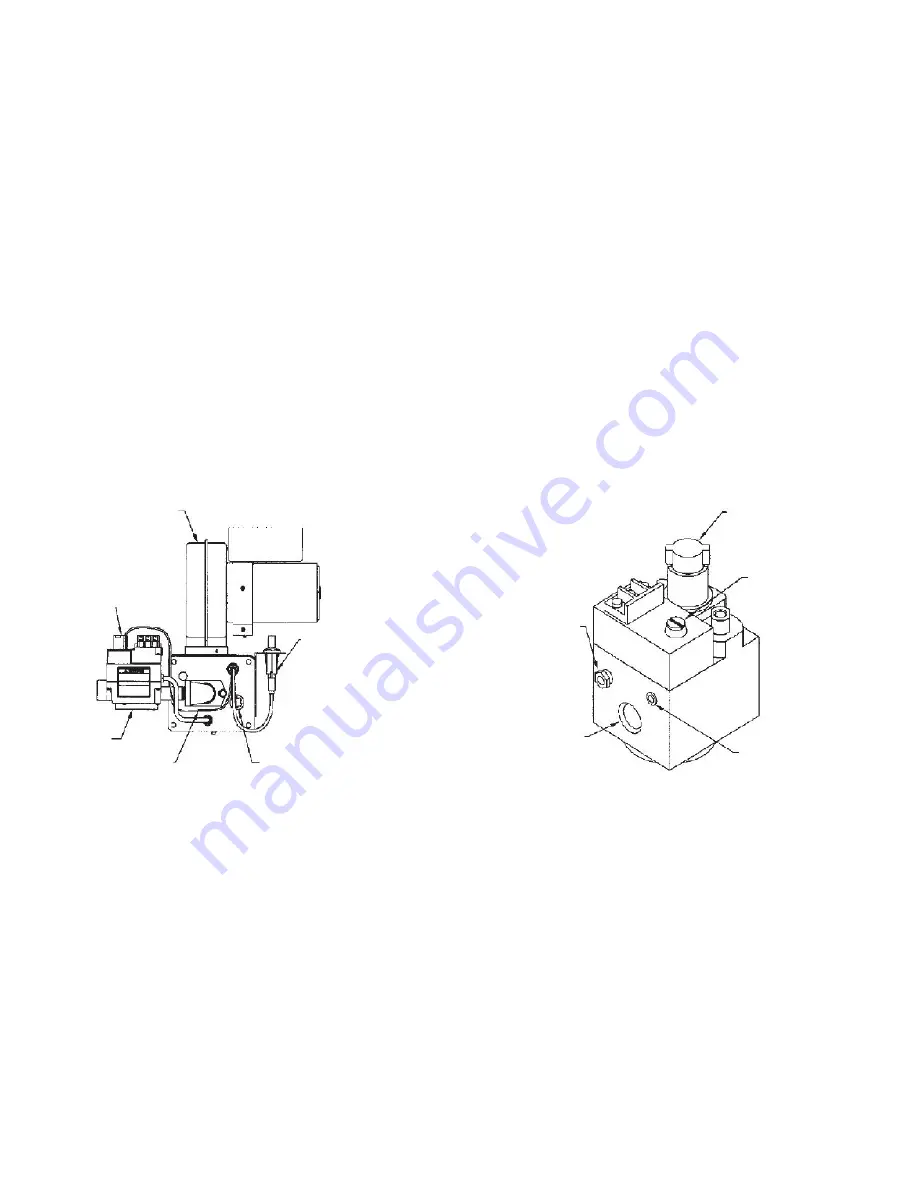
22
OPERATION OF BURNER (STANDING PILOT)
Starting the Burner:
1.
Depress the gas valve control knob on the combination gas valve and turn to “OFF” (See Figure 15).
2.
Set room thermostat above room temperature and let burner run five minutes to purge the appliance.
3.
Set thermostat below room temperature.
4.
Turn gas valve control to “PILOT”.
5.
Depress red button on valve to start pilot gas flow.
6.
Push red button down on spark igniter until it snaps. Repeat this until the pilot lights. Note: this may take some time until all the
air is “bled” out of the line. The pilot can be seen by looking through the sight glass.
7.
Hold the red button on the valve for 60 seconds, then release.
8.
Observe pilot – if not lit, SHUT OFF BURNER COMPLETELY AND WAIT 5 MINUTES. Repeat steps 1 through 7.
9.
Turn gas control valves to “ON”.
10.
Set room thermostat higher than room temperature so that the burner will start.
To put burner out of operation
1.
Depress the gas valve control knob on the combination gas valve and turn to “OFF”.
2.
Turn off electrical supply.
FIGURE 15
Combination Gas Valve
Standing Pilot
Burner
Motor/Blower
Assembly
Control Knob
Thermocouple
Gas Valve
Sight Glass
Spark Ignitor
Control Knob
Regulator
Adjusting Cover
Screw
Pressure Tap
Gas Outlet
Pilot Gas Outlet
Summary of Contents for P250 series
Page 35: ...35 FIGURE 23 WIRING DIAGRAMS FOR GAS BURNER WITH DIRECT IGNITION FENWAL...
Page 36: ...36 FIGURE 24 WIRING DIAGRAMS FOR GAS BURNER WITH ELECTRONIC PILOT HONEYWELL...
Page 37: ...37 FIGURE 25 WIRING DIAGRAMS FOR GAS BURNER WITH ELECTRONIC PILOT NO T STAT...
Page 38: ...38 FIGURE 26 WIRING DIAGRAMS FOR GAS BURNER WITH ELECTRONIC PILOT FENWAL...
Page 46: ...46 NOTES...