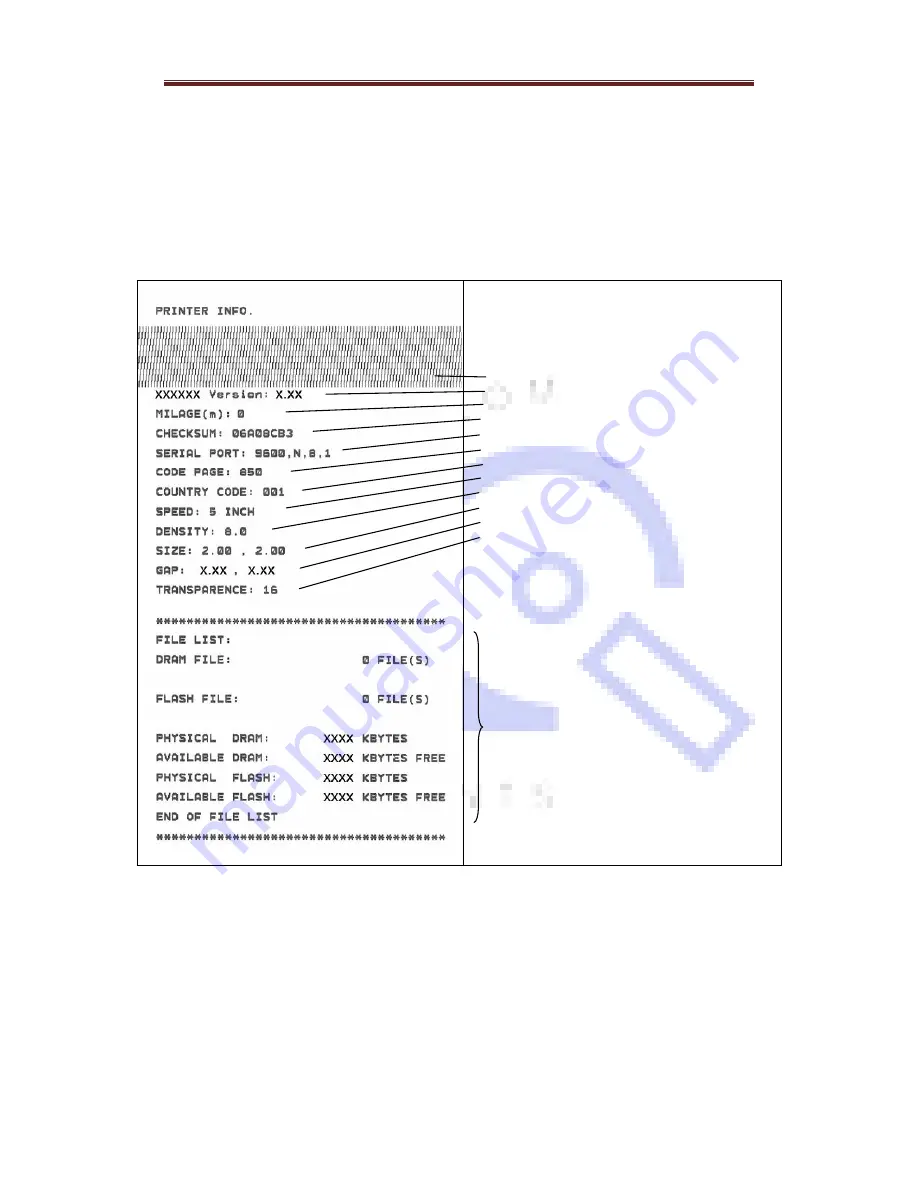
Wavecom Instruments Thermal Transfer Bar Code Printer User Manual
16
Self-test
Printer will print the printer configuration after
gap/black mark sensor calibration. Self-test
printout can be used to check if there is any dot damage on the heater element, printer
configurations and available memory space.
Print head test pattern
Printer model name & Main board firmware version
Printed mileage
Main board firmware checksum
Serial port setting
Code page
Country code
Print speed
Print darkness
Label size (width, height)
Gap size (vertical gap, offset)
Sensor sensitivity
File management information