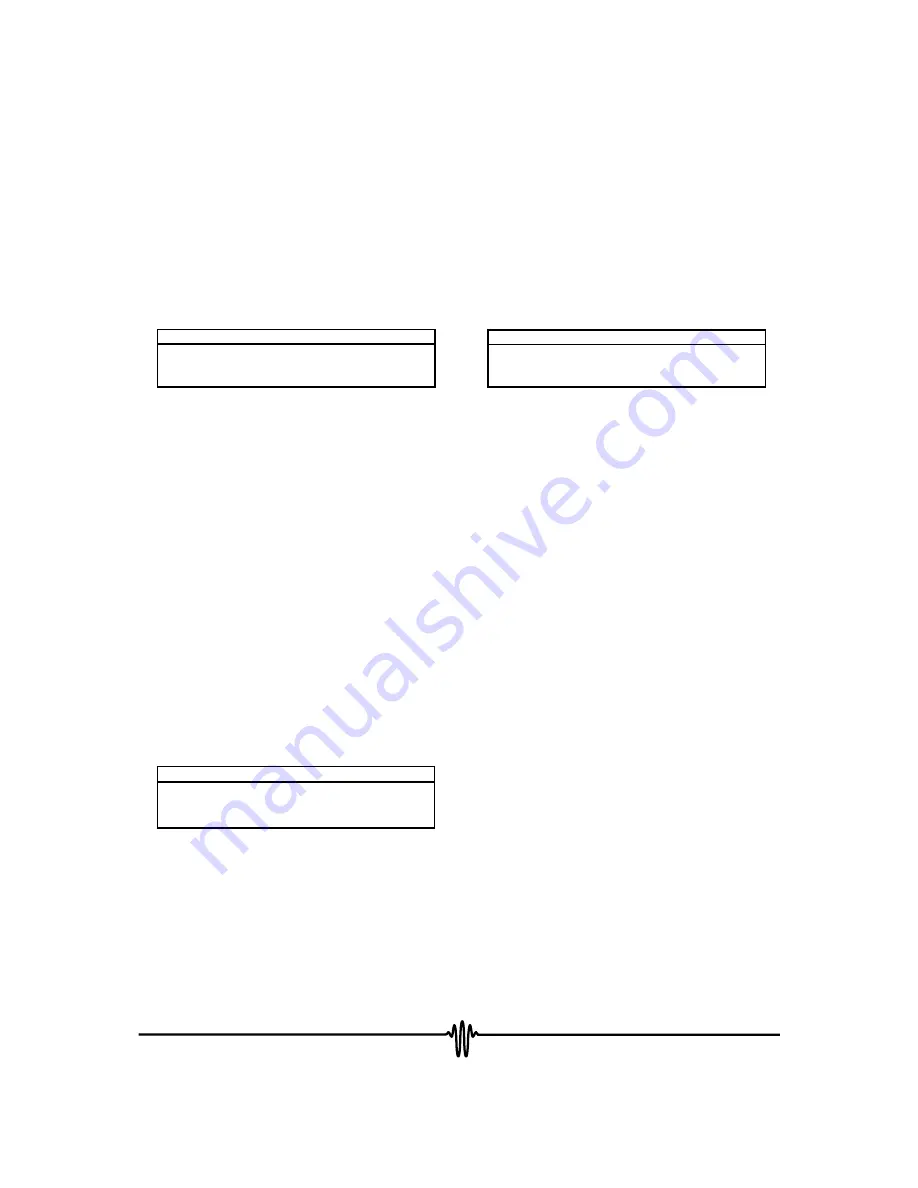
PLD-200 / PLD-500 / PLD-5000
13
____________________________
Operating Procedures for Type C laser diodes
______________ Constant Current Mode
With the Output Disabled:
(1) Configure Mode Switch to I.
[switch on top of PLD]
(2) Set Limit Current:
Monitor pins 5 & 6, adjust Current
Limit trimpot clockwise until the voltage at pin 5
corresponds to the desired voltage.
NOTE:
Current limit needs to be set 0.2 V above desired limit
level.
Limit Current and I Monitor Transfer Functions
PLD-200
80 mA/Volt
PLD-500
200 mA/Volt
PLD-5000
2 Amp/Volt
Once Current Limit is detected, the output will turn off and
the LIM I led will illuminate red. The LIM I Status voltage
and LIM I LED will stay on until the LD Enable is toggled
off then on, and the error no longer exists.
(3) Set Operating Current.
Use the transfer function
from step 2 to calculate the desired current. Monitor
pins 7 & 6. With the OUTPUT ADJUST trimpot fully CCW,
enable the output. Slowly adjust the OUTPUT ADJUST
trimpot CW until the desired voltage is measured at
pin 7.
(4) Monitor the Photodiode (optional).
If the Photo-
diode is connected to the laser diode, monitor pins 8 &
6. The PD switch on top of the PLD should be set to
L
:
L = 200
µ
A / V
(5) Analog Input:
This input is designed for analog signals
only and should not be used with TTL signals. You can
either input a DC voltage for remote current setpoint
control or use this input to modulate the laser diode.
This input sums directly with the output adjust trimpot.
The input transfer function will depend on the PLD model
in use.
Model
Transfer Function
PLD-200
40 mA / Volt
PLD-500
100 mA / Volt
PLD-5000
1 Amp / Volt
________________ Constant Power Mode
With the Output Disabled:
(1) Configure Mode Switch to P.
[switch on top of
PLD]
(2) Set Limit Current:
Monitor pins 5 & 6, adjust Current
Limit trimpot clockwise until the voltage at pin 5
corresponds to the desired voltage.
NOTE:
Current limit needs to be set 0.2 V above desired limit
level.
Limit Current and I Monitor Transfer Functions
PLD-200
80mA/Volt
PLD-500
200mA/Volt
PLD-5000
2 Amp/Volt
Once Current Limit is detected, the output will turn off
and the LIM I led will illuminate red. The LIM I Status
voltage and LIM I LED will stay on until the LD Enable
is toggled off then on and the error no longer exists.
(3)
Set the output power.
Determine the photodiode current (I
M
at operating
current
I
OP
) from data provided with your laser
diode. Monitor pins 8 & 6. One photodiode range
is available. Set the PD Range Switch to
L
.
L Range = 15 - 500
µµµµµ
A
With the OUTPUT ADJUST trimpot fully CCW,
enable the output. When the laser reaches
threshold, the photodiode current changes
abruptly and rises quickly. Adjust the
OUTPUT
ADJUST
trimpot slowly until the voltage at pin 8
corresponds to the desired photodiode current.
The transfer function is:
L = 200
µµµµµ
A / V
This can be adjusted with a resistor (R)
connected between PD Cathode (Pin 15) and
AUX V+ (Pin 1). The new range can be
calculated with:
RANGE = 2.5 V / (R || 5 k
Ω
) [
µ
A]
The new transfer function is:
1 / (R || 5 k
Ω
) [
µ
A / V]
For example, a 500
Ω
resistor across pins 15 and 2
converts the RANGE to:
2.5 / (500 * 5000 / (500 + 5000)) = 5500
µ
A max
and the transfer function to:
1 / (500 * 5000 / (500 + 5000)) = 2.2 mA / V
(4) Analog Input
This input is designed for analog
signals only and should not be used with TTL signals.
You can either input a DC voltage for remote power
setpoint or use this input to modulate the laser diode.
This input sums directly with the output adjust trimpot.
The input transfer function is
100
µµµµµ
A / V
for all
models. Note that the transfer function will change
if you change the photodiode RANGE. The new
transfer function is RANGE / 5 V