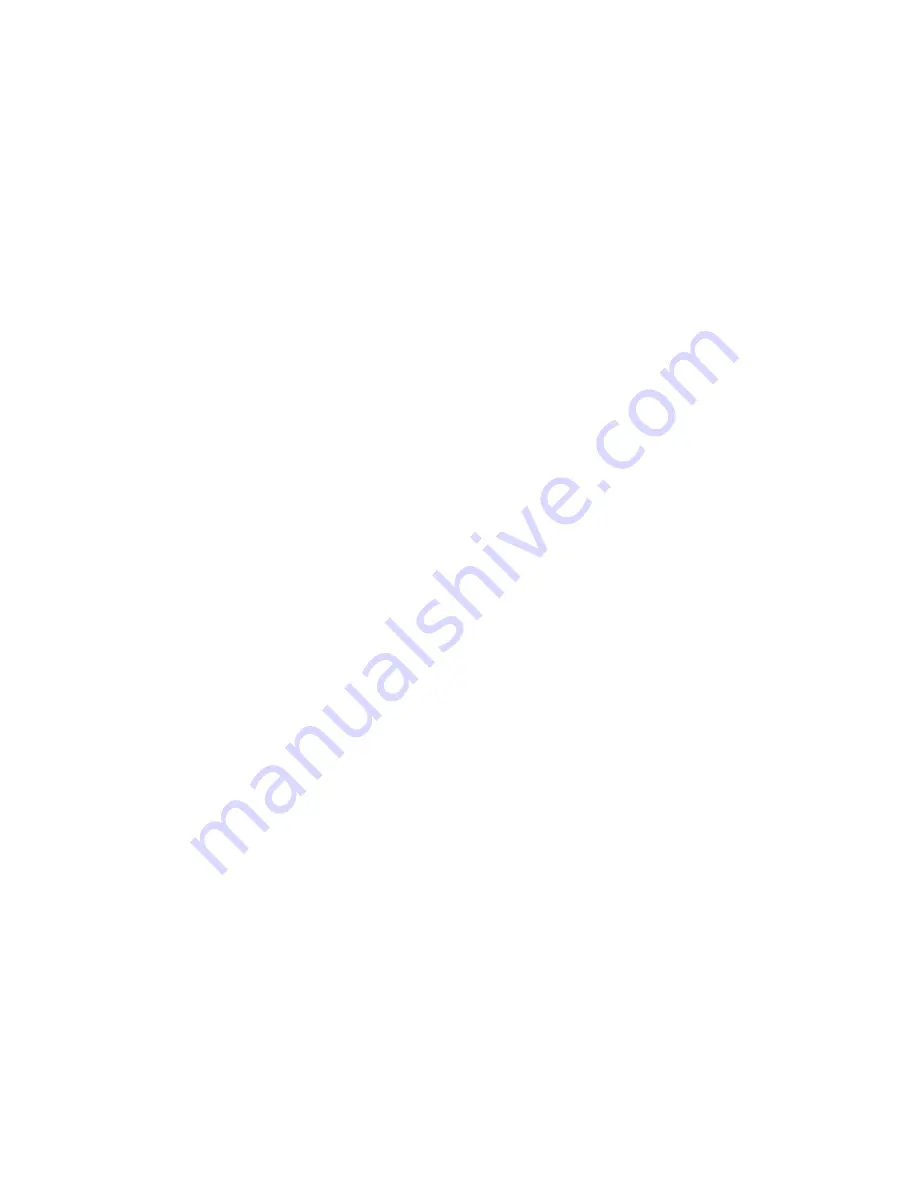
III. OPERATION
A. INSTALLATION
1.
Proper pretreatment must be determined and installed prior to the RO system.
2.
The water supply and pretreatment equipment should be sufficient to provide a
minimum of 10-psig at the maximum feed flow.
3.
An electrical receptacle with a ground fault interrupt (GFI) is highly recommended.
4.
Responsibility for meeting local electrical and plumbing codes lies with the owner /
operator.
5.
Install indoors in an area protected from freezing. Space allowances for the removal
of the membranes from the pressure vessels should be provided.
B. PLUMBING CONNECTIONS
Note: It is the responsibility of the end user to ensure that the installation is done according to
local codes and regulations.
1.
Connect the pretreated feed water line to the inlet valve (Figure # 1 item J). A feed
water shutoff valve should be located within 10 feet of the system.
2.
Temporarily connect the product water outlet to a drain. (The product outlet is
located below the product pressure switch, or on top of the product flow meter,
depending on how the unit is equipped.) The product water line should never be
restricted. Membrane and/or system damage may occur if the product line is blocked.
3.
Connect the reject water outlet to a drain. (The reject outlet is located at the reject
needle valve, or on top of the product flow meter, depending on how the unit is
equipped). The reject drain line should never be restricted. Membrane and/or system
damage may occur if the reject drain line is blocked. An air gap must be located
between the end of the drain line and the drain. The use of a standpipe or other open
drain satisfies most state and local codes and allows for visual inspection and
sampling.
4.
If a bladder tank is used for product water storage then the product pressure switch
(Figure #1 item B) needs to be connected. Install a tee and tube fitting in the inlet
piping of the bladder tank and connect the tank to the pressure switch using poly
tubing. A check valve should be installed between the RO unit and this tee.
C. ELECTRICAL
Note: It is the responsibility of the end user to ensure that the installation is done according to
local codes and regulations.
1.
Make sure the on / off switch is in the off position (Figure # 1 item A).
2.
Plug the unit into a standard 120 volt 3 prong outlet. An outlet protected with a
ground fault interrupt (GFI) is recommended.
Summary of Contents for R12-0150
Page 1: ...REVERSE OSMOSIS INSTALLATION AND OPERATION MANUAL R12 Wall Mount...
Page 2: ......
Page 8: ...Figure 1...