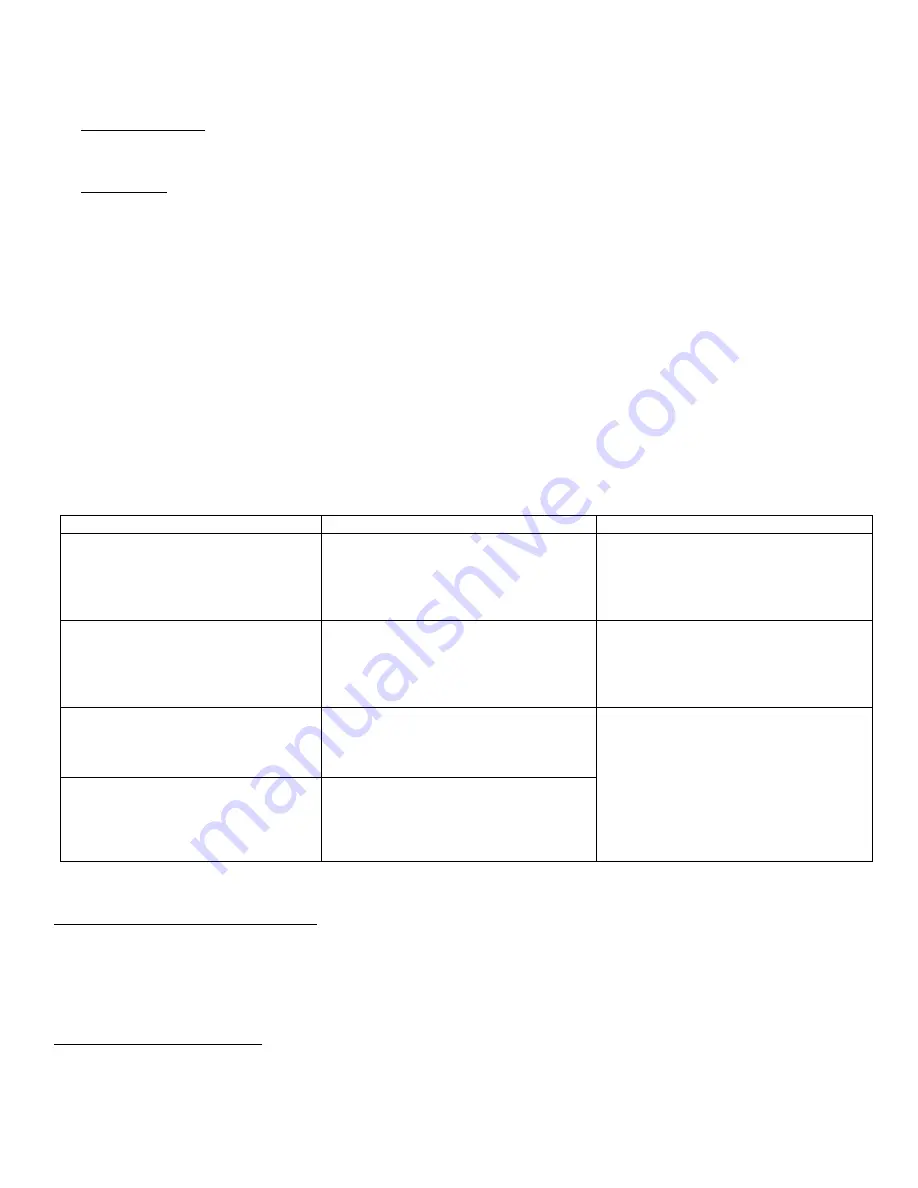
31
voltage, it should be replaced. If the voltage is not present at Terminals PV1 and ground (or across valve), the control should be
replaced.
5.
Electrode Placement
a. Electrode should be placed so optimum flame current is achieved for proper application.
b. Flame should not impinge on any portion of ceramic insulator.
6.
Flame Current
The flame detector circuit uses the ionized gas flame to conduct the flame signal. This signal is a small DC current which ca n be
measured directly with a 0 to 50 microamp meter.
Although the minimum flame current necessary to keep the control from going into lockout is 0.8 ,microamps, the lowest
recommended is 1.5 microamps.
To measure flame current, first shut off the power to the system and then connect a DC micro amp meter to the FC+ and FC-
terminals. Energize the ignitor. If the meter reads below zero, shut the system off and reverse the meter leads.
Once the flame is established, assure that the flame current is above the minimum specified. If not, assure that the system h as the
proper input voltage, and then adjust the pilot line gas pressure until flame current is increased.
Once the flame is has been established and the system is in its heat cycle, occasional sparking may occur. This is common in some
installations and is not significant. Sparking will not damage the ignitor.
Table 9: Service Hints
What’s Wrong
Why
What To Do
1.
Lockout occurs 3-10 seconds
after ignition.
1.
Reverse polarity.
2.
System improperly grounded.
3.
Gas pressure too high, causing
flame to lift off burner.
See Input Polarity (See 1)
See Improperly Grounding (See 2)
Check to ensure input pressure as
specified on manufacturer’s data plate.
See Flame Current (See 6)
2.
Flame not established. Arcing to
ground.
3.
No spark.
4.
Arcing other than across gap.
1.
Sensor probe incorrectly
positioned in flame pattern. Spark
gap too small. Spark too large.
Corroded connector.
2.
Cracked or dirty insulator.
See Inoperative High Voltage (See 3a)
5.
Weak spark.
1.
Broken high voltage lead. High
voltage lead too close to metal
surface. Valve malfunction.
Electrode improperly placed.
See Valve Malfunction (See 4)
See Electrode Placement (See 5)
See Flame Current (See 6)
Check to ensure that manifold
pressure meets manufacturer’s
specifications
No flame.
Low flame current and/or nuisance
lockouts.
1.
Flame current falls below 0.8 µa.
2.
Low gas pressure.
COMPONENT TROUBLESHOOTING AND DIAGNOSIS
24 VOLT TRANSFORMER MALFUNCTION
The 24 volt transformer has a 115 volt primary side with a 24 volt secondary circuit. To check the transformer, simply apply
115 volts to the black and white leads. If the transformer is working correctly, 24 volts will be present across the two yell ow
leads. If the multimeter does not register 24 volts then the transformer needs to be replaced. The transformer will not function
unless 115 volts are present across L1 and neutral.
COMBUSTION FAN ENDSWITCH
The 115 volt motor is equipped with a centrifugal endswitch. The purpose of the endswitch is to ensure that the combustion
fan motor has reached the proper operating RPM which is generally about 3400 rpm. If the endswitch fails to close then the 24
volt circuit to the gas primary is interrupted and the gas valve will not open. If the blower motor has 115 volts applied but is not
rotating then the motor assembly must be replaced. Lastly if the motor is not rotating, the centrifugal switch will not make and
24 volts will not be present at the gas primary control.
Summary of Contents for P250 series
Page 35: ...35 FIGURE 23 WIRING DIAGRAMS FOR GAS BURNER WITH DIRECT IGNITION FENWAL...
Page 36: ...36 FIGURE 24 WIRING DIAGRAMS FOR GAS BURNER WITH ELECTRONIC PILOT HONEYWELL...
Page 37: ...37 FIGURE 25 WIRING DIAGRAMS FOR GAS BURNER WITH ELECTRONIC PILOT NO T STAT...
Page 38: ...38 FIGURE 26 WIRING DIAGRAMS FOR GAS BURNER WITH ELECTRONIC PILOT FENWAL...
Page 46: ...46 NOTES...