such devices are removed during service
and repair work, make sure they are replaced before
operating the pump again.
•
Do not operate the pump when holding the cable assembly.
•
Blocking or restricting the discharge hose may cause it to
whip under the pressure.
•
Do not remove the drain plugs or valves if the pump is
operating.
•
The pump should be isolated from a pressurized system
before it is removed.
•
Allow pumps time to cool sufficiently before handling or
servicing them as heat and pressure build up inside during
operation.
•
Never apply heat in disassembling a pump as doing so could
cause an explosion.
•
Do not exceed manufacturer’s recommendation for maximum
performance, as doing so could cause the motor to overheat.
•
If the discharge valve is closed, do not continue operating the
pump. Doing so will decrease the life expectancy of the
bearings and mechanical seal. Also, the extreme heat from
doing so can cause steam to build up creating a dangerous
pressure situation. A temperature or pressure relief valve
should be installed on the pump body.
3.
Installation.
Location.
•
Place the pump as close to the suction source as
possible. Suction piping should be as short and direct as
possible.
•
Place the pump below the water level whenever possible.
This will facilitate priming, ensures a constant flow of liquid,
and provides a positive suction.
•
Make sure the NPSH (Net Positive Suction Head) is
accounted for at the suction end of pump relative to the
whole system. Available NPSH must always exceed the
required NPSH specified in the yield curve specifications of
the pump.